A few years ago, the German tycoon in the beverage industry, Gerolsteiner decided to implement one of the most modern logistics solutions. A fully automated, compact warehouse with a channel storage was to significantly improve the storage, but also to prepare the goods for the shipment.
Mobile racks, channel and standard storage systems or shuttle systems – those are the solutions usually used by the beverage industry. From the performance point of view, the most important are automated solutions. Certain activities are carried out using robots, an automated picking system is used, and companies use automated palletizing and depalletizing.
Some of these solutions were introduced in the Gerolsteiner automated facility. The storage system is based on the Schäfer Lift & Run – System. It is a solution for handling pallets in channel storage. It is usually used for feed-in and retrieval of the pallets, supporting rack systems up to 8m high (can handle 2 to 4 rack levels per axis).
Among the key advantages are high dynamics, low space demand and efficient use of energy. The system also increases product availability, delivery efficiency and quality of service, higher throughput.
Channel storage – WAMAS and Orbiter
An important element of the system used in Gerolsteiner is Orbiter and intelligent management system, WAMAS. Generally speaking, the Orbiter shuttle is responsible for putting the pallets in the channel storage space and picking them up from there.
Unlike conventional stackers, Orbiter shuttle vehicle runs on two rails and therefore doesn’t need upper guiding rails. The use of several devices one above the other allows you to handle very high shelves (up to 45 m).
Orbiter provides automated pallet support in channel storage. The channel transport shuttle (also known as the shuttle truck) works with the docking station.
Racks in which the shuttle operates have a centring console fitted onto the front.
The centring console prevents damage
The operation of the system starts with the placement of the docking station in the centring console of the desired rack. The centring console guarantees that the Orbiter is correctly positioned preventing material damage and saving time while feeding the load. This advantage is particularly evident in the case of higher levels of shelves, giving maximum confidence and safety to operators. The Orbiter trolley, which transports it into the channel to the docking station, transports it to the nearest free storage space in the channel.
Pallet support in a channel storage is possible in the FILO and FIFO schemes. In the case of the FILO model (First in-Last Out – the first entered, last exited) the pallets are entered into the warehouse and taken from only one side. In the case of the FIFO model (First In-First Out – first in, first out), pallets entered into the storage on one side are taken from the opposite side.
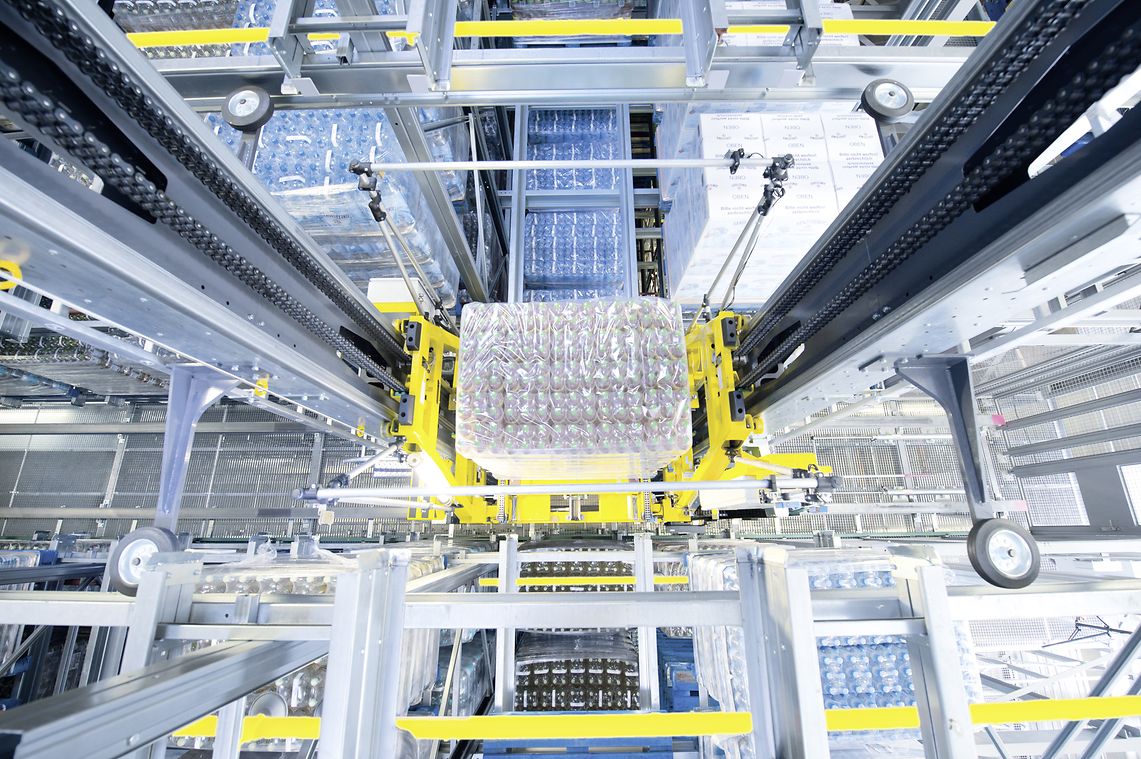
Photo: Schäfer
When the Orbiter shuttle moves the pallet to the warehouse location, the forklift can drive the next pallet, which is to be the next one introduced into the channel. This means saving time. The system allows you to handle over 100 different types of pallets.
The swinging system is powered by patented Power Caps modules (drive powered by capacitors) or accumulators. The transit instructions are sent to the trolley wirelessly using the remote control. After completing the task, the shuttle is automatically returned to the docking station.
The WAMAS logistics software controls the processes performed by the Lift & Run system. It includes entering goods to the warehouse and downloading them from there, controlling loading and managing stock levels and stocks. It also manages material flows and internal transport.
The warehouse has six aisles and approx. 19,000. storage locations.
Photo: Schäfer