The industry and logistics 4.0 covers the entire chain, from placing an order and delivering the components to the shipment of goods to customers and after-sale services. The modern tools support the employees by providing access to basically all useful information at any time in any place. The companies that introduce such innovative solutions may lower the costs, gaining a competitive advantage over the rivals.
The integration of the systems and people in the industry and logistics 4.0 is possible thanks to the internet and IT technologies. The purpose is, among others, easy identification and information flow in a vertical order: from particular elements to the IT system and backwards. The data flow takes place also in a horizontal order – it includes the machines involved in the process, which also communicate information to each other.
The management of Wabco, among others, knows about it. It is a global supplier of components and subcomponents (mainly in the safety area) for heavy goods vehicles, who decided to implement a solution that optimises work in the warehouse, as well as loading and unloading of goods. The system created especially for Wabco consists of three modules connected to each other.
Logistics 4.0 in the warehouse
The first of them covers the ramp and the warehouse. There are sensors in the warehouse that transmit the information on filling the particular pallet place to the system. The internal transport operators see the data also on the screens suspended over the ramps and on the terminal each vehicle is equipped with. Additionally, the places with fast rotation, on the edges of the shelves, a light signalling was placed, which simplifies work and helps the operator ensure if the particular place is free or taken.
The element of the module is a network solution that simplify planning the loading. Thanks to that, the monitors installed over the ramp display detailed information on the tasks on the particular position. The second module is used for the operations related to unloading and is based on the assumptions similar to the loading part. The third module is responsible for reporting. It is the third module, more specifically its functionality related to the analysis of the report, that allows for simplifying the operating of goods flows by the precise identification of mistakes and delays in the work of operators and carriers.
All the activities are described with a code
Integration, optimising and automation of the information flow and consequently simplified management and improvement of results are also the effect of implementing the innovative solution in Fuch Oil (manufacturer and supplier of, among others, oils for vehicles and machines). A large number of branches in scattered locations on the one hand enables reaching the customer quickly, and on the other it generates a considerable amount of data the quality of which needed improvement.
Service technicians, who are limited by time, are not always able to produce precise reports, which are important for the company to determine the demand for the substances that are often very expensive. The first step towards full process automation was finding the device that would not only operate as a mobile computer, telephone and camera, but also be resistant to falls, humidity, dust and dirt. On the next stage the focus was on simplifying the monitoring of oil deliveries to customers, reporting with the accelerated receiving of feedback and eliminating the potential mistakes.
A service technician who goes to the customer to carry out the ordered works, for example in the area of filling up oil and grease in machines knows that each device to work on has its own barcode, just as every packaging of oil and grease. Such a barcode was also assigned to each activity carried out by a service technician.
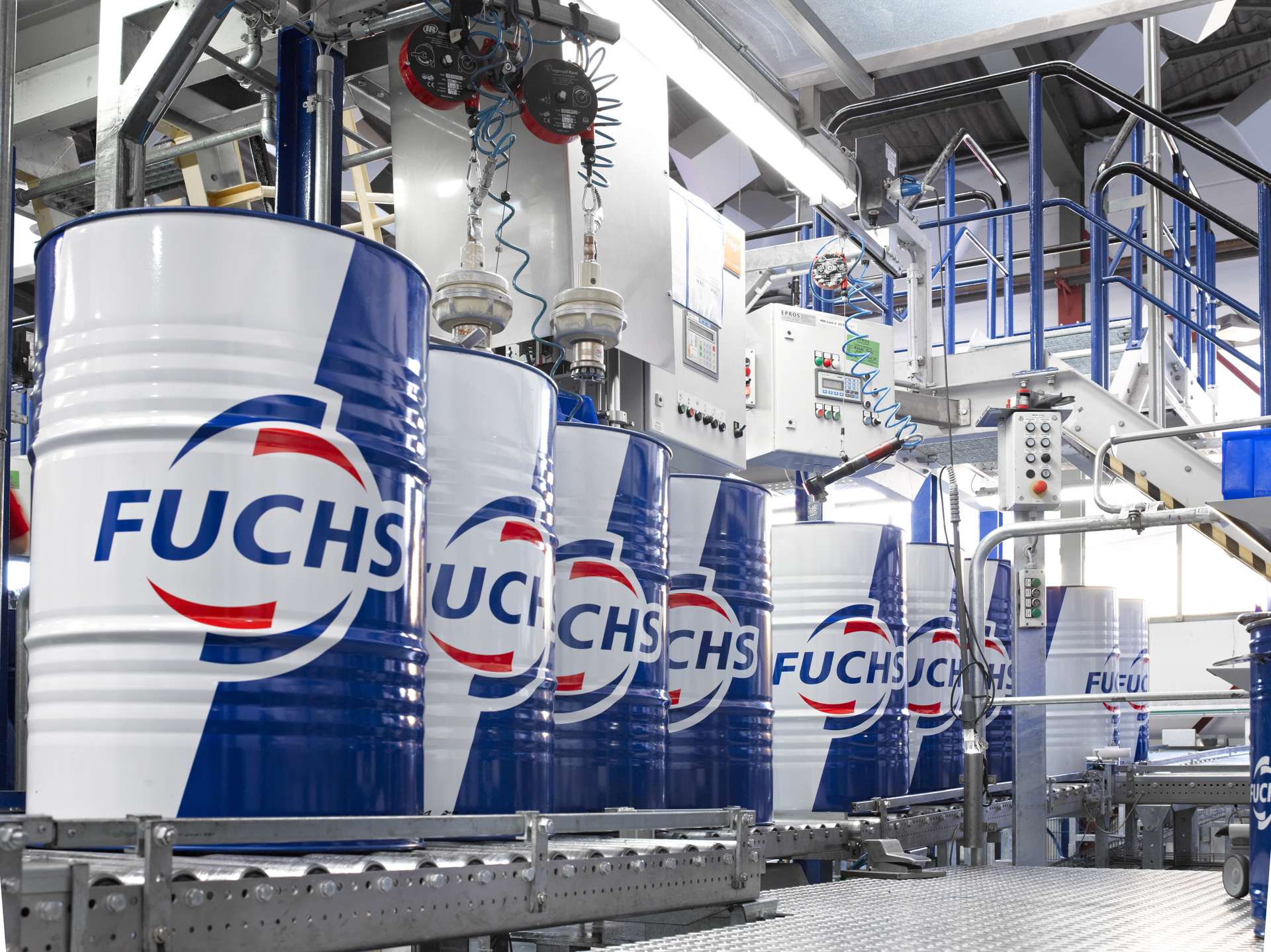
Photo: Fuchs Oil
The technician’s job is to scan all the codes, enter the amount of used materials and give its location with the customer’s name. Also, the technician must enter the amount of time devoted to the ordered activity and the data of person confirming the works on the part of the client. After coming back to the home branch all the data of the services carried out are placed in the main computer, which generates a detailed report for the customer, including for instance the time of carrying out the particular activities, the amount of materials used and the devices that were subject to servicing. The report with the invoice is then sent to the customer. All the data are encrypted and may also be exported to other branches, e.g. for comparative purposes.
Photo: Wabco