Trudno sobie wyobrazić w dzisiejszych czasach nowoczesny magazyn, który nie byłby wyposażony w szereg narzędzi wspomagających jego zarządzanie. Przedsiębiorstwa stają przed dylematem, czy zastosowanie programów dedykowanych do obsługi poszczególnych procesów logistycznych jest konieczne, czy też wystarczy sam system ERP?
Ponieważ system ERP jest zazwyczaj pierwszym systemem wdrożonym w przedsiębiorstwie, jest systemem „do wszystkiego”. Realizowane są w nim zarówno operacje finansowo-księgowe, jak i magazynowe. Dodatkowo, jest to często jedyna baza danych. Na wczesnym etapie rozwoju firmy, jest to działanie uzasadnione, głównie z przyczyn ekonomicznych. Niezależnie od sektora, jeżeli rośnie baza klientów i/lub produktów, pojawia się potrzeba zarządzania poszczególnymi działaniami w sposób bardziej złożony.
Jeżeli chodzi o tytułowe zarządzanie magazynem, programem pierwszego wyboru jest system WMS. Oprogramowanie to jest w całości dedykowane zarządzaniu magazynem, potrafiące przenieść logistykę na zupełnie inny poziom.
Główne różnice pomiędzy systemem ERP a WMS
ERP |
WMS |
Stan indeksów z ilością sumaryczną, czasami przypisane sektory składowania |
Pełna wiedza na temat ilości danego indeksu. Sumarycznie, per lokalizacja, “w drodze” w magazynie |
Produkty wraz z cenami i ich historią |
Brak obsługi cen |
Historia sprzedaży |
Historia ruchów fizycznych towaru |
Historia zakupów |
Historia przyjęć |
Analiza ABC (analiza mająca na celu wytypowanie najbardziej dochodowych indeksów) |
Analiza XYZ (analiza mająca na celu wytypowanie najbardziej rotujących indeksów) |
Pełne dane na temat majątku firmy |
Pełne dane na temat produktów i materiałów eksploatacyjnych |
Prognozowanie zakupów |
Estymacja zajętości poszczególnych lokacji |
Brak ograniczeń co do wielkości i ilości produktów |
Wprowadzone realne dostępne powierzchnie do wykorzystania |
Pełna baza dostawców, współpracowników i klientów |
Dane tylko dotyczące realizowanych dostaw i zamówień |
Możliwa inwentaryzacja majątku firmy |
Możliwa inwentaryzacja towarów i innych materiałów ewidencjonowanych |
Przykład źle dobranego rozwiązania do obsługi procesów magazynowych (branża e-commerce)
Firma uzyskała dodatkowy kapitał od podmiotu zewnętrznego w związku z czym, zdecydowała się na podjęcie działań w poniższej kolejności:
– Relokowała dotychczasowy magazyn do nowego, znacznie większego obiektu
– Zintensyfikowała zakupu u dotychczasowych dostawców oraz znacznie poszerzyła ofertę sklepu
– Uruchomiono nowy system ERP, w którym realizowano zarówno czynności finansowo-księgowe jak i operacje magazynowe
– Rozpoczęto kampanię reklamową w internecie
– Zaplanowano wdrożenie systemu klasy WMS na kolejny rok, po szczycie sezonowym, który dla tej branży trwa około trzech miesięcy, na przełomie wiosny i lata
– Rozpoczęto analizę procesów logistycznych pod kątem optymalizacji kosztowej i wdrożenia systemu WMS
W trakcie analizy przeprowadzonej na zlecenie przedsiębiorstwa przez podmiot zewnętrzny, wskazano szereg zagrożeń związanych z organizacją procesów logistycznych przy użyciu systemu ERP. Jako kluczowe ograniczenia wskazano:
– Brak historii ruchów magazynowych w jednej bazie danych
– Brak funkcjonalności stricte magazynowych w wybranym systemie ERP
– Brak możliwości pracy na skanerach
– Brak dynamicznego zarządzania rotacyjnością towarów (pierwotne ułożenie zgodnie z historia sprzedaży, z każdym dniem traci na znaczeniu i przestaje pełnić funkcje optymalizującą procesy
– Brak możliwości użycia MOP zarówno w wariancie kompletacji sumy indeksów i ich dekonsolidacji na zamówienia w strefie pakowania jak i w wariancie kompletacji kilku zamówień na raz
– Brak funkcjonalności automatycznych uzupełnień
– Brak sugestii dotyczących sposobów pobierania i pakowania na podstawie wymiarów produktów (sugestia ilości nośników pod zamówienie, wielkości kartonów do pakowania, automatycznego wyliczenia potrzebnej ilości listów przewozowych)
Wniosek końcowy analizy
Obsługa zbliżającego się szczytu sprzedażowego przy pomocy systemu ERP jest bardzo ryzykowna, możliwe jest wygenerowanie znaczących kosztów związanych z koniecznością zatrudnienia dodatkowych 10 – 20 FTE (wzrost od 50 do 100 proc.), a także stratami wizerunkowymi wśród klientów (niezrealizowane zamówienia, błędy). W celu uniknięcia powyższych zagrożeń, oraz ze względu na niewielki margines czasowy (zbliżający się szczyt sezonu) zaproponowano:
– Zmianę kolejności działań i minimalizację strat w nadchodzącym sezonie
– Zmiana polegającą na skupieniu się w pierwszej kolejności na aktualnie realizowanych procesach oraz wdrożeniu WMS
– Minimalizację strat, poprzez zatrudnienie 20 proc. więcej FTE, oraz zablokowaniu wszelkie reklamy i utrzymanie poziomu 100 proc. realizowanych zamówień złożonych
Firma nie zdecydowała się na zmianę kolejności zaplanowanych działań, natomiast nakłady reklamowe zostały zmniejszone tuż przed rozpoczęciem sezony (wcześniej mocno podnosząc ilość wizyt i zamówień). Efektem był wzrost zatrudnienia w sezonie o 55 proc. i realizacja zamówień złożonych w danym dniu na poziomie 40 proc. Spowodowało to:
– wydłużenie czasu dostawy do klienta z 24 h na 5 dni roboczych
– utratę części zamówień nie zrealizowanych na czas
– zwiększenie ilości zwrotów i doręczeń nieskutecznych
– znaczne zmniejszenie rentowności RDR
Dlaczego nie udało się obsłużyć „peak time”?
W powyższym przykładzie, przedsiębiorstwo powinno zmienić kolejność działań związanych z rozwojem biznesu. W pierwszej kolejności powinno skupić się na analizie procesów niezbędnych do zrealizowania założonych celów. Następnie wdrożyć system WMS i zoptymalizować procesy magazynowe wymienione po analizie jako kluczowe ograniczenia. Szczególny nacisk należałoby położyć na MOP oraz pełną obsługę wszystkich procesów w magazynie. W ostatniej kolejności natomiast uruchomić kampanię reklamową i rozszerzyć ofertę magazynową.
Rzadko się zdarza, żeby firma rozpoczynająca działalność, z którą związane jest magazynowanie produktów, półproduktów lub surowców, była w stanie przewidzieć stopień rozwoju logistyki własnej w perspektywie kilku kolejnych lat. Z kolei bardzo często możemy w praktyce logistycznej spotkać przedsiębiorstwa, które wybierając system WMS lub moduł WMS w obrębie systemu ERP nie miały wiedzy, doświadczenia lub skoncentrowały się tylko na czynnikach ekonomicznych. W takich przypadkach, przy rozwoju logistyki własnej (np. optymalizacja kosztowa, automatyzacja, analizy przepływów) zmuszone są do poszukiwań bardziej rozbudowanych systemów. Zmiana tak kluczowego dla magazynu systemu jak WMS, wiąże się przede wszystkim z:
– Wysokim kosztem zakupu nowego oprogramowania
– Czasochłonną analizą przed wdrożeniem
– Ustaleniem i usunięciem krytycznych połączeń pomiędzy systemem ERP a starym systemem/modułem WMS oraz ich migracja do nowego rozwiązania
– Najczęściej implementacją na zasadzie „operacji na żywym organizmie” przeprowadzeniem etapami w weekendy lub przerwy w działaniach handlowych
– Przeglądem i zmiana fizycznej struktury magazynu (oznakowania, układy regałów/półek/pól odkładczych, wymiany skanerów, drukarek, sieci, etc.)
Fot. Pixabay/efaflex
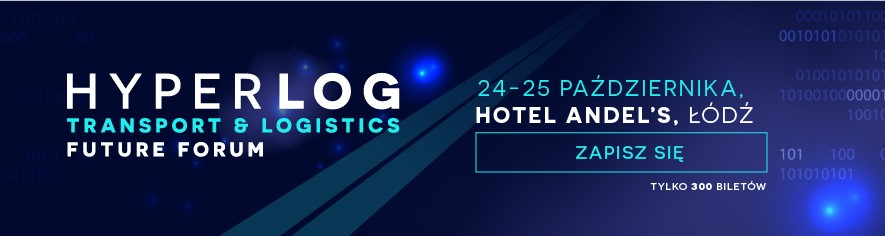