– Zdarzały się przypadki załadunków z dwóch lub więcej punktów, jak również konieczność przerzucania, nierzadko znacznych ilości, między magazynami – przyznaje Hubert Frasunkiewicz, dyrektor pionu zarządzania łańcuchem dostaw w Grupie CIECH. To przeszłość. W wywiadzie z Trans.INFO tłumaczy, jak magazyn wysokiego składu w Janikowie oraz okna czasowe sprawiły, że czas załadunku skrócił się kilkukrotnie.
Dorota Ziemkowska, Trans.INFO: Założyliście sobie cel, by załadunek towarów opakowanych nie zajmował więcej, niż 30 min, a nawet by zamykał się w kwadransie. Cel podobno ambitny, pytanie, jak to wyglądało wcześniej?
Hubert Frasunkiewicz, dyrektor pionu zarządzania łańcuchem dostaw w Grupie CIECH: Zanim został uruchomiony magazyn wysokiego składu w Janikowie, a wraz z nim okna czasowe na załadunkach, które miały umożliwić osiągnięcie tego celu, załadunki były organizowane nierzadko z różnych lokalizacji. Zdarzały się przypadki załadunków z dwóch lub więcej punktów, jak również konieczność przerzucania, nierzadko znacznych ilości, między magazynami. W konsekwencji nasze wolne przestrzenie magazynowe szybko się zapełniały, często też blokowane były strefy wysyłkowe aby oszczędzić czas i nie składować palet na regały tylko na chwilę.
Precedens ten oczywiście utrudniał organizację załadunku. Druga sprawa – zanim wdrożyliśmy okna czasowe, przewoźnicy awizowali się w godzinach, które im odpowiadały najbardziej. Bo albo akurat tak kierowcy wypadała pauza, albo o takiej porze zjeżdżał z trasy. Brak planowania aut często powoduje tworzenie się kolejek przed zakładem w oczekiwaniu na załadunek, co też miało miejsce w naszej organizacji.
Stąd konieczność zmian. Tylko skąd założenia akurat 30, a nawet 15 minut?
Założenia i cele, które sobie postawiliśmy w tym projekcie wynikały z historycznych analiz oraz best practice rynkowych (najlepszych praktyk rynkowych – przyp.red.). Myślę, że przyjęliśmy dosyć bezpieczny wariant.
Istotnym elementem w procesie wyznaczania długości okna nie jest fizyczne wstawienie palet na auto (dobry operator zrobi to w parę minut), a wystawienie palety z regału wysokiego składu i dowiezienie jej do punktu przygotowania wysyłki. Czas tego procesu nie zależy tylko o szybkości przenośników czy zwinności operatora. Bardzo ważna jest strategia składowania palet w magazynie oraz reguły ich wydawania. W naszym przypadku wyzwaniem był też fakt, iż proces układany był pod nowy magazyn w fazie „start up”. A wiadomo, że podczas rozruchu takiej inwestycji mogą się pojawić pewne problemy, nad którymi trzeba będzie zapanować. Bardzo krótkie okna czasowe mogłyby nam uniemożliwić jakąkolwiek reakcję. Zwłaszcza w szczycie sezonu, gdy mamy napięty harmonogram i każde okno jest zapełnione.
I jak wyglądała sytuacja zaraz po wdrożeniu okien czasowych?
Poprzez lepsze planowanie oraz zmianę organizacji pracy czas załadunku skrócił się znacząco, co też bezpośrednio przyczyniło się do skrócenia czasu oczekiwania kolejnych aut. Poza awaryjnymi przypadkami nie mamy już przypadków, by samochód czekał po parę godzin. Zdarzają się oczywiście przypadki, gdzie auto czeka, jednak jest to głównie związane z decyzją o optymalizacji trasy przejazdu przewoźnika lub np. „kręcenia” pauzy kierowcy na parkingu przed zakładem.
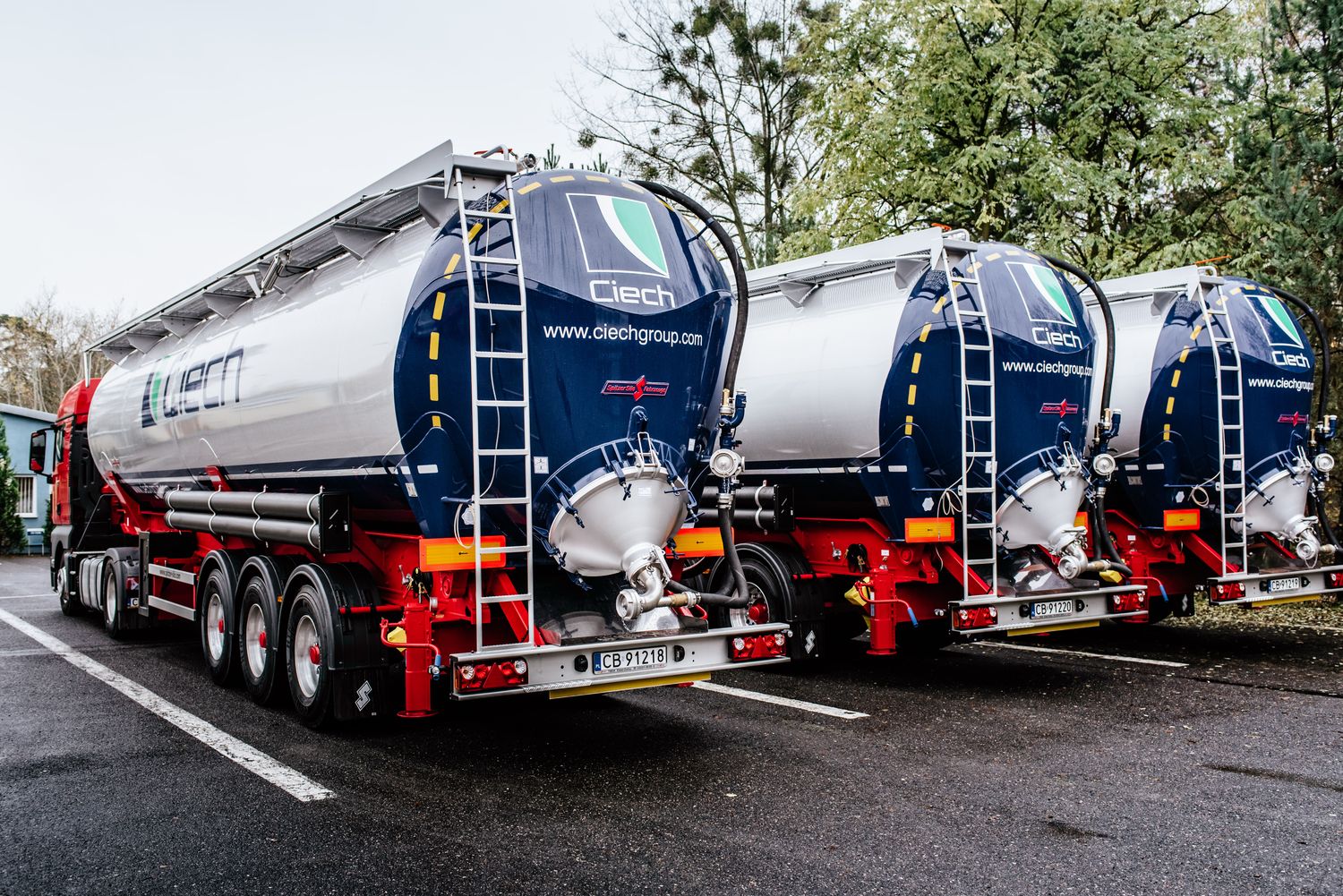
Fot. Grupa Ciech
Ile na swoją kolej muszą czekać kierowcy, którzy nie zdążą na swoje okno czasowe?
Standardowo spóźnialscy powinni zostać przekierowani na koniec kolejki. Jednak do tematu podchodzimy indywidualnie, a większe zmiany ustalamy bezpośrednio z działem sprzedaży. Zdarzają się różne scenariusze, np. przewoźnik podstawia podwójną obsadę kierowców, opóźniony załadunek nie spowoduje spóźnienia dostawy. W skrajnych przypadkach, po uzgodnieniu z klientem, przesuwamy termin realizacji. Możemy też mieć wolne okna w tzw. „międzyczasie” i wówczas wypełniamy je „spóźnialskimi”.
Jak często dochodzi do sytuacji, że nie każde okno czasowe jest obstawione? Macie Państwo zawsze ustawiony jakiś bufor?
Z reguły nie planujemy buforów. Staramy się wypełniać każde okno czasowe, które w standardzie wynosi 30 minut. Czas ten jest wystarczający do sprawnego przeprowadzania załadunku. Ale pamiętajmy również, że kierowca wykonuje manewry „przygotowujące” przed i po opuszczeniu doku, albo że musimy przygotować odpowiednie dokumenty transportowe. Te dodatkowe czynności też konsumują czas i muszą zostać obsłużone w oknie czasowym.
Nie oznacza to jednak, że nie zostawiamy żadnej elastyczność przewoźnikowi. Przewoźnik otrzymując od nas zlecenie może dokonać wyboru godziny (w ramach wolnego okna czasowego), na którą planuje się podstawić. Działa to trochę na zasadzie – kto pierwszy, ten lepszy. I ten będzie mógł sobie wybrać najlepsze okno. Przy czym, oczywiście, duże znaczenie ma to, na którą godzinę towar musi dojechać. Dajemy więc pewną elastyczność przewoźnikowi, musi on jednak pamiętać o terminach, jakie nad nim ciążą. Z naszej strony temat jest monitorowany przez dział obsługi transportu i podejmowane ewentualne działania na wypadek odchyleń.
I jak to kontrolujecie?
Sprawdzamy, co wpisał. Jeśli widzimy, że przewoźnik zaawizował się np. na godz. 20, a rozładunek jest o 6 rano i może nie zdążyć, to będziemy interweniować. Jesteśmy ograniczeni przepisami prawa i umowami, więc koniecznym jest abyśmy mieli nad tym wszystkim kontrolę.
Jak często zdarza się, że trzeba ingerować?
Pyta pani o bardzo operacyjny aspekt tej pracy, którym ja do końca nie zajmuje się na co dzień. Musimy mieć jednak na uwadze, że transport jest bardzo dynamicznym obszarem do zarządzania, gdzie odchylenia mogą pojawić się praktycznie na każdym etapie realizacji. Na bazie doświadczenia mogę zapewnić, że działamy w sposób nie odbiegający znacząco od innych organizacji.
Pamiętajmy też, że to w interesie przewoźnika leży, żeby zamówić sobie takie okno załadunku i tak dobrać dostępne auto, żeby dostarczyć terminowo towar i podjąć kolejny ładunek zgodnie z planem.
Oczywiście mamy świadomość, że rynek jest dziś niełatwy dla przewoźników drogowych, jednak po to właśnie mamy okna czasowe, procedury wewnętrzne, kontrakty długoterminowe i periodyczną analizę współpracy z danym przewoźnikiem, żeby wszystkie te narzędzia wykorzystywać w procesie continuous improvement (ciągłego udoskonalania – przyp. red.)
Jak działa system, przez który przewoźnicy mogą zaplanować termin przyjazdu i podać dane awizacyjne?
Mówimy o systemie klasy TMS, spiętym poprzez interface z systemem klasy ERP, który Ciech ma w swoich lokalizacjach. Zlecenia z ERP są przesyłane do TMS, w którym zakładane jest zamówienie transportowe, dotyczące konkretnej trasy. I to leży po naszej stronie.
Następnie to zamówienie przesyłane jest automatycznie do przewoźnika, który jest do tej trasy przypisany. On je akceptuje, po czym uzupełnia niezbędne informacje typu: okno czasowe, dane kierowcy, ciągnika i naczepy. Ewentualne ma określony czas na to, żeby nas poinformować, że nie może zrealizować takiego zlecenia. Wtedy szukamy innego rozwiązania.
To znaczy, co dokładnie wtedy robicie?
Standardowo strategią jest uzyskanie odpowiedzi na takie pytania:
– jeśli nie możesz na tę godzinę, to na którą możesz;
– jeśli możesz na inną, to czy jest wówczas wolne okno czasowe;
– jeśli jest wolne okno czasowe, to czy dojedziesz na czas z towarem do odbiorcy;
– jeśli nie dojedziesz na czas, to czy możesz dać na ten kurs podwójną obsadę;
– jeśli nie możesz jej dać, to idziemy na rynek i szukamy innego przewoźnika do tego zlecenia (zazwyczaj korzystamy ze stałej bazy firm). Jeśli go znajdziemy, ale jest droższy, to ty, nasz kontraktowy przewoźniku, płacisz różnicę;
– jeśli widzimy, że dostawa będzie opóźniona, wówczas informujemy dział sprzedaży z prośbą o nową awizację u klienta.
A jak wygląda procedura, gdy winni problemów są nie przewoźnicy, ale sam magazyn?
Takie opóźnienia mogą mieć kilka przyczyn. Po pierwsze, może się okazać, że nie ma towaru pod załadunek. Natomiast już przy składaniu zamówienia korzystamy z systemu, który sprawdza nam dostępność towaru i jest w stanie zablokować konkretną liczbę palet pod jakieś zamówienie. W ten sposób minimalizujemy to ryzyko.
Po drugie, może się pojawić awaria systemu polegająca np. na tym, że nie jesteśmy w stanie wypisać dokumentów systemowo, tylko musimy to robić ręcznie. Albo nie mamy możliwości wydania palety (błąd systemu czy awaria automatyki).
Wtedy informacja o tym idzie od razu do działu sprzedaży, który informuje klientów o opóźnionych dostawach. Oczywiście z całą konsekwencją tego, że z niektórymi klientami mamy SLA (Service Level Agreement, czyli umowa dotycząca gwarantowany poziom świadczenia usług – przyp. red.), która determinuje konsekwencje i sposób działania w przypadku opóźnionych dostaw.
Niezależnie od powodu, czy chodzi o to, że załadunek się opóźnia z winy magazynu, czy auto przyjechało nie w terminie, staramy się nadrobić ten czas. Lead time’y nie są liczone z dokładnością co do pięciu minut, więc jakieś bufory w każdym przypadku są z góry założone, w związku z czym wiele zależy od organizacji pracy w takiej chwili.
Może więc wystarczyć, że przysunie się dodatkowy wózek, żeby przyśpieszyć załadunek, znajdzie dodatkowego operatora, poprosi kontrahenta o podwójną obsadę, albo podmieni przewoźnika na innego, który może szybciej dostarczyć jakiś towar. Wszystko to organizowane jest z udziałem działu sprzedaży, aby klient nie dość, że nie był zaskoczony zmianą, to jeszcze dostał informację wraz z propozycją rozwiązania.
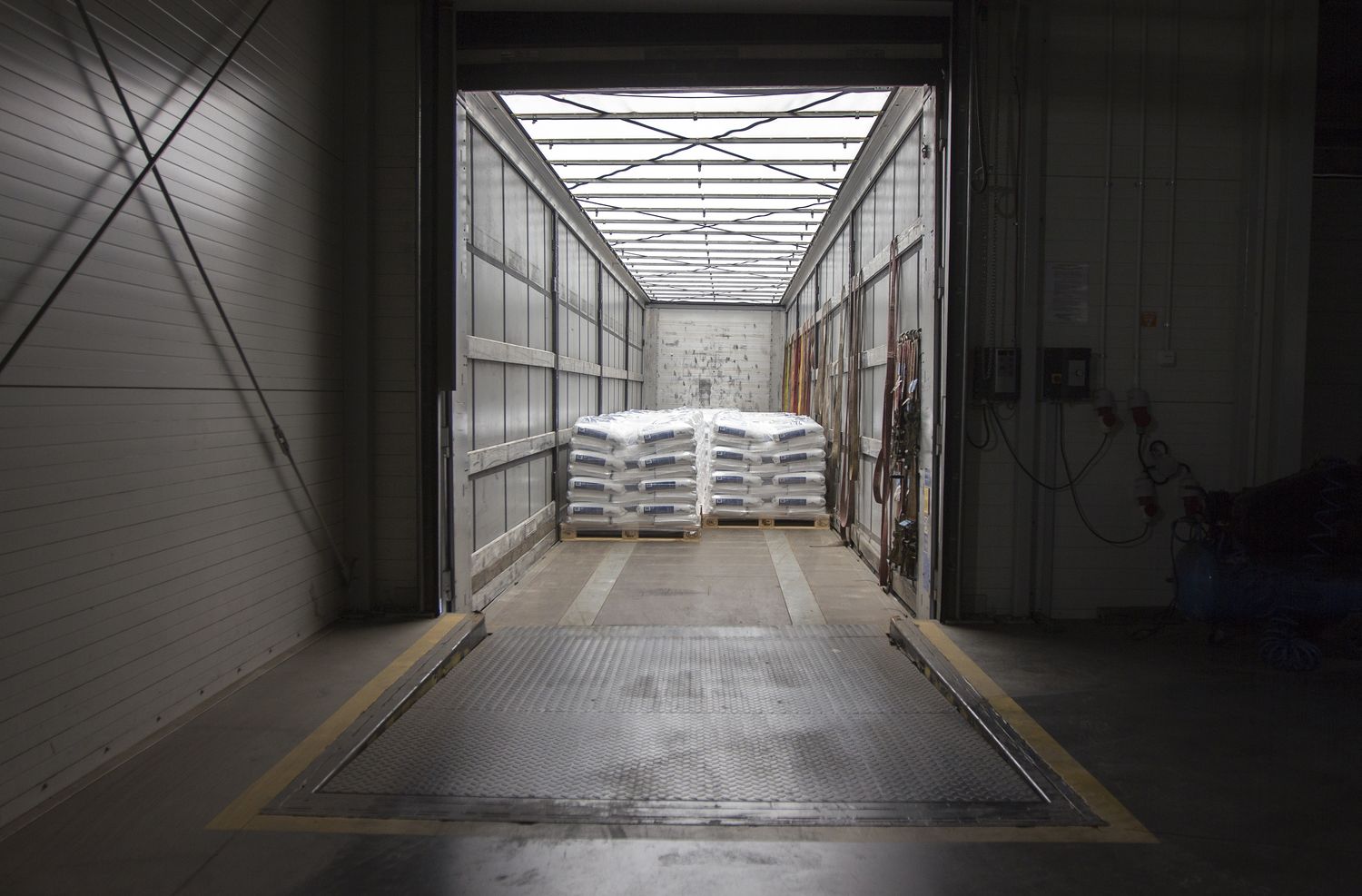
Fot. Grupa Ciech
A jak często dochodzi do sytuacji wymuszających modyfikowanie tego planu?
Niezbyt często, bo, jak powiedziałem, mamy system kontroli zapasów, mamy okna czasowe, którymi nie tylko zarządzamy na bieżąco, ale też szukamy zagrożeń w awizacjach, jeśli ktoś wpisał się nie tam, gdzie trzeba.
Jak już mówiłem, na co dzień nie zajmuję się operacjami, więc nie powiem pani, ile to jest procentowo. Zdarzają się takie przypadki, natomiast skala nie jest tak duża, by uważać, że stoi za tym problem natury procesowej. Raczej siła wyższa.
To może inaczej. Czy w ciągu ostatniego roku dochodziło do takich sytuacji?
Tak.
Ile razy?
Nie powiem pani, ile konkretnie było takich przypadków.
Przejdźmy więc do kolejnych rozwiązań, które mają ograniczyć czas załadunków towarów. Podobno CIECH postawił również na zwiększenie liczby punktów przeładunkowych. Do ilu?
Obecnie mamy w Janikowie sześć punktów, jednak na bieżąco korzystamy z czterech, dwa są raczej buforowe. Cztery wspomniane działają najbliżej grzebieni przy dokach, czyli rolkowych przenośników grawitacyjnych, po których przyjeżdżają palety przysłane z magazynu wysokiego składu.
W jaki sposób ta inwestycja wpłynęła na cały proces załadunku?
Wraz z nią zmieniła się cała koncepcja przygotowania procesu załadunku. Bo zacznijmy od tego, jak to wyglądało, zanim wprowadziliśmy zmianę. W wielu przypadkach staraliśmy się przygotować zamówienie jeszcze zanim samochód się podstawił. Odkładaliśmy 24 palety, czyli liczbę, którą bierze taka ciężarówka, i czekaliśmy na jej przyjazd.
I to się sprawdzało, gdy auta pojawiały się o czasie, z regularnością, którą sobie zaplanowaliśmy. Natomiast jakiekolwiek obsunięcie powodowało, że zostawaliśmy z tymi 24 paletami, które nas blokowały. Byliśmy zakorkowani, a już musieliśmy wystawiać kolejne, dla następnego auta. Że nie wspomnę o fakcie, że im więcej przesuwania palet, tym większe ryzyko ich uszkodzenia. Nie stronimy więc dziś od przyznania, że to nie był efektywny sposób działania.
I kolejna sprawa z tym związana – nasz magazyn wysokiego składu o wysokości kilku miejsc paletowych, miał regały wjezdne. Co skutkowało tym, że sam proces pobrania palety był wydłużony, ponieważ wiadomo, że wózek widłowy, który musi wjechać w wąski skład nie działa tak szybko jak automat, który taką paletę pobierze sam. Tak, w skrócie, to wszystko wyglądało przed zmianą.
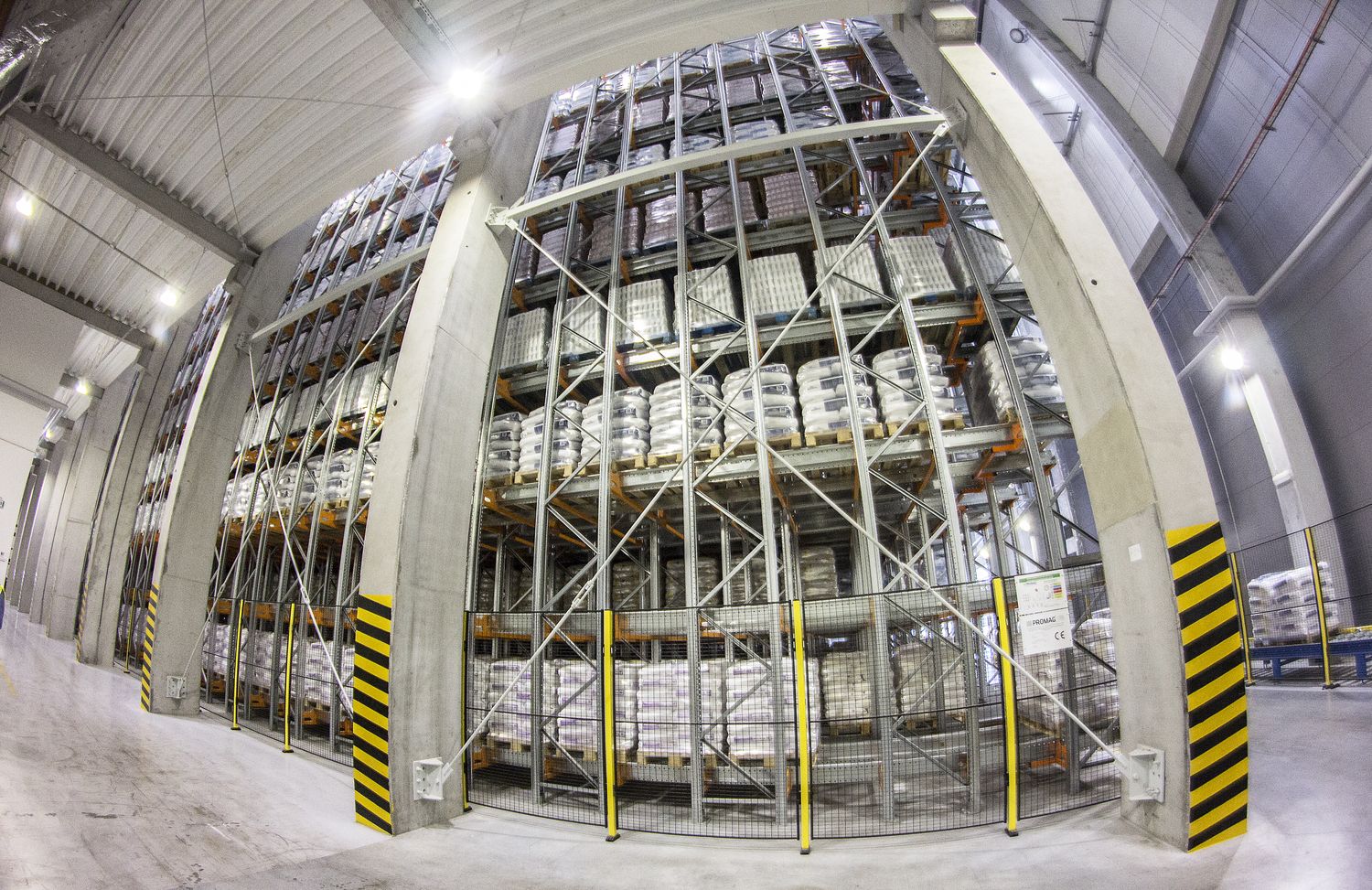
Fot. Grupa Ciech
A po niej?
Przede wszystkim uruchomiliśmy magazyn wysokiego składu z półautomatycznym rozwiązaniem. To znaczy, że paleta z produkcji jest przyjmowana systemowym wózkiem widłowym, wkładana na satelitę, który przenosi ją na konkretną lokalizację na wysokim składzie.
Z kolei proces wysyłki z tego magazynu polega na tym, że operator wysyła zadanie do satelity, w którym określa, jaką paletę, z jakim zamówieniem trzeba pobrać. Paleta przyjeżdża tym satelitą do operatora wózka, który później przekłada ją na przenośnik. W związku z czym sam proces przygotowania zamówienia jest sprawniejszy.
Mamy też większy bufor czasowy, m.in. dzięki temu, że posiadamy dziś wydłużony system transportujący, czyli rolki, dzięki czemu możemy z palet na te rolki ustawić więcej towaru. Pomagają również wspomniane wcześniej grzebienie, których obecność daje nam większe pole manewru, gdyby się okazało, że jakieś auto się nie podstawia. Jesteśmy w stanie szybciej zareagować, nawet zatrzymać wydawanie jednych palet i rozpocząć kolejnych.
Dziś nasz docelowy model działania zakłada, by rozpocząć pobieranie palet z magazynu dopiero w momencie zawizowania samochodu pod wysyłkę na bramie. Bo wówczas ryzyko, że auto się nie podstawi, nie istnieje.
A nie ma ryzyka, że wtedy kierowca będzie musiał czekać na towar zbyt długo? W końcu sam proces pobierania palet zajmuje trochę czasu.
Oczywiście, ryzyko jest. Gdyby pojawiła się jakaś awaria – czy to przenośnika, czy wózka widłowego, byłoby opóźnienie. Pamiętajmy jednak, że po pierwsze, auto musi dojechać z bramy do doku, a sam proces przygotowania palet pod załadunek zajmuje średnio kilkanaście minut (w zależności od lokalizacji palet), po drugie, w te 10 minut nie trzeba wcale przygotować całego towaru. Wystarczy pierwsze palety, po to, by auto, jak się podstawi, mogło już rozpocząć załadunek. A w międzyczasie, gdy kierowca pobiera go z grzebienia, jadą do niego kolejne palety.
Udało się obliczyć, o jaki procent te wszystkie rozwiązania, o których mi Pan opowiedział, usprawniły obsługę zamówień?
O kilkanaście procent.
Idźmy dalej. Załadunek w Grupie CIECH miało usprawnić również zainwestowanie w nowe wagi samochodowe. Skąd pomysł na taką inwestycję?
Odchodzimy tutaj od załadunku soli i wchodzimy w biznes związany z sodą. Bo jeśli chodzi o opakowania, o których rozmawialiśmy, to nie ma obowiązku ważenia samochodu, który przewozi palety opakowaniowe, ponieważ paleta jest wagą deklarowaną, to znaczy, że każda ma w systemie ustaloną swoją wagę. Jeśli paleta ma tonę, to wiem, że mogę maksymalnie załadować 24 palety. My jednak sprawdzamy kontrolnie wagę, głównie po to, żeby wiedzieć, czy samochód sam w sobie nie jest cięższy, niż powinien być. Taki proces ma miejsce np. w Janikowie.
Jeśli zaś chodzi o produkty sypkie, to stosujemy przy nich wagi samochodowe zainstalowane przy terminalach załadunkowych. I jest to ważna inwestycja, bo dzięki niej mamy informację, czy samochód jest już przeładowany, czy też możemy do niego jeszcze doładować.
Pytam o wagi samochodowe, bo poza celami wyznaczonymi dla produktów opakowanych postawiliście sobie również pewne cele dotyczące załadunku towarów masowych (sypkich). W ich przypadku zależy wam na załadunku trwającym około 30 minut, a więc nieco dłużej. Jednak, jak sami przekonujecie, jest to załadunek trudniejszy. Dlaczego?
Ponieważ załadunek odbywać się może bezpośrednio z produkcji, a więc w przypadku awarii auto będzie czekało. Proces samego ładowania jest też istotny, aby odpowiednio „rozmieścić” towar w auto silosie (waga całkowita i nacisk na oś). Do tego mogą dojść przypadki związane ze specyfikacją jakościową produktu.
Pod koniec zeszłego roku, w czwartym kwartale, mieliśmy parę takich zdarzeń, które spowodowały, że oczekiwanie samochodu na towar zajmowało więcej czasu.
To znaczy ile?
Zdarzało się, że ten czas przekraczał dwie godziny.
Dziś, standardowo, taki załadunek trwa około 30 minut. Samochód podjeżdża pod terminal. Kierowca idzie do dyspozytora z informacją o zleceniu, ten rozpoczyna załadunek. Gdy samochód jest załadowany, kierowca dostaje dokumenty, wraca do samochodu i jedzie na wspomnianą wagę. Bo ta, która znajduje się pod samym terminalem jest wagą orientacyjną, a nie certyfikowaną. Już przy bramie, po ważeniu, kierowca dostaje dokumenty z informacją o wadze załadowanego towaru.
Docelowo chcielibyśmy jeszcze zautomatyzować ten proces. Wprowadzić karty magnetyczne, które umożliwią kierowcy ustawienie całego procesu pod siebie, chcemy też dodać wizualizację świetlną informującą, czy samochód jest dobrze podstawiony. W niektórych miejscach, na przykład w Inowrocławiu, potrzebne jest przestawienie wagi bliżej punktu wyjazdu, dzięki czemu skrócony zostanie czas przejazdu samochodu po terenie zakładu.
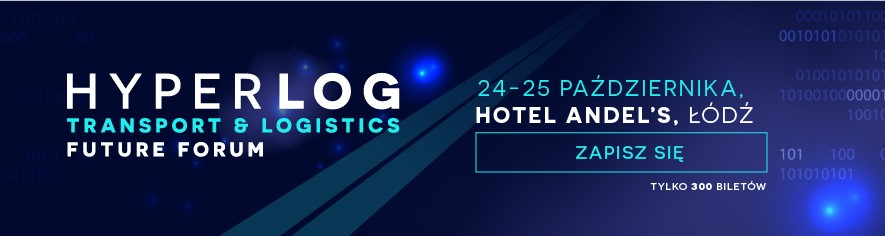
Jakie są dalsze plany Grupy CIECH, które mają jeszcze usprawnić załadunek?
Pracujemy nad procesem automatycznej identyfikacji aut przy bramie oraz na poszczególnych etapach realizacji zlecenia. Takie rozwiązanie może np. wykorzystywać kamery, które automatycznie identyfikują samochody pojawiające się w naszym zakładzie. Mówiąc w skrócie, gdy auto przyjedzie, system będzie robić zdjęcie tablicy rejestracyjnej, a rozpoznając numerację sprawdzi, jakie zamówienie transportowe jest do niej przypisane.
Rozważamy też wdrożenie systemu Yard Management System, który umożliwia bardziej szczegółowe raportowanie różnych etapów realizacji zamówienia na zakładzie produkcyjnym, niż TMS, który mamy dziś. Z tym systemem związana jest również możliwość sprawdzania, czy samochód nie spędza zbyt dużo czasu na terenie zakładu, co też analizujemy.
Rozważamy również doposażenie obecnego magazynu dla soli w rozwiązania bardziej automatyczne (np. układnice) oraz lepszą wizualizację procesów w systemach operacyjnych na magazynie (WMS).
Jak daleka to przyszłość?
Decyzja o tym, czy rozwiązanie (doposażenie magazynu) zostanie wdrożone i kiedy, jest zależne od innych inicjatyw, które prowadzimy w organizacji oraz dostępności zasobów. Technicznie takie rozwiązanie można zrealizować w około 6 miesięcy (zakładając ambitny plan) lub bezpieczny w 9-12 miesięcy. Na ten moment jednak mamy tylko szacunkowe plany. Nie ma konkretnej daty.
Fot. Grupa CIECH