Opracowana przez Japończyków, metoda kanban (z jap. szyld, tabliczka) powstała już siedem dekad temu. Dotyczy sterowania produkcją i zaopatrzeniem. W istocie opiera się na stworzeniu systemu przekazywania informacji dotyczących planowania, rozdziału zadań oraz ich przygotowania i realizacji. Nieodłącznym elementem jest również kontrola.
Pierwszy raz rozwiązanie nazwane kanban opisał w 1947 r. Taiichi Ohno, pracownik Toyota Motor Corporation. – Należy zorganizować przepływ materiałów w produkcji według zasady supermarketu, konsument bierze z półki określoną ilość produktu, a zauważona luka jest natychmiast uzupełniana – tak ideę kanban wyjaśniał wówczas Taiichi Ohno.
Jednym z kluczowych powodów, jakie przyświecały wdrożeniu kanban w Toyocie, była wówczas jej relatywnie niewielka produktywność w stosunku do ówczesnych, amerykańskich potentatów w branży motoryzacyjnej. Japończycy wyglądali w tej konkurencji blado, a właśnie urzeczywistnienie idei kanban miało – zdaniem jej propagatorów, to zmienić.
Idea była jasna: znaleźć sposób na to, by zwiększyć możliwość dostaw, bez potrzeby znaczącego powiększania magazynów. Wiązałoby się to rzecz jasna ze zmniejszeniem kosztownych zapasów surowców i półfabrykatów. Aby jednak dało się zminimalizować te koszty, potrzebny był elastyczny i wydajny system produkcyjny.
Kanban to takie zorganizowanie produkcji, aby każda komórka wytwarzała dokładnie tyle, ile w danej chwili jest potrzebne. W metodzie tej za czynnik krytyczny zarządzania materiałami uznano sterowanie zapasami.
Znaczenie systemu kanban często prezentowane jest jako urzeczywistnienie hasła “7 razy żadnych”
A dokładnie:
– żadnych braków,
– żadnych opóźnień,
– żadnych zapasów,
– żadnych kolejek,
– żadnych bezczynności,
– żadnych zbędnych operacji technologicznych i kontrolnych,
– żadnych przemieszczeń.
Teoretycznie sprawa wydaje się być prosta i oczywista, w praktyce bywa z tym jednak jednak różnie. Rzecz rozbijać się bowiem może głównie o organizację zaopatrzenia. Charakterystyczną cechą metody jest bowiem praktyczna likwidacja magazynów przedprodukcyjnych (jedyny zapas znajduje się na stanowisku roboczym, zresztą jest on stosunkowo niewielki). Dla wielu firm oznacza to prawdziwą “rewolucję”.
Zlecenia produkcyjne są ściśle zsynchronizowane z zamówieniami otrzymywanymi od klientów. Materiały i półfabrykaty dostarczane są od dostawców z godzinową dokładnością, a dzięki rezerwom zdolności produkcyjnych i elastyczności procesu produkcji możliwe jest wyprodukowanie niemal dowolnego elementu, w każdej chwili.
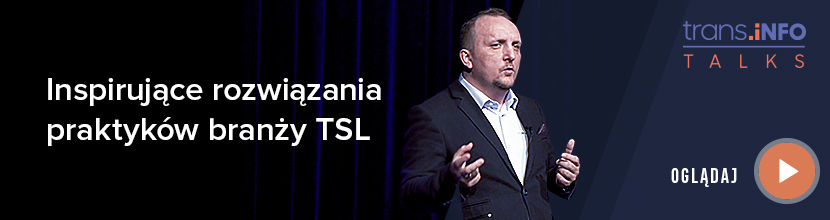
Aby skutecznie wdrożyć system kanban, obrót materiałowy może wymagać w konkretnej firmie szeregu zmian.
Chodzi m.in. o to, by:
– proces produkcyjny był ciągły, a produkty – jeśli to możliwe, maksymalnie ustandaryzowane
– cykle transportowe były możliwie ujednolicone, bo to pozwala planować logistykę w taki sposób by móc redukować zapasy (np. zastosowanie tzw. pętli mleczarza).
– wielkość produkcji musi być urealniona, tylko wówczas można redukować zapasy
– należy możliwie wyeliminować wahania w produkcji, szczególnie ważne jest planowanie jej w finałowym etapie
– należy stworzyć warunki kontrolowania przepływu materiałów za pomocą kart kanban (każdy produkowany/magazynowany element powinien mieć unikatową nazwę, indeks oraz miejsce składowania; dane powinny być dotyczyć zarówno produktów, jak i materiałów i pojemników, bądź palet transportowych)
– móc optymalnie zarządzać pojemnikami (składowanie pojemników na stanowisku również kosztuje, rzecz w tym aby te koszty zmniejszać).
Cały system musi być przy tym prosty i przejrzysty, aby maksymalnie ograniczyć ryzyko błędów
W Lean Enterprise Institute Polska podkreślają, że kanban to w istocie sterowanie produkcją według zasad Lean Manufacturing. Kanban sprzężony jest bowiem z czasem, produkcją w systemie ssania i poziomowanym harmonogramowaniem, co w praktyce umożliwia realizację zasady just in time.
Zwykle kanban jest wykorzystywany do sygnalizowania, kiedy dany element do produkcji zostanie zużyty (skonsumowany). W Lean Enterprise Institute zaznaczają jednak, że kanban różni się, w kilku punktach, od tradycyjnych metod sterowania produkcją. W wytwarzaniu tradycyjnym harmonogram produkcyjny jest dostosowany każdego indywidualnego procesu i każdy proces produkuje zgodnie z tym harmonogramem (brak zsynchronizowanego w czasie sprzężenia zwrotnego z procesów z informacją o dokładnych potrzebach).
Tymczasem kanban jest w istocie fizycznym narzędziem harmonogramowania, ściśle łączącym i synchronizującym aktywność na poszczególnych etapach zaopatrzenia i produkcji. Steruje przemieszczeniami materiałów, uwzględniając zarówno czas, jak i ilość, w zależności od sygnałów z procesu.
Zapobiega nadprodukcji i pomaga redukować zapasy
Zdaniem Arta Smalleya, autora pracy “Poziomowany system ssący” (wyd. Lean Enterprise Institute Polska), kanban ma za zadanie w szczególności:
– zapobiegać nadprodukcji (i nadmiernemu przemieszczaniu) materiałów pomiędzy procesami produkcyjnymi;
– dostarczać konkretne zlecenia produkcyjne procesom w oparciu o zasady uzupełniania (osiąga to, zarządzając zarówno synchronizacją czasu ruchu materiałów, jak i ilością przemieszczanych materiałów);
– służyć nadzorującym produkcję za narzędzie sterowania wizualnego, pozwalające określić, czy produkcja wyprzedza, czy spóźnia się z realizacją harmonogramu (rzut oka na miejsca, w których trzymane są skrzynki do gromadzenia kanbanów, pokazuje, czy materiały i informacja przepływają w sposób czasowo zsynchronizowany, zgodnie z planem);
– być narzędziem ciągłego doskonalenia (każdy kanban reprezentuje pojemnik zapasów w strumieniu wartości; planowana z czasem redukcja liczby kanbanów w systemie oznacza bezpośrednio redukcję zapasów i odpowiadające tej redukcji zmniejszenie czasu przejścia od surowca po klienta).
Fot. pixabay.com/geralt