Smyk to sieć handlowa z artykułami dla dzieci, m.in. zabawkami. Obecna jest w Polsce od czterech dekad, dysponuje 140 punktami w galeriach, ma też własny sklep internetowy. Rozwój sieci oraz coraz większa różnorodność produktów w sklepach stacjonarnych spowodowały, że liczba towarów do “przeprocesowania” zaczęła przewyższać możliwości magazynu.
Placówki Smyka działają też w Rosji, na Ukrainie i w Rumunii. Plany spółki przewidują rozwój wszystkich kanałów sprzedaży.
– Zwinność i sprawność operacyjna nabiera szczególnego znaczenia w czasach powszechnego trendu ilustrowanego popularnym stwierdzeniem “be multichannel or die”. W przypadku Smyka oznacza to obsługę klientów w trzech kanałach dystrybucji: obsługę sklepów stacjonarnych w Polsce i za granicą, obsługę partnerów franczyzowych poza granicami Polski i klientów sklepu internetowego. Każdy kanał ma inną dynamikę, wymagania asortymentowe i serwisowe oraz sezonowość uwarunkowaną klimatem i kulturą danego rynku zbytu – tłumaczy Michał Janikowski, supply chain director sieci Smyk.
Sorter podwoił wydajność
Od ponad dziesięciu lat, w zakresie magazynowania i dystrybucji Smyka obsługuje Spedimex. Wśród niedawnych, głośnych usprawnień jest zautomatyzowany sorter w łódzkim magazynie, który przyspieszył logistykę Smyka.
Dzięki niemu, ponad dwukrotnie zwiększono wydajność procesu (z ok. 40 tys. do nawet 100 tys. sztuk dziennie), bez potrzeby powiększania powierzchni magazynowej oraz zespołu pracowników. Największy potencjał drzemał w procesie kompletacji.
Sorter działa w oparciu o system kompletacji pick-by-light. Ta metoda opiera się na systemie świetlnym, w którym lista towarów zastępowana jest przez cyfrowy wyświetlacz, z wykorzystaniem diod sygnalizacyjnych.
System podpowiada, jakie czynności należy wykonać, co ogranicza do minimum ryzyko potencjalnych błędów.
Nowy system zwiększył tempo kompletacji
Sorter kompletacyjny oparto na przenośnikach, ze zindywidualizowanym oprogramowaniem. Umożliwia kompletowanie zamówień częściowo, czyli bez konieczności procesowania całego zlecenia, aby przygotować konkretną partię i od razu wysłać do odbiorcy.
Po prekompletacji kartony z indywidualną etykietą wjeżdżają na nitkę sortera. Etykieta jest skanowana, a system wie co i w jakiej ilości znajduje się na nitce zasilającej. Na każdym wjeździe do danego węzła zainstalowano czytnik, który sprawdza czy dany asortyment jest potrzebny w danej sekcji. Jeżeli tak, kartony wpychane są do węzła za pomocą automatycznych wysięgników. Wówczas na wyświetlaczu pojawia się liczba sztuk do spakowania. Osoba kompletująca wyjmuje wskazaną ilość i umieszcza w kartonach.
Po zapełnieniu się kartonu operator wypycha jednostkę kompletacyjną na przenośnik, a karton w dalszym etapie wędruje do strefy kontroli, gdzie przeprowadzana jest weryfikacja jakościowa oraz ilościowa. Karton jest zamykany automatycznie, etykietowany i wysyłany do sortera końcowego. Tam towar układany jest na paletach, w strefie konsolidacji, czeka na załadunek.
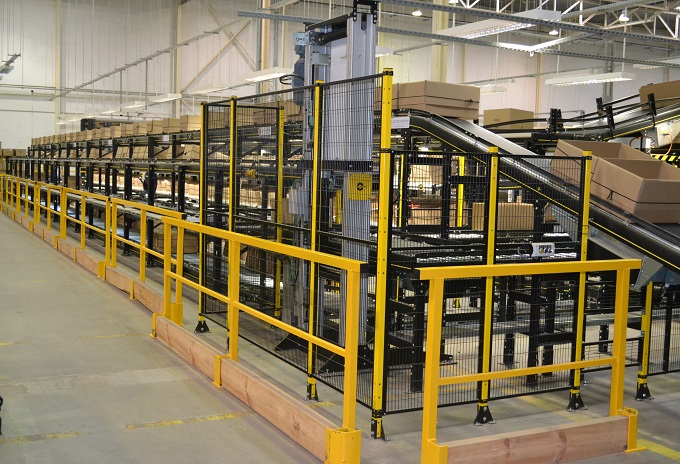
Fot. Spedimex
Wdrożenie podzielono na trzy etapy: instalację sortera, stworzenie oprogramowania oraz modyfikację samego procesu. Poprzedził je pilotażowy projekt.
Wprowadzone rozwiązanie wpłynęło zarówno na poprawność, jak i tempo kompletacji. Wzrosła wydajność procesu, a także przepustowość magazynu. Niejako „przy okazji”, automatyzacja wpłynęła na usprawnienie pracy zespołu kompletacyjnego. System podpowiada pracownikom, jakie zadania należy wykonać, co znacząco ogranicza ryzyko potencjalnych błędów.
Załoga potrzebowała czasu na oswojenie
Ważnym aspektem nowego rozwiązania jest zwiększenie komfortu i ergonomii pracy. Kartony zasilające podawane są na poszczególne sekcje bezpośrednio za pomocą przenośników (operator nie musi po nie chodzić). Każda osoba ma swoje lokacje do obsługi, z tego samego miejsca pobiera puste kartony i bez wykonywania dodatkowych ruchów, odrzuca puste kartony zasilające.
Ewidentne korzyści bynajmniej nie sprawiły, że załoga od razu dała się przekonać do wprowadzonych zmian.
– Załoga, która od lat była przyzwyczajona do zupełnie innego systemu pracy, podchodziła z rezerwą do nowych rozwiązań, a zmiana mentalności dokonywała się stopniowo. Obawy były związane zarówno z pracą z samym urządzeniem, jak i zupełnie nowym procesem. Z czasem pracownicy docenili intuicyjność i łatwość pracy z sorterem. Zyskali przekonanie, że można pracować sprawniej i wykonywać więcej, niż to było jeszcze rok wcześniej – podkreślają gospodarze magazynu w Łodzi.
Optymalna wydajność to dziś 70 tys. do 100 tys. sztuk dziennie.
– Zaletą rozwiązań automatycznych, oprócz oczywistego przyspieszenia operacji, jest “zapas mocy”, który można wykorzystywać w okresach największej aktywności – konkluduje Michał Janikowski.
Fot. Pixabay/falco