Już sama liczba podzespołów, z których składa się samochód, stanowi wielkie wyzwanie dla producentów, a co za tym idzie – również dla logistyków. Branża automotive jest pod tym względem niezwykle wymagającą. Obsługa logistyczna i transportowa tego sektora przemysłu koncentruje się przede wszystkim na dostarczaniu fabryk oraz serwisów komponentów i części. Do tego potrzebne są odpowiednie środki techniczne – choćby pojemniki przystosowane do przewożenia ciężkich elementów.
W magazynowaniu i transporcie na rzecz automotive stosuje się głównie skrzynie metalowe, tzw. gitterboxy, pojemniki siatkowe zwane również drucianymi. Metalowe pojemniki nadają się do transportowania oraz przechowywania ciężkich i nieporęcznych przedmiotów, a z takimi mamy do czynienia nierzadko w sektorze motoryzacyjnym. Do najpopularniejszych należą też pojemniki typu KLT, wykonane z tworzy sztucznych. Mają wzmocnioną konstrukcję, zapewniającą wysoką wytrzymałość. Można je z powodzeniem stosować wielokrotnie w łańcuchu dostaw bez ryzyka uszkodzenia samych pojemników i towaru.
Konkretne rozwiązania stosowane w poszczególnych fabrykach tego sektora są jednak dosyć zróżnicowane. Za dość typowe i nowoczesne uznać można to co stosuje firma Gestamp Umformtechnik, która specjalizuje się w produkcji stalowych części i podzespołów – o od drzwi przesuwnych na słupkach B, do tylnych osi (jej kluczowi klienci to BMW, Daimler, Ford, Volvo i VW, a także producent maszyn rolniczych John Deere). W logistyce wykorzystuje pojemniki Magnum Optimum.
Te pojemniki mieszczą więcej i nie rdzewieją
Fabryka w Bielefeld zatrudnia niemal 1,5 tys. pracowników i jest największym zakładem produkcyjnym grupy Gestamp. Na terenie siedziby (ok. 200 tys. mkw.) prowadzonych jest równocześnie wiele prac, a wewnętrzna powierzchnia logistyczna często jest niemal całkowicie zajęta.
Zakład musiał zatem usprawnić np. logistykę stalowych pustych ram dostarczanych w klatkach stalowych z Manchesteru. W brytyjskiej spółce stowarzyszonej z Gestamp produkowane są zakrzywione ramy o długości ok. 850 mm. Z Manchesteru są dostarczane do Bielefeld w celu dalszego przetworzenia jako integralne ramy do wahaczy.
Duże nośniki ładunku okazały się wydajniejszym rozwiązaniem niż używane wcześniej klatki stalowe. Jeszcze kilka lat temu elementy pakowano w stalowe klatki o wymiarach 1240 x 835 mm. Przechowywanie ich wymagało jednak dużo miejsca, a transport zwrotny do Anglii generował wysokie koszty. Stalowe klatki narażone były też na negatywne działanie oraz skutki przechowywania na otwartej, niezabezpieczonej przestrzeni na zewnątrz, co w rezultacie powodowało korozję.
Kluczową zaletą nowego rozwiązania jest większa pojemność i wytrzymałość plastikowego pojemnika. Magnum Optimum mieści 98 sztuk, do tej pory ładowano w klatkach 78 stalowych pustych ram. Gestamp Umformtechnik transportował wcześniej 60 stalowych klatek lub 4680 stalowych pustych ram za pomocą jednej ciężarówki, obecnie na ciężarówkę wchodzą 52 plastikowe kontenery o zawartości 5096 sztuk. Pojemniki chronią zawartość przed zabrudzeniem i rdzą, kurzem (dzięki zamkniętym ścianom bocznym i pokrywie). Jeśli Gestamp chce używać opakowania do innych produktów, można je dostosować do wymaganej wysokości za pomocą dołączonej ramy Optiframe.
Transport opon
Nie zawsze, dla przewiezienia konkretnego rodzaju ładunku optymalne okazuje się typowe nadwozie lub standardowa naczepa. Bywa, że trzeba pojazd zaopatrzyć w specjalne rozwiązania, np. ze względu na przepisy dotyczące transportu opon. Fliegl opracował system QTS, który można dokupić do każdej naczepy kurtynowej we wszystkich wersjach standard, maxi, mega, jumbo, coil mulda, również w wariancie light. QTS pozwala na stabilny bezpieczny załadunek opon po sam dach, kierowca sam może zdemontować i zmontować QTS, stąd naczepa pozostaje uniwersalna, wykorzystywana może być do ładunków paletowych, jak również do przewozu kilku rodzajów ładunku jednocześnie. System opracowano tak, aby w maksymalny sposób zmniejszyć nacisk ładunku na plandekę. Dobrym pomysłem jest sektorowy podział, który zapewnia odpowiednio skonstruowany system kłonic, listew aluminiowych oraz pasów.
Własne wersje zabezpieczeń do transportu opon ma Kögel. Pierwsza obejmuje trzy burty siatkowe z aluminium umieszczone w schowku, po cztery stalowe szyny kotwowe kombi przypadające na obszar kłonic od dołu, aluminiową burtę siatkową górną i mocowanie krzyżakowe z pasami mocującymi. W wersji drugiej każdy obszar kłonic wyposażony jest dodatkowo w trzy burty siatkowe z aluminium i dwie stalowe szyny kotwowe kombi, jak również jedną pionową stalową szynę kotwową kombi, zawieszaną centralnie w środkowej części obszaru kłonic.
Naczepy do przewozu stali i blach
W przypadku towarów o nietypowych gabarytach czy kształtach, a z takimi mamy nierzadko do czynienia w przypadku automotive, wszystko sprowadza się do stworzenia możliwości należytego zamocowania przewożonego ładunku.
W dostawach blach wykorzystywanych w automotive przydają się np. zabudowy kurtynowe w wersji specjalnej z klinami (np. Wesob). Zabudowa jest stała, z kurtyną przesuwną, dachem przesuwnym i podnoszonym na czas załadunku. Wbudowana mulda umożliwia przewóz blachy o średnicy zwojów od 800 do 1900 mm. Zastosowano system klinów, które stanowią punkty podparcia dla zwojów blachy o średnicy większej niż 1300 mm. Są też dodatkowe gniazda do mocowania kłonic (wzdłużne zabezpieczenie przewożonych zwojów blachy).
Schmitz Cargobull oferuje dla zwojów stali rozwiązanie S.CS COIL. Dzięki zamykanej muldzie pojazd pozostaje uniwersalny, może być wykorzystany w transporcie różnych innych ładunków, np. w drodze powrotnej (pokrywa muldy umożliwia m.in. transport towarów na paletach).
Również naczepę Krone Coil Liner Compact można zamówić np. z systemem mocowania dla transportów stali. Masa własna naczepy jest mniejsza niż 5 t, w ten sposób zwiększa się ładowność, która pozwala na transport szczególnie ciężkich zwojów blachy lub większych ilości ciętej taśmy. Kolejną cechą szczególną pojazdu jest system Vario Coil, oparty na dwóch bocznych szynach rastrowych w podłodze. Dzięki szynom rastrowym zwoje/cięte taśmy o wszelkich wymiarach i masie można umieszczać na środku ciężkości pojazdu, można zrezygnować z dotychczas typowego zabezpieczenia kłonicami.
Magazyny bazują na automatyzacji
Jest coraz więcej przykładów nowoczesnych, kompleksowych rozwiązań z zakresu składowania i transportu dla automotive. Część z nich wykorzystuje koncepcję przemysłu i logistyki 4.0.
W przypadku Centrum Dystrybucyjnego Volkswagena w Polsce zastosowano np. 128 regałów mających prawie 100 tys. miejsc składowania. Wśród nich są cztery szafy automatyczne: dwie typu paternoster oraz dwie typu lean-lift. Procesy usprawnia automatyczny, wewnątrz magazynowy system transportu, przenośnik rolkowy o niemal 580-metrowej długości, obsługujący 3 piętra regału podestowego. Jest 8 stanowisk przyjęcia towaru oraz 8 ujść (wysyłka). Wydajność stacji przenośnika wynosi 1,2 tys. pojemników/godz. Rocznie w magazynie realizowanych jest około 1,5 mln zleceń, liczba wydań jest ponad trzykrotnie większa.
Po to by móc przyjmować, składować i dystrybuować oferowane przez siebie towary (ponad dwa miliony części zamiennych i akcesoriów) Inter Cars, w oddanym do użytku kilkanaście miesięcy temu Centrum Logistycznym w Zakroczymiu zastosował rozwiązania automatyczne.
Magazyn realizuje wszystkie kluczowe zadania logistyczne:
– przyjmuje towary od dostawców,
– realizuje zamówienia i wydaje towary dla klientów,
– obsługuje zwroty,
– prowadzi przeładunki typu “cross-docking”,
– realizuje usługi konfekcjonowania.
Całość składa się z czterech hal, główny magazyn ma wysokość 10 m, a jego serce stanowi czteropoziomowa zabudowa regałowa (17 tys. miejsc paletowych i 18 tys. miejsc półkowych) oraz system taśmociągów o łącznej długości ok. 11 km. Przyjęcia i wydania towaru realizowane są z wykorzystaniem ok. czterdziestu bram magazynowych. Magazyn wyposażono w specjalnie dla niego zaprojektowany system sortowania, dzięki któremu możliwe jest przesortowanie 30 tys. sztuk towaru w ciągu godziny.
Całością kieruje system informatyczny, rola pracowników sprowadza się głównie do programowania poszczególnych zadań, a także do nadzoru.
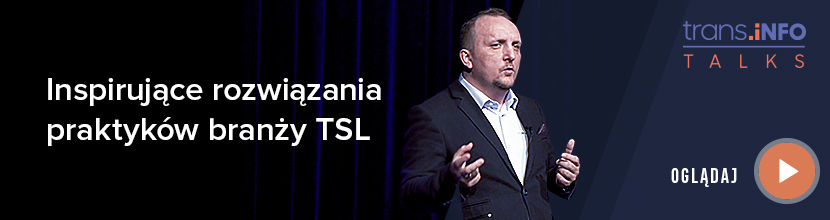
Miniload sprawdza się w magazynach z małymi częściami
W automotive często stosuje się także rozwiązania magazynowe typu miniload. Przeznaczone ono jest głównie do obsługi relatywnie niewielkich ładunków, w różnego typu opakowaniach składowych i transportowych (kartony, pojemniki plastikowe oraz tace).
Te ostatnie wykorzystywane są np. do składowania części lub elementów konstrukcyjnych, a następnie ich wydawania na linię produkcyjną, przechowywania towarów i zasilania operacji pobierania, kompletacji i pakowania zamówień w branży motoryzacyjnej. Buforowanie skompletowanych zamówień i wydawanie kartonów lub pojemników do wysyłki odbywa się automatycznie zgodnie z regułą GTP (Goods to Person – towar do człowieka).
W SSI Schaefer podkreślają, że całe jednostki magazynowe, pełne małych części, kontrolowane są komputerowo, a następnie transportowane za pomocą bezobsługowych systemów zautomatyzowanych. Moduły miniload z kanałami kompletacyjnymi sprawdzają się w:
– magazynach sektora automotive, w których znajduje się duża ilość małych części o dużym przepływie materiałów,
– w różnego rodzaju narzędziowniach,
– w składach buforowych dla pojemników/kartonów skompletowanych i oczekujących na wysyłkę.
Wśród spektakularnych wdrożeń automatycznego magazynu pojemnikowego jest Kiekert. Zaprojektowano układ składający się z dwóch układnic o wysokości blisko 12 m, systemu regałów, systemu przenośników oraz systemu zarządzającego. Regałów to standardowa konstrukcja typu open face o podwójnej i poczwórnej głębokości. Oznacza to, że w regale na półce mogą znajdować się dwa pojemniki o podstawie 600 x 400 mm lub cztery pojemniki o podstawie 300 x 400 mm. Nie oznacza to jednak, że w lokacji składowane musi być dany rodzaj pojemnika – możliwe jest wiele kombinacji np. jeden nośnik o podstawie 600 x 400 mm i dwa o podstawie 300 x 400 mm.
Autonomiczny transport wewnętrzny
Środkami transportu, które coraz częściej trafiają do automotive usprawniając transport wewnątrzzakładowy są wózki autonomiczne. Po zastosowaniu odpowiedniej infrastruktury, np. w postaci podajników, mogą zastąpić typowe widlaki. Automatyczne, samojezdne wózki AGV (Automated Guided Vehicles) potrafią np. transportować komponenty z obszaru magazynowego do strefy montażu. Inwestycje w tego typu sprzęt są uzasadnione, gdy przynoszą oszczędności kosztów robocizny oraz umożliwiają pracę praktycznie bez przerwy.
W WDX podkreślają, że wózki samojezdne są sprzętem w pełni zautomatyzowanym, nie wymagającym obsługi operatora. Pojazdy mogą holować załadowane przedmiotami wózki, które mogą się z nim sprzęgać automatycznie. Wózki (przyczepy) mogą przewozić surowce lub gotowe produkty. AGV może również przewozić przedmioty na sobie. Przedmioty te mogą być przyjmowane przez wbudowane rolkowe przenośniki i rozładowane przez odwrócenie kierunku obrotu rolek.
Pojazdy AGV mają zdefiniowane trasy i obszary, w których mogą się poruszać. Nawigacja realizowana jest np. za pomocą taśmy magnetycznej przyklejonej do podłogi, lasera, stosowana jest też metoda pętli indukcyjnej. Pierwsze, w automotive stosowane są do transportu części między stanowiskami montażowymi i transportu towarów wewnątrz zakładów lub magazynów. Zaletą tej metody jest prosta i tania instalacja i możliwość łatwej i szybkiej modyfikacji trasy.
Alternatywę stanowi rozwiązanie, w którym trasa jest wyznaczona przez przewód elektryczny umieszczony w kanale wykonanym w podłożu. Przewód jest używany do przesyłania sygnału radiowego lub prądu o określonej częstotliwości, który generuje pole magnetyczne. Czujnik zamontowany na podwoziu blisko podłoża wyczuwa położenie pojazdu względem ścieżki sygnału i zapewnia poruszanie się po wyznaczonej trasie. Trzeci wariant stanowi nawigacja laserowa.
Cechą rozwiązań logistycznych dla automotive jest dość powszechne stosowanie zestawów transportowych. Dzięki możliwości podpięcia kilku przyczep można dowolnie dobierać liczbę i rodzaj jednostek ładunkowych (palety, kosze, pojemniki). Kierowca, wykonując jeden cykl transportowy, jest w stanie osiągnąć podobny rezultat w procesie logistycznym do tego, który operator wózka widłowego uzyskuje w kilku etapach (jeden pociąg transportowy jest zatem w stanie zastąpić kilka wózków). Ważna jest także możliwość dokładnego dopasowania poszczególnych wózków, elementów pociągu do charakterystyki danego użytkownika, a nawet do konkretnego „gniazda” odbioru. W tej kwestii przydaje się elastyczna konfiguracja liczby i gabarytów przewożonych pojemników z komponentami dostarczanymi w określone miejsce.
Fot. Fliegl