Systemy automatyczne mają zapewnić maksymalne wykorzystanie dostępnej przestrzeni, tak w poziomie jak i w pionie, jak również mają ułatwić prace magazynowe. Rozwiązania typu miniload przeznaczono głównie do obsługi relatywnie niewielkich ładunków. Ich skuteczność sprawdziła jedna z sieci handlowych, ale także dostawca części dla sektora motoryzacyjnego.
Technologia miniload ma zastosowanie w wielu branżach, a jednocześnie sprawdza się w centrach dystrybucji. Automatycznie obsługiwać można wiele rodzajów opakowań składowych i transportowych: kartony, pojemniki plastikowe o różnych rozmiarach oraz tace różnej wielkości. Te ostatnie wykorzystywane są np. do składowania części lub elementów konstrukcyjnych, a następnie ich wydawania na linię produkcyjną, przechowywania towarów i zasilania operacji pobierania, kompletacji i pakowania zamówień, np. w branży motoryzacyjnej, odzieżowej i w handlu detalicznym.
Automatycznie przeprowadza się buforowanie skompletowanych zamówień i wydawanie kartonów lub pojemników do wysyłki, zasilanie rozwiązań modułowych opartych o technologię GTP (Goods-to-Person/towar-do-człowieka).
W SSI Schaefer podkreślają, że całe jednostki magazynowe, pełne małych części, kontrolowane są komputerowo, są transportowane za pomocą bezosobowych, zautomatyzowanych systemów magazynowania i wyszukiwania. Następnie przekazywane są one do odpowiednich punktów komisjonowania za pomocą przenośników.
Miniload szansą dla e-commerce
Dostawcy poszczególnych rozwiązań nie mają raczej wątpliwości, że motorem rozwoju i w tym przypadku jest technologia i to właśnie ona będzie miała wpływ na większą liczbę wdrożeń systemów miniload w przyszłości.
Oprócz problemów na rynku pracy (trudności z pozyskaniem nowych i utrzymaniem obecnych pracowników) ważnym czynnikiem wpływającym na rosnące zainteresowanie technologią miniload jest rozwój przedsiębiorstw. Przykładem są firmy z sektora e-commerce, w którym sprawne funkcjonowanie w oparciu o tradycyjne technologie staje się coraz trudniejsze, a w niektórych przypadkach wręcz nie jest możliwe.
Moduły miniload z kanałami kompletacyjnymi sprawdzają się w:
– magazynach małych części o dużym przepływie materiałów;
– narzędziowniach;
– magazynach buforowych dla pojemników/kartonów skompletowanych oczekujących na wysyłkę.
Automatyczny magazyn pojemnikowy
Przykłady wdrożeń można mnożyć. Wśród spektakularnych jest Kiekert, dostawca w branży automotive, dla której Logzact zrealizował projekt automatycznego magazynu pojemnikowego. Zaprojektowano układ składający się z dwóch układnic Swisslog Tornado o wysokości blisko 12 m, systemu regałów, systemu przenośników oraz systemu zarządzającego automatycznym magazynem pojemnikowym MFC+ z interfacem do systemu SAP.
System regałów to standardowa konstrukcja typu open face o podwójnej i poczwórnej głębokości. Oznacza to, że w regale na półce mogą znajdować się dwa pojemniki o podstawie 600 x 400 mm lub cztery pojemniki o podstawie 300 x 400 mm. Nie oznacza to jednak, że w lokacji składowane musi być dany rodzaj pojemnika – możliwe jest wiele kombinacji np. jeden nośnik o podstawie 600 x 400 mm i dwa o podstawie 300 x 400 mm.
Wymagania klienta względem wydajności zostały oszacowane na podstawie danych z obszaru produkcji i wynoszą 200 poj. in i 200 poj. out w ciągu godziny. Całość rozwiązania sprostała wymaganiom klienta dając również pewien zapas wydajności i pojemności na przyszłość.
Większa pojemność składowania
Mecalux ma na swym koncie rozwiązanie przygotowane na potrzeby firmy Unidroco. To hiszpańska spółka będącej właścicielem sieci dwustu lokali zajmujących się sprzedażą artykułów drogeryjnych i perfumeryjnych oraz ponad trzydziestu lokali specjalizujących się w sprzedaży farb oraz dekoracji.
Opracowano i wdrożono projekt magazynu automatycznego opartego na systemie „produkt do operatora”, pozwalającego jednak na równoczesne uzupełnianie stanu magazynowego. Montaż instalacji podzielono na trzy etapy. W rezultacie powstał magazyn automatyczny pojemników składający się z czternastu rzędów regałów obsługiwanych przez siedem układnic, systemu przenośników oraz strefy ręcznej kompletacji, na którą składają się cztery stanowiska przystosowane do falowego przygotowywania zamówień.
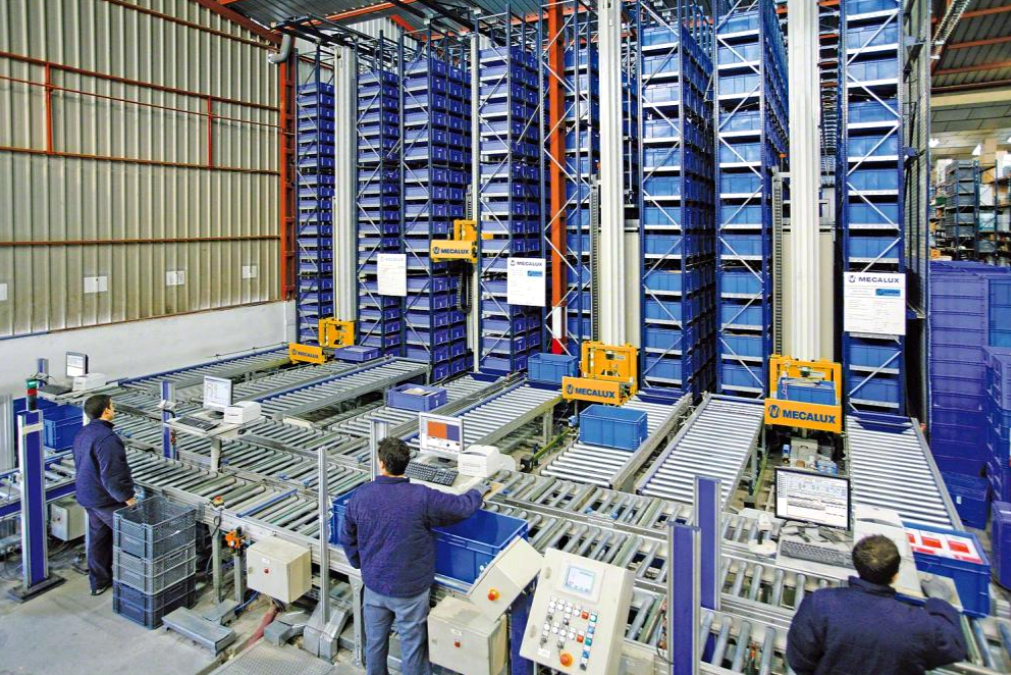
Fot. Mecalux
Ponadto w magazynie wdrożono system Easy WMS, który kontroluje każdy produkt, decydując gdzie powinien być skierowany oraz dostosowując odpowiednie działania do parametrów danego produktu, od momentu jego wejścia do magazynu do momentu wyjścia.
Korzyści dla Unidroco:
– większa pojemność składowania: łączna poj. magazynu wynosi 14,2 tys. pojemników o wymiarach 800 x 600 x 420 mm oraz obciążeniu do 100 kg;
– zwiększenie produktywności (zastosowane rozwiązanie pozwala na zwiększenie przepływu wejść i wyjść, co bezpośrednio przekłada się na wzrost liczby realizowanych zamówień);
– wzrost bezpieczeństwa pracy: zautomatyzowane systemy niemalże nie wymagają ludzkiej ingerencji, przez co ryzyko wypadku przy pracy zostaje znacznie ograniczone;
– skuteczne zarządzanie: dzięki systemowi zarządzania magazynem Easy WMS oraz systemowi sterowania Galileo, Unidroco ma możliwość zarządzania wszystkimi procesami, działaniami i operacjami zachodzącymi w magazynie.
Fot. Mecalux