Firma Gaugler & Lutz zastosowała indukcyjnie prowadzone, wielokierunkowe wózki bocznego załadunku do nowego, systemu regałowego. Przejścia w magazynie są wąskie, a powierzchnia wykorzystana w pełni.
Gaugler & Lutz dostarcza elementy konstrukcyjne do turbin wiatrowych, transportu drogowego i kolejowego oraz przemysłu stoczniowego. W zakładzie stolarki przemysłowej w Aalen-Ebnat przetwarza drewno i materiały piankowe. Są wykorzystywane np. do budowy łopat wirników turbin wiatrowych.
Przetworzone materiały były wcześniej przechowywane w trzech magazynach w Ebnat-Süd. Ze względu na rosnące zapotrzebowanie zdecydowano się zainwestować w nowy obiekt. W nowym centrum logistycznym w Aalen-Ebnat zastosowano inteligentny system magazynowania.
Wózki boczne prowadzi indukcja
Bazę stanowi 12-metrowy system regałów wspornikowych (pow. 2200 mkw.) tworzący miejsce na ok. 2500 palet. Palety są transportowane po magazynie za pomocą elektrycznych, wielokierunkowych wózków bocznych MQ 30. Wózki transportują towary przez mobilny regał za pomocą indukcyjnego systemu prowadzenia. Precyzyjnie umieszczają palety w wyznaczonych miejscach, a pomaga w tym półautomatyczny system pozycjonowania.
– Codziennie obsługujemy do 120 palet surowców – informuje Rüdiger Wittenbeck, kierownik projektu ds. optymalizacji procesów w Gaugler & Lutz.
Zanim zbudowano nowe centrum logistyczne, towary składowano w standardowych regałach lub po prostu układano jeden na drugim. Ładowacze czołowe transportowały palety do miejsc przeznaczenia. Różne formaty materiałów i różne rozmiary palet utrudniały przechowywanie materiałów tak, by optymalnie wykorzystywać dostępną przestrzeń.
– Po wdrożeniu półautomatycznego systemu logistyki magazynowej w nowym miejscu, transport i magazynowanie są teraz znacznie bardziej efektywne – twierdzi Vanessa Iliadis, która odpowiada za przetwarzanie logistyczne w Gaugler & Lutz.
Przygotowano specjalnie dedykowaną dla tego użytkownika koncepcję interfejsu, łączącego technologię transportu wewnętrznego ze specyfiką magazynu.
W ruchomym regale nie marnuje się miejsca
Każdy z regałów ma od trzech do pięciu ciągłych poziomów magazynowania, zainstalowanych jeden nad drugim, wraz z dwoma stałymi rzędami regałów połączonymi z bokami budynku. Ponieważ palety i przechowywane na nich materiały nie występują w standardowych formatach, długość, szerokość i wysokość towarów trzeba za każdym razem zmierzyć. Po pomiarze materiały są też ważone. To wymiary, a także całkowita waga określa miejsce przechowywania konkretnych towarów. Po zmierzeniu danego towaru system przenośników rolkowych transportuje go do magazynu. Tam ładunek trafia na wózek MQ 30, skanowany jest kod kreskowy.
– Miejsce do przechowywania jest wyraźnie określone przez wymiary i wagę ładunku i jest przekazywane do operatora wózka. Wyznaczony korytarz w ruchomym regale otwiera się automatycznie. Kierowca ustawia pojazd przed przejściem na przewodzie indukcyjnym, a następnie ustawia w ruchu elektryczny wielokierunkowy wózek boczny. Następnie pojazd ustawia się we właściwym miejscu przed regałem. Towary muszą być umieszczone bardzo precyzyjnie, aby umożliwić prześwit zaledwie kilku milimetrów i zapobiec kontaktowi z regałami lub towarami – wyjaśnia Vanessa Iliadis.
Maszt podnoszący zatrzymuje się automatycznie po osiągnięciu wymaganej wysokości regału.
Wielokierunkowe wózki boczne wyposażono w systemy ochronne. Skanery laserowe w pojazdach stale monitorują przejścia między stojakami, wykrywając ludzi lub przedmioty znajdujące się w niebezpiecznej odległości od pojazdów. “Inteligentny” sterownik automatycznie zmniejsza prędkość pojazdu przed zatrzymaniem.
Elektryczne, wielokierunkowe wózki boczne są prowadzone wzdłuż ścieżek, mających zapewniać precyzyjne pozycjonowanie. Indukcyjny system prowadzenia w mobilnym regale odpowiada za to, by poziom bezpieczeństwa był maksymalny, a ryzyko uszkodzenia regałów i towarów praktycznie wyeliminowano. Zoptymalizowane trasy w magazynach pomagają zaoszczędzić czas podczas przechowywania i pobierania towarów.
– Dzięki mobilnemu systemowi regałów i wielokierunkowym wózkom bocznym MQ 30 zmniejszyliśmy o połowę ilość miejsca potrzebnego do przechowywania. Udało się idealnie zsynchronizować system zarządzania magazynem, pojazd, czujniki i system regałów – podkreśla Rüdiger Wittenbeck.
Fot. Hubtex
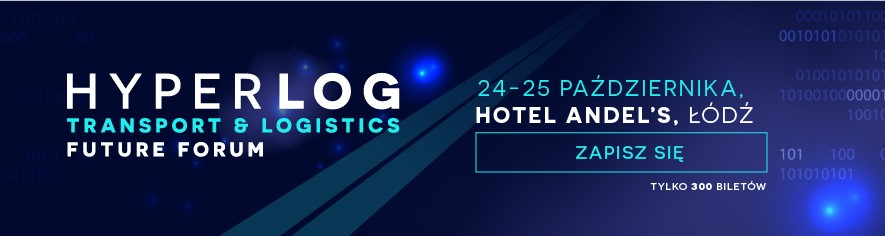