Opracowana przez Japończyków, metoda kanban (z jap. szyld, tabliczka) ma już grubo ponad pół wieku. Dotyczy sterowania produkcją i zaopatrzeniem. Opiera się na stworzeniu systemu przekazywania informacji dotyczących planowania, rozdziału zadań oraz ich przygotowania i realizacji. Wymyślił ją pracownik Toyoty, w fabrykach tej firmy została też zastosowana w pierwszej kolejności.
Taichii Ono wraz z zespołem sprecyzował kluczowe zasady ułatwiające wdrożenie kanban. Podstawę stanowi założenie, że każdy klient (zewnętrzny lub wewnętrzny) wydaje zapotrzebowanie swoim dostawcom (wewnętrznym lub zewnętrznym) w momencie skonsumowania zapasów. Z kolei dostawcy produkują dokładnie taką ilość danego wyrobu, jaka wynika z zapotrzebowania klienta (żaden produkt nie jest wytwarzany lub transportowany bez zapotrzebowania).
Dokument z zapotrzebowaniem na dany wyrób podąża razem z wyrobem, a rolą dostawcy jest zapewnienie zgodności (w tym jakości) produktu z wymaganiem. Wszystko to razem zwiększa efektywność i czułość procesu produkcyjnego.
Takie właśnie zasady rozpoczęto wdrażać w pierwszej połowie lat 50-tych ubiegłego wieku w zakładach Toyoty. W głównej fabryce, niejako “podłączono” to pod filozofię just in time (JiT).
Obecnie kanban i JiT powszechnie stosuje się w całym przemyśle motoryzacyjnym. Stawia to konkretne zadania przed logistykami. Kanban nie oznacza, że firmy nie magazynują. Wręcz przeciwnie, magazynują, tyle że ilości magazynowanych wyrobów bardzo uszczuplono.
Inicjatorem całego procesu jest de facto… ostateczny odbiorca samochodu
To on zamawiając auto uruchamia proces dostaw, który zostanie sfinalizowany za kilka, a czasem nawet za kilkanaście tygodni.
Kanban stał się zatem w Toyocie narzędziem do obsługi systemu produkcyjnego typu “pull”. Zapewnia przekazywanie informacji pomiędzy procesami i automatycznie zamawia części. Każdy przedmiot lub pudełko przedmiotów przepływających przez proces produkcyjny ma własny kanban (kanbany są usuwane z elementów podczas ich używania lub transportu i wracają do poprzednich procesów jako zamówienia na dodatkowe elementy).
Opracowana przez Toyotę metoda stała się więc, opartym na znakach systemem szeregowania, uruchamiającym logistyczny łańcuch i utrzymującym go na optymalnym poziomie. To coś w rodzaju systemu dostaw JiT, harmonizującego poziom zapasów z rzeczywistym zużyciem (hasła kluczowe: weź tylko to co potrzebne; wyprodukuj dokładnie wymaganą ilość; dostarcz na miejsce rzeczywiście tylko to, co zostanie zużyte).
W istocie proces uzupełniania porównywany jest do tego, jaki stosuje się w supermarketach. Ten proces ma zalety, pozwala uniknąć zakłóceń w tempie dostaw, ale też pośpiechu w ostatniej chwili.
Aby dobrze zorganizować pracę zespołową, należało przygotować system, w którym produkcja będzie opierała się tylko i wyłącznie na sygnale kanban znajdującym się pomiędzy różnymi miejscami (z góry określonymi) na produkcji. Sygnałami tymi mogą być np. sygnały dźwiękowe/świetlne, karty kanban, pusta paleta technologiczna lub pojemnik.
Wyliczono, że po trzech latach od wprowadzenia systemu kanban w Toyocie osiągnięto 75-procentową redukcję wszelkich zapasów i 95-procentową redukcję braków
Produkcja wzrosła o ok. jedną czwartą, przy jednoczesnym zredukowaniu przestrzeni produkcyjnej o ok. 10 proc.
Kilka lat temu zastosowaniem kanban chwaliła się też inna z firm sektora motoryzacyjnego, Kongsberg Automotive.
Norwegowie (w Polsce funkcjonują od 2000 r. w Millenium Logistics Park Pruszków) są dostawcą produktów (systemy wsparcia lędźwiowego, systemy masażu oraz maty grzejne do siedzeń foteli samochodowych) dla takich marek jak: Audi, BMW, Land Rover, Toyota, Volvo, VW.
Pierwszym obszarem, w którym do zaopatrywania wykorzystano system kanban, była linia produkcyjna DPU, wytwarzająca pompki do systemów masażu. Uruchomiono ją w 2012 r. Dla każdego obszaru produkcyjnego określono wykaz wyrobów gotowych wraz z pełną listą części niezbędnych do ich wytworzenia. Następnie wyodrębniono komponenty, których przemieszczanie z magazynu na linię produkcyjną może odbywać się w systemie “ssania” (m.in. drobne elementy: kostki, opaski zaciskowe, tuby, konektory, złącza, elementy gumowe, uszczelki, silniczki).
Ilość komponentów ciągnionych za pomocą jednej karty kanban stanowi iloraz liczebności partii produkcyjnej wykonywanej w ciągu dwóch godzin roboczych na jednym stanowisku pracy, a także liczby komponentów wchodzących w skład jednej sztuki wyrobu gotowego i liczby stanowisk roboczych równocześnie wykonujących pracę. Zastosowano karty kanban przepływu (wykorzystywane jako zlecenia wydań magazynowych) oraz pojemniki kanban z etykietą karty kanban, opisującą zawartość pojemników. Karty przepływu i pojemniki dotyczą określonego detalu używanego w zaznaczonym obszarze produkcyjnym i używane w zamkniętym obiegu pomiędzy magazynem jako dostawcą detalu a jego technologicznym odbiorcą.
Kolejny etap to domena magazynierów. Przejazd wózka widłowego i zbiórka kart przepływu i pojemników odbywa się po dokładnie wyznaczonej trasie, tzw. “Pętli Kanban” (magazynier organizuje przejazd po Pętli co godzinę, zbierając po kolei pojemniki i karty będące zgłoszeniem zapotrzebowania na komponenty). Posortowanie zleceń według zapisanej na karcie lub pojemniku lokalizacji magazynowej służy skróceniu czasu kompletacji zamówień.
Kanban dla firmy Kongsberg oznacza m.in. mniejszą ilość strat i marnotrawstwa, przez co system produkcyjny jest bardziej elastyczny i odporny na zakłócenia zewnętrzne. Dzięki dostępności części w systemie kanban odnotowano wzrost produktywności od 0,5 do 5 proc. dla każdej komórki i linii produkcyjnej. Po trzecie, system kanban zapewnia eliminację zbędnych cykli dostaw, nie zaburzając przy tym organizacji przepływów materiałowych. Pozwala zatem na obniżenie kosztów i minimalizację czasu pracy. Umożliwia redukcję zatorów i przestojów na liniach produkcyjnych oraz pozwala na obniżenie poziomu zapasów przed- i międzyoperacyjnych na stanowiskach roboczych do minimum – tłumaczyła Joanna Walasek, specjalista ds. logistyki w Kongsberg Automotive w wypowiedzi dla Log24.
O tym, że kanban sprawdza się również w innej roli, konkretnie w planowaniu pracy zespołu utrzymaniowego przekonują natomiast w PSI.
System PSIwms zarządza magazynami m.in. w LPP, Cisowiance, Piątnicy oraz ABM Greiffenberger. Każdy klient ma indywidualnie opracowaną strategię reagowania na zgłoszenia w zależności od jego potrzeb tak, by ewentualne problemy rozwiązywać możliwie jak najszybciej.
Szef zespołu zapytał nas (Quality Managerów) o to, jak można takie zadania zorganizować. Zgodnie z filozofią kanbana, postanowiliśmy zacząć od zrozumienia obecnego procesu: przebiegu zgłoszenia, roli każdego z użytkowników. Spotkaliśmy się i spróbowaliśmy ten proces narysować. Okazało się, że niektóre jego fragmenty były na tyle złożone, że aż trudne do wyjaśnienia i przełożenia na papier. To zwróciło naszą uwagę i już wiedzieliśmy, że właśnie tutaj pojawiają się wąskie gardła, które należy poprawić, pamiętając o tym, że proces jest tak wydajny, jak wydajne jest jego najwęższe gardło. Najbardziej skomplikowanymi i niejasnymi częściami były te związane z planowaniem pracy dla poszczególnych pracowników – tłumaczył Piotr Pilakowski, Junior Quality Manager PSI Polska.
Rozwiązaniem, w przypadku zespołu wsparcia systemu WMS okazała się wizualizacja procesu. Na potrzeby projektu utworzono tablicę kanbanową, zbierającą w jednym miejscu zgłoszenia od wszystkich klientów systemu. Zwiększenie widoczności zadań pozwoliło szybko oszacować ilość pracy do wykonania i sprawdzić ich status.
Istotny jest nie tylko aspekt przejrzystości, ale i użyteczności. “Szybkie filtry” pozwalają przełączać widok na zadania pogrupowane wg klientów, terminów lub czasu ostatniej aktualizacji, z kolei kolory pasków przy zadaniach wyróżniają te, które nie mają jeszcze ustalonego wymaganego terminu zakończenia. Różne typy zadań są jasno podzielone na błędy, usprawnienia, czy nowe funkcjonalności. Panel dostępny jest dla wszystkich pracowników zespołu, więc programista może w prosty sposób, przeciągając zadanie, oznaczyć je jako np. rozwiązane.
Tablica pozwala obserwować status zadań, natomiast szef projektu musi jeszcze wiedzieć jak bardzo zajęci są ludzie w jego zespole, by odpowiednio przypisywać pracę
Drugą rzeczą, która okazała się niezwykle przydatna, było wykorzystanie dwóch tak prostych narzędzi jak pisak i kartka papieru. Sama próba wizualizacji zastanego procesu spowodowała to, że bardzo szybko wykryliśmy elementy, które należy zmienić w pierwszej kolejności. Próba, ponieważ właśnie fragmenty dotyczące przydzielania pracy okazały się zbyt złożone, by je wyjaśnić i przenieść na papier. Jest to wyraźny sygnał, że tutaj należy zacząć zmiany – dodaje Piotr Pilakowski.
Fot. Wikicommons
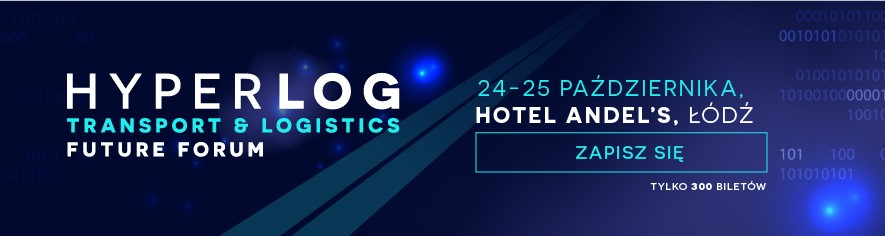