W fabryce Seata w Martorell w Hiszpanii pracuje 125 mobilnych robotów. Przewożą niemal 24 tys. części dziennie, pokonując rocznie 436 tys. km. To kolejny przykład praktycznego zastosowania koncepcji logistyki i przemysłu 4.0.
Według raportu Konferencji Narodów Zjednoczonych ds. Handlu i Rozwoju, na świecie wykorzystywanych jest ok. 2 mln robotów przemysłowych. Blisko połowa z nich znajduje się w zaledwie trzech państwach: Niemczech, Japonii i Stanach Zjednoczonych. To zbyt mało, by mówić o rewolucji – przekonują badacze. Inny obraz wyłania się z analiz firmy McKinsey. Zgodnie z jej prognozami, w samej branży produkcyjnej zautomatyzowane może być już niemal dwie trzecie czasu pracy. Transport oparty na robotach ułatwia i optymalizuje pracę osób zatrudnionych w fabrykach oraz jest w stanie skrócić czas produkcji nawet o jedną czwartą.
Mogą pracować tam, gdzie dla człowieka jest niebezpiecznie
Dowodem coraz powszechniej wkraczającej do intralogistyki automatyzacji i robotyzacji są pojazdy typu AGV (Automated Guided Vehicles). Potrafią np. transportować komponenty z obszaru magazynowego do strefy montażu. Mogą znacznie ułatwić kluczowe operacje obejmujące produkcję just-in-time i just-in-sequence, a także optymalizować przepływy logistyczne w obrębie fabryki, poprawić zarządzanie magazynem.
Są uniwersalne, mogą transportować rozmaite produkty, mogą pracować na okrągło, praktycznie bez przerw. Wózki można stosować w środowiskach, w których warunki higieniczno-sanitarne, mikrobiologiczne lub temperaturowe nie zapewniają pełnej ochrony operatora. Rozwiązania konstrukcyjne AGV są do siebie podobne. Chodzi m.in. o system prowadzenia (taśma magnetyczna); system kontroli (markery) oraz zasilanie (akumulatory). Pojazdy mają rozbudowany system bezpieczeństwa – laserowe czujniki można precyzyjnie programować, w zależności od rozmieszczenia przeszkód w konkretnym pomieszczeniu. Wózki zaopatrywane są również w czujniki wykrywania ładunku.
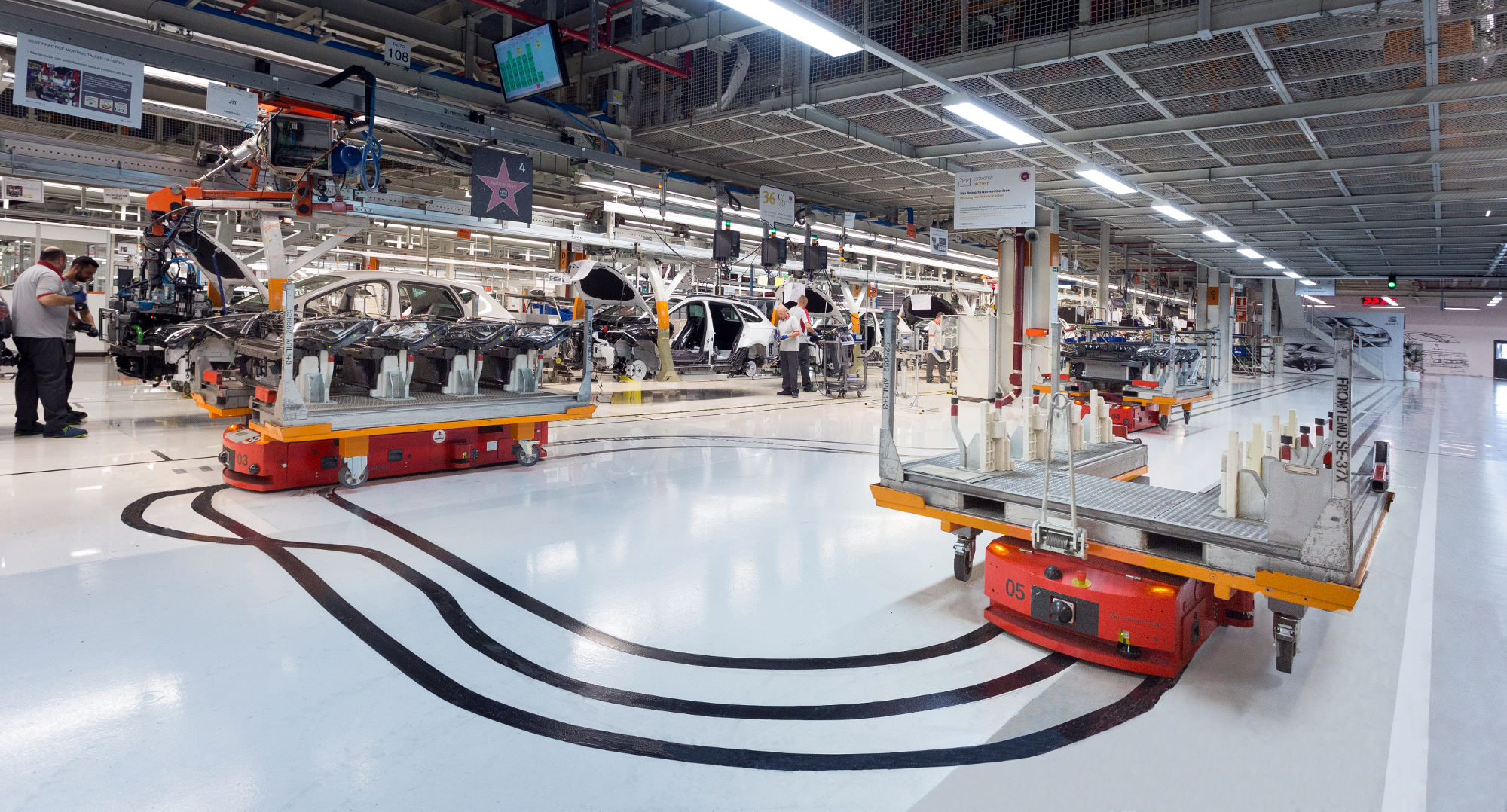
Fot. Seat
W każdym przypadku klucz do efektywności leży w zastosowanym systemie sterowania, a możliwość ingerencji w konfigurację ścieżki roboczej jest podstawowym czynnikiem powodującym rozpowszechnienie tych robotów transportowych. System sterowania może monitorować zarówno wszelkie informacje dotyczące położenia i stanu wózków, jak i zamówienia wysyłane przez system produkcyjny.
Roboty transportowe przewożą nawet 1,5 t. komponentów
Takie właśnie rozwiązania stosuje od niedawna Seat. Działający w tej firmie Easy Mobility Team, pracujący nad nowymi rozwiązaniami, wdrożył bezzałogowe maszyny w fabryce samochodów.
Roboty mobilne w fabryce w Martorell poruszają się po 40 wbudowanych w podłogę wyznaczonych ścieżkach magnetycznych. Pokonanie każdej z tras zajmuje im od 1 do 7 minut. W tym czasie roboty korzystają z układów sterowniczych i automatycznie zwalniają na zakrętach, by nie stracić stabilności podczas przenoszenia ciężkich ładunków i utrzymać bezpieczny dystans.
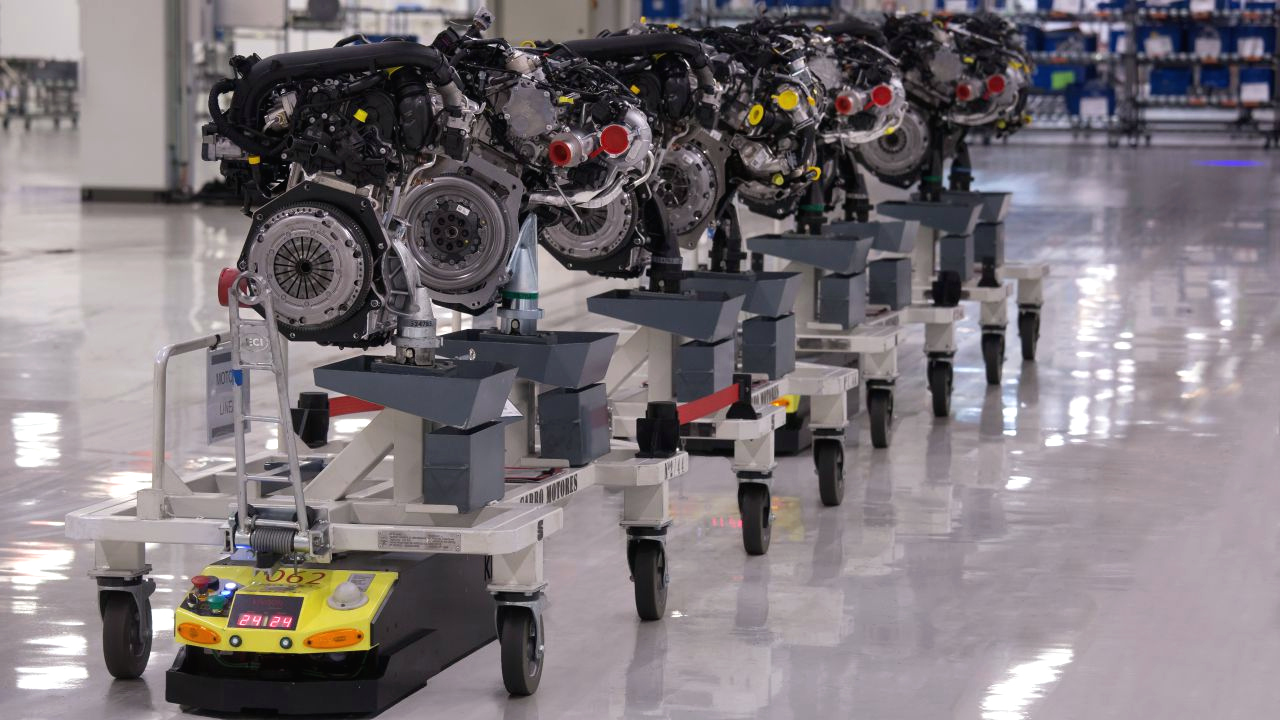
Fot. Seat
Roboty skanują kod kreskowy, aby upewnić się, że transportują odpowiednią część. Następnie dzięki czujnikowi otwierają się drzwi magazynu, umożliwiając maszynom wykonanie powierzonych zadań.
Tak właśnie swój dzień rozpoczynają maszyny, rutynowo mijające się ze sobą i z 7 tys. pracowników fabryki w rytmie przypominającym w pełni zsynchronizowany mechanizm. Automatyczne roboty transportowe przewożą silniki, skrzynie biegów, amortyzatory lub szyby okienne, a ładowność każdego z nich sięga 1,5 t.
Każdego roku roboty pokonują ponad 436 tys. km czyli trasę mniej więcej o jedną trzecią dłuższą niż odległość między Ziemią a Księżycem. Podążając wstępnie ustalonymi ścieżkami, dzięki systemowi kamer (360 st.) maszyny wiedzą, kiedy zatrzymać się na czerwonym świetle i kiedy na swej drodze napotykają pracownika. Są skoordynowane z ruchem pieszych poruszających się po fabrycznych halach i gwarantują ich bezpieczeństwo dzięki ostrzeżeniom generowanym przez światła skanowania laserowego.
Pięciu ludzi czuwa nad ścieżkami robotów
Sterowanie odbywa się zdalnie. Pięciu pracowników z pomieszczenia kontrolnego konfiguruje, a w razie potrzeby zdalnie modyfikuje ustawienia ścieżek robotów transportowych AGV.
Zadaniem scentralizowanego serwera jest natomiast gromadzenie informacji z oprogramowania zainstalowanego w każdym robocie, a ich dokładna pozycja jest wyświetlana w postaci symbolu numerycznego widocznego na ekranach w pomieszczeniu kontrolnym. Zielone światło wskazuje na ich pełną wydajność; światło pomarańczowe oznacza zatrzymanie przez przeszkodę albo ładowanie baterii. System wykrywa również ewentualne problemy techniczne i jest w stanie natychmiast je rozwiązać.
Fot. Seat