Przemysł i logistyka 4.0 obejmuje cały łańcuch, od złożenia zamówienia i dostarczenia komponentów, aż do wysyłki towaru do klientów i usług posprzedażnych. Nowoczesne narzędzia wspierają pracowników, zapewniając dostęp do praktycznie każdej przydatnej informacji, w dowolnym czasie i miejscu. Firmy wdrażające takie nowatorskie rozwiązania mogą obniżać koszty, zyskując istotną przewagę nad konkurencją.
Integracja systemów i ludzi w przemyśle i logistyce 4.0 jest możliwa dzięki internetowi i technologiom informatycznym. Chodzi m.in. o łatwą identyfikację i przepływ informacji, realizowany w pionie: z poszczególnych elementów do systemu informatycznego i z powrotem. W przepływ danych odbywa się także w poziomie – są w niego włączone maszyny zaangażowane w proces, które także przekazują sobie informacje.
Wiedzą o tym m. in. zarządzający firmą Wabco. To globalny dostawca części i podzespołów (głównie z zakresu bezpieczeństwa) dla pojazdów ciężarowych, który zdecydował się na wdrożenie rozwiązania optymalizującego pracę w magazynie, a także przy załadunku oraz rozładunku towarów. Stworzony specjalnie dla Wabco system składa się z trzech powiązanych ze sobą modułów.
Logistyka 4.0 w magazynie
Pierwszy z nich obejmuje rampę i magazyn. W magazynie umieszczane są czujniki, które przekazują do systemu informacje o wypełnieniu danego miejsca paletowego. Operatorzy środków transportu wewnętrznego widzą te dane także na ekranach podwieszonych nad rampami oraz na terminalu, w który wyposażono każdy pojazd. Dodatkowo, na miejscach szybko rotujących, znajdujących się na skrajnych obszarach regałów, umieszczono sygnalizację świetlną, która usprawnia pracę i pomaga operatorom upewnić się, czy dane miejsce jest wolne czy zajęte.
Elementem modułu jest sieciowe rozwiązanie ułatwiające planowanie załadunku. Dzięki niemu, na monitorach umieszczonych nad rampą wyświetlane są szczegółowe informacje dotyczące zadania na danym stanowisku. Drugi moduł obsługuje czynności związane z rozładunkiem i jest oparty na założeniach zbliżonych do części załadunkowej. Z kolei trzeci moduł jest odpowiedzialny za raportowanie. To właśnie on, a dokładniej funkcjonalność związana z analizą raportu, pozwala na usprawnienie funkcjonowania przepływów towarowych przez precyzyjne zidentyfikowanie pomyłek i opóźnień w pracy operatorów i przewoźników.
Każda czynność opisana kodem
Integracja, optymalizacja i automatyzacja przepływu informacji, a w rezultacie uproszczone zarządzanie i poprawa wyników to też efekt wdrożenia nowatorskiego rozwiązania w Fuchs Oil (producent i dostawca m.in. olejów dla pojazdów i maszyn). Duża liczba oddziałów w rozproszonych lokalizacjach pozwala z jednej strony na szybkie dotarcie do klienta, z drugiej natomiast generuje znaczną liczbę danych, których jakość wymagała poprawy.
Ograniczeni czasowo serwisanci nie zawsze mogą sporządzać precyzyjne raporty, które są tak ważne dla firmy po to, by określić zapotrzebowanie na nierzadko bardzo drogie substancje. Pierwszym krokiem do pełnej automatyzacji procesów było znalezienie urządzenia, które z jednej strony spełniałoby funkcję mobilnego komputera, telefonu i aparatu fotograficznego, a z drugiej byłoby odporne na upadki, wilgotność, pył i zabrudzenia. W kolejnym etapie położono nacisk na usprawnienie monitoringu dostaw olejów do klientów, raportowanie wraz z przyspieszeniem otrzymywania informacji zwrotnych, a także wyeliminowanie potencjalnych błędów.
Serwisant, jadąc do klienta, by wykonać zlecone prace chociażby w zakresie uzupełnienia oleju i smarów w maszynach, wie, że każde urządzenie, na którym będzie pracować ma swój kod kreskowy, podobnie jak każde opakowanie oleju i smaru. Taki kod został również przypisany do każdej czynności wykonywanej przez serwisanta.
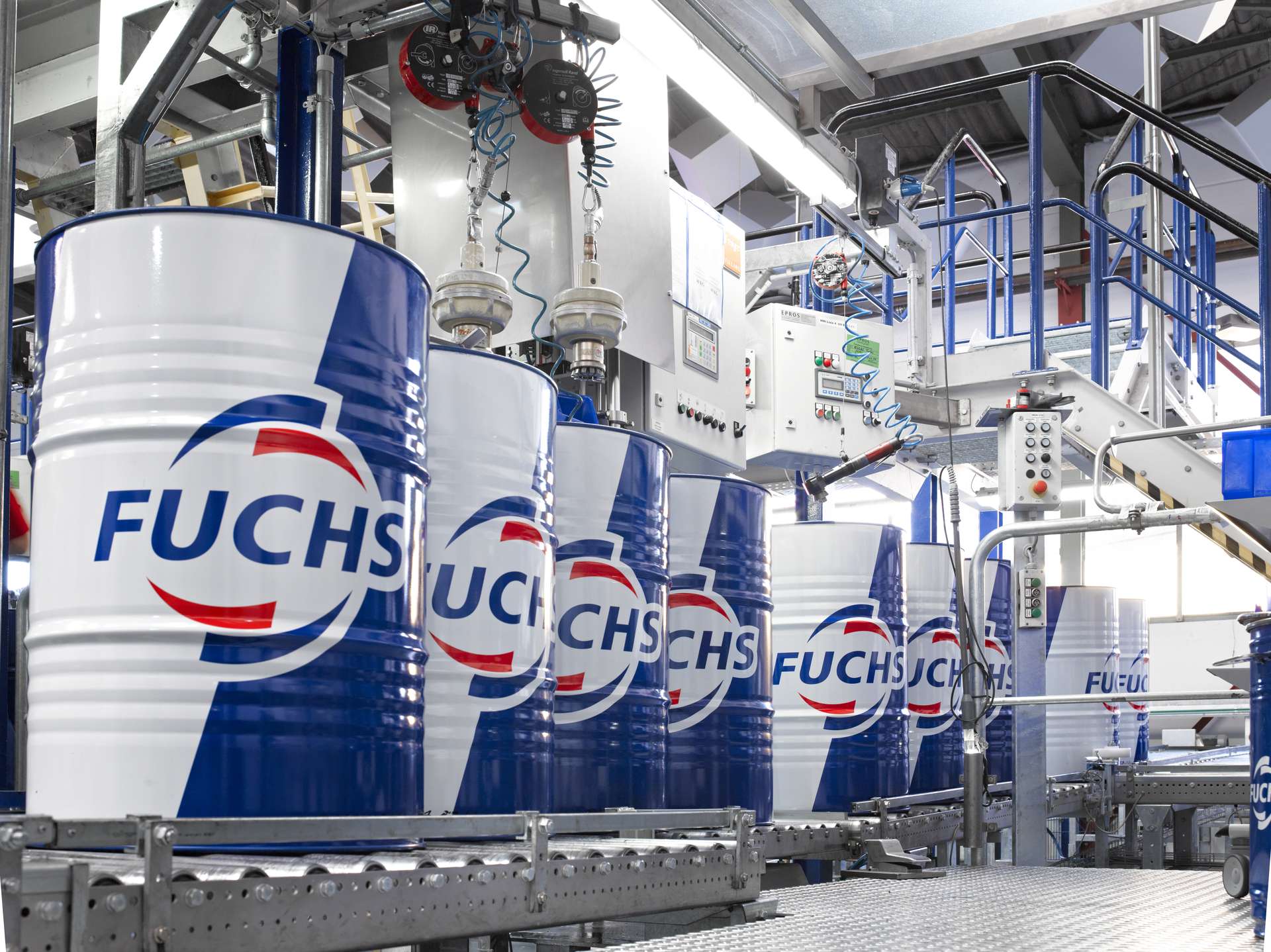
Fot. Fuchs Oil
Jego zadaniem jest zeskanowanie wszystkich kodów, wprowadzenie ilości wykorzystanych materiałów oraz podanie swojej lokalizacji wraz z nazwą klienta. Dodatkowo musi on wpisać ilość poświęconego czasu na zleconą czynność oraz dane osoby zatwierdzającej prace po stronie klienta. Po powrocie do macierzystego oddziału wszystkie dane z wykonanych usług serwisowych są umieszczane w komputerze centralnym, który generuje szczegółowy raport dla klienta uwzględniający m. in. czas wykonywania poszczególnych czynności, ilość zużytych materiałów oraz serwisowanych urządzeń. Raport wraz z fakturą jest wysyłany do klienta. Wszystkie dane są szyfrowane i mogą być również eksportowane do innych oddziałów, np. w celach porównawczych.
Fot. Wabco