W pełni zautomatyzowany magazyn samonośny o wysokości 32 m i zarządzanie towarem za pomocą oprogramowania magazynowego WMS – to najogólniejszy opis kompleksu Multisoft, systemu logistycznego wybudowanego kilka lat temu dla firmy Lakma w Warszowicach na Górnym Śląsku.
Lakma to producent chemii budowlanej, systemów dociepleń, chemii gospodarczej. Posiada jeden z najwyższych w Polsce magazynów wysokiego składowania, który jest w pełni automatyczny i dysponuje miejscem na ponad 15 tys. palet. Jest on częścią wysoko wyspecjalizowanego centrum logistycznego w Warszowicach.
Firma dysponuje rozległą siecią dystrybucji obejmującą większość krajów Unii Europejskiej. W centrum towary są składowane, następuje ich kompletowanie do wysyłki i organizowana jest dystrybucja (we współpracy z największym przewoźnikami w Europie).
Prawie 100 proc. terminowości
Centrum logistyczne jest w pełni zautomatyzowane i ulokowano je na powierzchni około 4,3 tys. mkw. Pełna nazwa projektu brzmi: Multisoft – Samoadaptacyjny Silos z Sensorycznym Software’owym Cyklem Multiplikacji. Chodziło o maksymalnie zoptymalizowanie łańcucha logistycznego. Zdecydowano się wykorzystać zaawansowane technologicznie rozwiązania, aby usprawnić wszystkie etapy procesu magazynowego – od przyjęcia towaru, poprzez magazynowanie i kompletację, aż po wysyłkę gotowych zamówień (uzyskując przepływ 162 palet na godz.).
Centrum Logistyczne realizuje wiele procesów:
– przyjęcie, składowanie, kompletację i wysyłkę towaru na jednostkach logistycznych;
– co-packing;
– cross-docking;
– pełną obsługę klienta dzięki własnym działom Customer Service.
Zarządzanie odbywa się z poprzez WMS, pozwalający konfigurować zamówienia klientów praktycznie bez ograniczeń. Samo centrum jest zresztą stale rozwijane. Zmiany wynikają m.in. z konieczności obsługi wahań wolumenowych sięgających kilkuset procent.
Gospodarze obiektu z dumą mówią o wskaźnikach:
– 99,8 proc. terminowości w zakresie realizacji wysyłek (w trybie AB);
– 0,002 proc. pomyłek w zakresie kompletacji towarów;
– 98 proc. terminowości w zakresie dostaw przewoźnika (tryb AB).
Układnica jednokolumnowa zamiast wózków widłowych
Multisoft ma strukturę samonośną. Obiekt ulokowano na gruncie niezdolnym do przeniesienia dużych obciążeń z konstrukcji, ładunku, od wiatru i śniegu. Z tej racji został postawiony na 254 palach. 220 pali stanowi posadowienie pośrednie dla 50-centymetrowej płyty fundamentowej magazynu samonośnego, natomiast 34 pale są posadowieniem pośrednim hali spedycji zlokalizowanej w bezpośrednim jego sąsiedztwie.
Automatyczny magazyn tworzą cztery korytarze z regałami o podwójnej głębokości po obu stronach. Mają 32 m wysokości i 81 m długości, a także 14 poziomów ładunkowych.
W magazynie na jedną pozycję asortymentową przypada relatywnie duża liczba palet, co umożliwiło zastosowanie regałów o podwójnej głębokości składowania. Rozwiązanie znacząco zwiększyło pojemność magazynu, nie zmniejszając jednocześnie jego wydajności.
W każdym korytarzu pracuje układnica jednokolumnowa, zastępując tradycyjne urządzenia transportu wewnętrznego, głównie wózki widłowe. Przemieszcza palety z prędkością 160 m/min w poziomie i 38 m/min w pionie. Zadaniem układnic jest przemieszczanie towaru między regałami oraz przenośnikami wejściowymi i wyjściowymi usytuowanymi na końcu korytarza. Układnice wyposażono w chwytaki teleskopowe umożliwiające dostęp do drugiego, głębiej położonego miejsca paletowego.
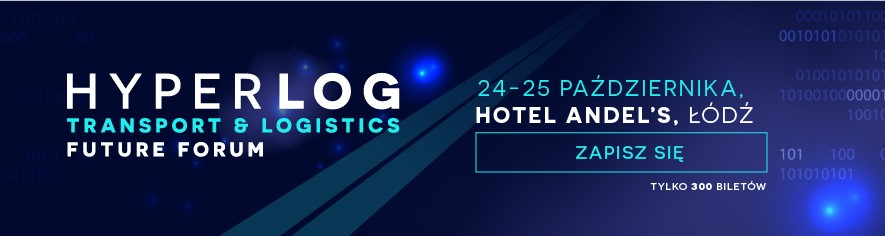
WMS czuwa nad rozlokowaniem towaru
WMS, za pomocą terminali radiowych umożliwia kontrolę wszystkich procesów odbywających się w magazynie, od przyjęcia poprzez składowanie do wydania towaru.
Obok magazynu powstał niższy i mniejszy od niego budynek o wysokości blisko 8 m i powierzchni nieco ponad 2 tys. mkw. Jest to miejsce o bardzo dużym natężeniu ruchu. To tu odbywają się wejścia i wyjścia ładunków oraz kompletacja zamówień.
Każdego dnia do magazynu przyjmuje się 70 palet pochodzących z innych fabryk lub od dostawców. Operatorzy umieszczają palety na przenośnikach wejściowych, którymi towar dociera w pierwszej kolejności do stanowiska kontroli, gdzie sprawdza się wymiary i wagę oraz stan palet pod kątem spełniania wymogów jakości obowiązujących w automatycznym magazynie. Gdy paleta pomyślnie przejdzie kontrolę, dwupaletowy wózek wahadłowy transportuje ją do korytarza wyznaczonego na jej składowanie przez WMS. Jednym z wejść przyjmowane są do magazynu produkty z działającej w sąsiednim budynku fabryki (ok. 130 palet dziennie), z którą magazyn połączony jest łącznikiem nadziemnym.
Kompletacja nawet 600 palet dziennie
Przygotowywanie zamówień, a zatem kompletacja, to jeden z głównych etapów procesu logistycznego odbywającego się w magazynie Lakmy. Przygotowuje się tutaj kilkadziesiąt zamówień dziennie. Palety z produktami przeznaczonymi do kompletacji umieszczane są w kanałach przepływowych, w których przemieszczają się samoczynnie pod wpływem grawitacji od wejścia do końca kanału. Następnie operatorzy pobierają z nich kartony z produktami wchodzącymi w skład poszczególnych zamówień i umieszczają je na wózkach kompletacyjnych. Kierują się przy tym wskazaniami programu WMS wyświetlanymi na terminalach radiowych.
Z magazynu wysyłanych jest średnio 180, a maksymalnie ponad 600 palet dziennie. W większości są to zamówienia wymagające uprzedniego przygotowania, ponieważ każda paleta zawiera różne produkty.
Magazyn opuszczają jednak także palety zawierające jeden typ produktu, które nie muszą być kompletowane. Dla takich zamówień zostały utworzone trzy szybkie wyjścia na jednym końcu trzech bloków kanałów przepływowych do kompletacji. Składają się one z rolkowych przenośników grawitacyjnych umieszczonych na końcu trasy wózków wahadłowych. Budowa przenośników umożliwia pobieranie z nich palet dostarczonych z magazynu przez wózki. Ładunki pobierane przez operatorów wózków są następnie ładowane na ciężarówki.
Fot. Mecalux