DGS Poland, część międzynarodowej grupy William Demant, wytwarza aparaty słuchowe, implanty kostne i urządzenia wspomagające medycynę słuchu. Precyzyjny produkt i jego komponenty wymagają równie precyzyjnej opieki podczas przepływu towaru przez magazyn.
DGS w Polsce funkcjonuje od kilkunastu lat. W fabryce niedaleko Szczecina ulokowano produkcję cyfrowych aparatów słuchowych m.in. takich marek jak Oticon, Bernafon i Sonic, a także aparatury diagnostycznej marek GSI, Interacoustics oraz Maico.
Jedno z kluczowych miejsc w łańcuchu dostaw DGS Poland stanowi magazynowanie. Zadanie nie jest proste, wyroby firmy są bardzo małe i delikatne.
Kilka lat temu kompleks produkcyjny firmy w Mierzynie dopełniono budową zautomatyzowanego centrum dystrybucji. Stąd wyroby gotowe są ekspediowane do ponad 130 krajów świata. Obiekt pełni też funkcję magazynu przyprodukcyjnego.
Packaline stworzy specjalnie dla DGS
Zastąpienie manualnego magazynu z papierowymi listami materiałów automatem oraz kilkukrotne zwiększenie wydajności z zapasem na przyszłość, to kluczowy cel dokonanych zmian.
Główną funkcjonalnością jest śledzenie materiału za pomocą StUnitów i pobieranie materiału z magazynu manualnego w kombinacji z automatyką i Logimatami. Wśród najciekawszych funkcjonalności jest packline (stacja montażowa). Jest to moduł do pakowania przed wysyłką, stworzony specjalnie na potrzeby DGS.
Na powierzchni 4,4 tys. mkw centrum dystrybucji, dla 110 tys. indeksów magazynowych dostępnych jest prawie 2,9 tys. miejsc paletowych, 22 tys. pojemników miniloadu i 600 pojemników w systemie karuzelowym.
Codziennie manualnie oraz z wykorzystaniem systemów pick-by-light i pick-to-tote komisjonowanych jest ok. 13,5 tys. linii na sprzedaż i 1,2 tys. linii na produkcję.
Mnogość wykonywanych operacji, niewielkie rozmiary obsługiwanych elementów, konieczność etykietowania całego materiału przed wydaniem na produkcję to wyzwanie, z którym mierzą się pracownicy centrum dystrybucji. Podstawę funkcjonowania magazynu stanowi 3 tys. pojemników, które każdego dnia opuszczają swoje półki.
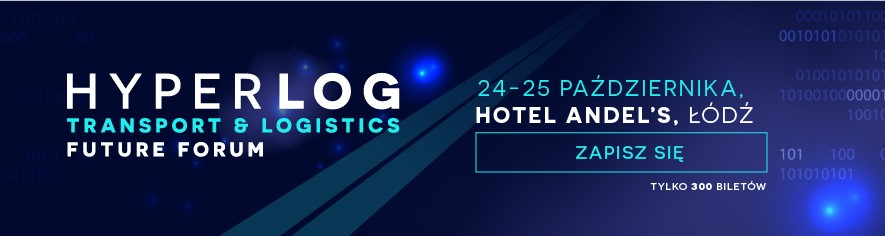
Centrum dystrybucji sterowane przez zmodyfikowany WMS
Spory problem stanowi zróżnicowanie wielkości zamówień, od pojedynczych sztuk do dziesiątków tysięcy gotowych produktów. Wsparcie stanowi system WMS.
Przed wdrożeniem dokonano analizy wizualnej, zmapowano procesy i predykcję działania magazynu. Na podstawie zebranych informacji przygotowano rozwiązania i zmiany, aby móc obsłużyć wszystkie życzenia przyszłego użytkownika. Np. dostawca WMS znacząco zmodyfikował system.
Przede wszystkim dostosowano go do obsługi wielu sposobów kompletacji i pakowania, w zależności od tego kim jest finalny odbiorca produktu. Kompletacja może odbywać się automatycznie lub manualnie. Może być potrzebne złożenie wszystkich komponentów w jeden zestaw lub też indywidualna wysyłka poszczególnych składowych zestawu. Czasami jest wymagane pobranie takich danych jak numery seryjne, a czasami pobierane produkty tego nie wymagają. Liczba kombinacji możliwego sposobu realizacji procesu wydania sprawiła, że system został częściowo “uszyty na miarę”, by sprostać specyficznym potrzebom.
Błędne pobrania zredukowane
Jednym z ciekawszych przykładów modyfikacji jest dostosowanie procesu optymalizacji wypełnienia pojemników kompletacyjnych do charakterystycznych wymogów tej branży. Zestawy aparatów są kompletowane jako oddzielne komponenty, a następnie składane. W całym procesie kompletacyjnym, zarówno same komponenty, jak i złożone już zestawy są transportowane za pomocą przenośników w plastikowych pojemnikach o standardowej wielkości. I tu pojawiło się wyzwanie, ponieważ objętość zestawów jest inna po złożeniu niż przed, a proces logistyczny wymusza, by określona liczba produktów końcowych musiała pasować do tych samych pojemników kompletacyjnych, w których poszczególne komponenty zostały dostarczone na stację montażową zestawów.
Poszczególne komponenty, takie jak: sam aparat, akcesoria, instrukcja w wybranym języku, opakowanie zewnętrzne, itp., są dostarczane w pojemnikach na stację montażową za pomocą przenośników. Tam następuje składanie poszczególnych elementów w zestaw, pobieranie numerów seryjnych lub numerów partii z kluczowych produktów za pomocą skanowania kodów kreskowych, a także wydruk etykiet znakujących finalny produkt.
Złożenie poszczególnych zestawów wymaga wyświetlenia instrukcji montażu “krok po kroku” na ekranie komputera, a często również i zdjęcia gotowego produktu. Wszyscy teamleaderzy mają dostęp do Astro M2 (M2 jest interfejsem użytkownika systemu Astro WMS), który np. pozwala ustalić, kto pracuje nad którą paczką, jaki jest jej status realizacji, lokacja itp. Papierowe listy „zakupów” zmieniły się w pracę na terminalach. Operator nie musi szukać materiału, bo system zawsze wskaże, gdzie ten się znajduje. Spadła liczba błędów i pomylonych materiałów.
Dzięki wdrożeniu systemu WMS wskaźnik OTIF (on time and in full – czyli wskaźnik zgodności dostawy) wynosi średnio 99,47 proc. Liczba błędnych pobrań to 0,5 proc. tzn. statystycznie, jeden błąd pobrania ma miejsce na 200 zamówień.
Fot. Mecalux