Nowy magazyn firmy chemicznej AlzChem, zlokalizowany w Trostbergu, będzie wyposażony w automatyczny system Pallet Shuttle. Obiekt o wysokości 25 m pomieści łącznie ponad 5 tys. palet, a koordynację całego procesu logistycznego zapewni oprogramowanie magazynowe Easy WMS.
Decyzję o zautomatyzowaniu centrum magazynowo-dystrybycyjnego AlzChem wywołała z jednej strony potrzeba przyspieszenia procesów związanych z zaopatrzeniem produkcji, a z drugiej chęć usprawnienia kompletacji i przygotowania towarów do wysyłki.
Po obu stronach jedynego korytarza magazynu zostaną zamontowane dwa bloki regałów z kanałami o długości 10 i 11 m mieszczącymi odpowiednio 7 i 8 palet, które będą obsługiwane przez układnicę i wózek Pallet Shuttle. Magazyn zostanie połączony z zakładem produkcyjnym dwoma przenośnikami: jeden będzie transportował surowce, drugi zaś produkty gotowe.
Praca w nocy bez operatorów
System zarządzania magazynem będzie miał za zadanie koordynować przyjęcia i wydania towaru oraz wyznaczać miejsca składowania każdej palety. Dla zapewnienia odpowiedniej wydajności centrum logistycznego oprogramowane WMS będzie na stałe połączone z systemem ERP wykorzystywanym przez AlzChem. To umożliwi ich dwukierunkową komunikację (wymiana danych).
– Dzięki temu rozwiązaniu będziemy mogli pracować w systemie 24/7, przy czym na nocnej zmianie nie będzie potrzebna obecność operatorów – tłumaczy Andreas Hensel, specjalista ds. zarządzania surowcami w AlzChem.
Półautomatyczny system magazynowania akumulacyjnego do załadunku i rozładunku palet wykorzystuje wózki Pallet Shuttle. W istocie zastępują one typowe wózki magazynowe, skracając czas obsługi i umożliwiając pogrupowanie artykułów według kanałów zamiast według pełnych korytarzy.
Operator przy użyciu tabletu wydaje komendy wózkowi, które przekazywane są za pośrednictwem sieci Wi-Fi. Wózek umieszcza pobrany ładunek w pierwszym wolnym miejscu, maksymalnie zagęszczając składowane palety. Minimalny dystans pomiędzy poziomami składowania pozwala na duże zagęszczenie magazynowanych ładunków. Czujniki wózków kontrolują umieszczanie ładunków, eliminując wolne miejsca w regale. Dzięki temu rzeczywista ładowność (biorąc pod uwagę przepływ wejść i wyjść) jest praktycznie taka sama, jak fizyczna pojemność magazynu.
Szybszy załadunek i rozładunek
Walorem jest też oszczędność czasu. Skrócenie czasu załadunku i rozładunku towarów następuje dzięki wyeliminowaniu pracy operatora wewnątrz kanału. Prędkość jazdy wózka wynosi 90 m/min bez obciążenia i 45 m/min z obciążeniem. Czas podnoszenia, to zaledwie 2 sekundy. Wykonując jedno polecenie, wózek może opróżnić lub zapełnić cały kanał.
Dzięki zastosowaniu Pallet Shuttle w każdym kanale można składować inną jednostkę, co umożliwia większe zróżnicowanie produktów w magazynie. Stosowana jest generalna zasada “produkt do operatora” (ładunek przemieszcza się w kierunku operatora, nie musi on “spacerować” po obiekcie). W trakcie wykonywania polecenia przez wózek Pallet Shuttle operator wybiera kolejną paletę, dzięki czemu jest zachowana ciągłość cyklu. W zależności od temperatury i obciążenia wózek może pracować nieprzerwanie do 10 godzin. System praktycznie eliminuje ewentualne błędy, użytkownik docenia też funkcję inwentaryzacji (wózek przelicza palety składowane w kanale).
Zwraca uwagę też wszechstronność zastosowań. Wózek ma wbudowane czujniki, które wykrywają i obsługują różne rodzaje palet. Np. model 1012 obsługuje europalety o szerokości 800 lub 1000 mm, model 1212 europalety o szerokości 800, 1000 lub 1200 mm.
Wszystkie wózki mogą pracować w trybie LIFO (last in-first out) lub FIFO (first in-first out). Operator wybiera odpowiedni tryb na tablecie. Platforma wózka jest zaprojektowana do obsługi palet ze strzałką ugięcia, tzn. maksymalnym dopuszczalnym odkształceniem do 25 mm. Dopuszczalne obciążenie wynosi 1,5 t na paletę. System jest łatwy w rozbudowie, w sytuacji gdy wymagana jest większa wydajność instalacji wystarczy zwiększyć liczbę wózków.
Fot. Mecalux
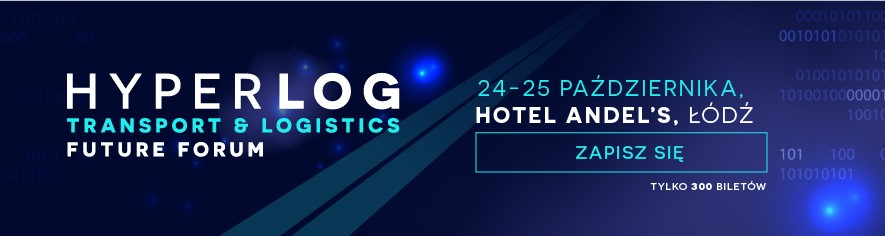