CCC ma solidną pozycję na rynku obuwniczym. Grupa ma sieć ponad 900 salonów, o powierzchni przekraczającej pół miliona mkw i jest obecna w kilkudziesięciu krajach. Przez swoją spółkę zależną eobuwie.pl działa też na rynku e-commerce. Rocznie ekspediuje ponad 50 mln par butów, a to wymaga sprawnej logistyki.
Rozwój nie byłby możliwy bez inwestycji w logistykę. Proces trwa od lat. Od niedawna w centrum dystrybucyjnym CCC wózki widłowe mają możliwość korzystania z automatycznego sterowania, dzięki zintegrowaniu systemu zarządzania magazynem z oprogramowaniem środków transportu wewnętrznego. Do jej wdrożenia konieczne było dokładne “zmapowanie” przestrzeni magazynowej i udostępnienie interfejsów przez producenta widlaków.
Po to, by uzyskać taki rezultat, należało zintegrować WMS (Warehouse Management System) z funkcją samodzielnego poruszania się wózków. Aby zwiększyć efektywność rozwiązania system zarządzania skomunikowano z oprogramowaniem sterującym wózkami w taki sposób, że może przekazywać im informacje o lokalizacji konkretnych produktów w magazynie. Wózki mogą dzięki temu samodzielnie nie tylko pokonać trasę do docelowej lokalizacji, ale również podjąć ładunek i transportować go do wskazanego punktu odbioru. Rolę operatora ograniczono do minimum, jego zadaniem jest jest nadzór i potwierdzanie operacji realizacji przez skanowanie kodów kreskowych.
To jedno z kluczowych założeń, w CCC podkreślają bowiem, że automatyzacja procesów zarządzania i pracy jest realizacją jednego z priorytetów grupy, czyli zwiększania bezpieczeństwa i wyeliminowania zdarzeń potencjalnie niebezpiecznych, do jakich może dochodzić z udziałem pracowników. Sprawa bynajmniej nie jest prosta uwzględniając specyfikę centrum dystrybucyjnego CCC.
– Centrum dystrybucyjne obejmuje 111 tys. miejsc paletowych, a zastosowane wózki mają możliwość obsługi regałów o wysokości do 17,5 m. Przy takiej skali przedsięwzięcia nie ma miejsca na pomyłki. Wdrożenie rozwiązania PSI i Jungheinrich poprawiło szybkość operacji przy jednoczesnym zagwarantowaniu maksymalnego bezpieczeństwa – komentuje Julita Barnowska, dyrektor ds. Logistyki w CCC.
Wąskie i wysokie korytarze
Specyfika magazynu wysokiego składowania wymaga zatem wyjątkowej precyzji i niezawodności jeśli chodzi o transport, tak ze względu na rozmiar obiektu (55 tys. mkw), jak i relatywnie niewielkie odstępy pomiędzy regałami.
Dostawcą wysokich regałów, a także środków transportu potrafiących je obsługiwać (za- i wyładunek) jest Jungheinrich. W jednostkach dystrybucyjnych CCC znalazły zastosowanie maszyny typu VNA – wózki systemowe do pracy w bardzo wąskich korytarzach. To modele EKK 516k podnoszące ładunki na wysokość 13,5 m, jak również EKX 516 z masztami o maksymalnej wysokości podnoszenia 17,5 m. Szczególną rolę mają do spełnienia wózki systemowe EKX z podnoszoną kabiną (wyposażone w bezobsługowy napęd synchroniczny 80 V). Ponieważ przy podnoszeniu na wysokość 17,5 m mogą pojawić się drgania na maszcie i w kabinie, spowodowane choćby minimalnymi nierównościami posadzki zastosowano system stabilizacyjny FloorPro, który je redukuje. Zastosowano też moduł sideshift PLUS umożliwiający pracę w korytarzach o różnej szerokości.
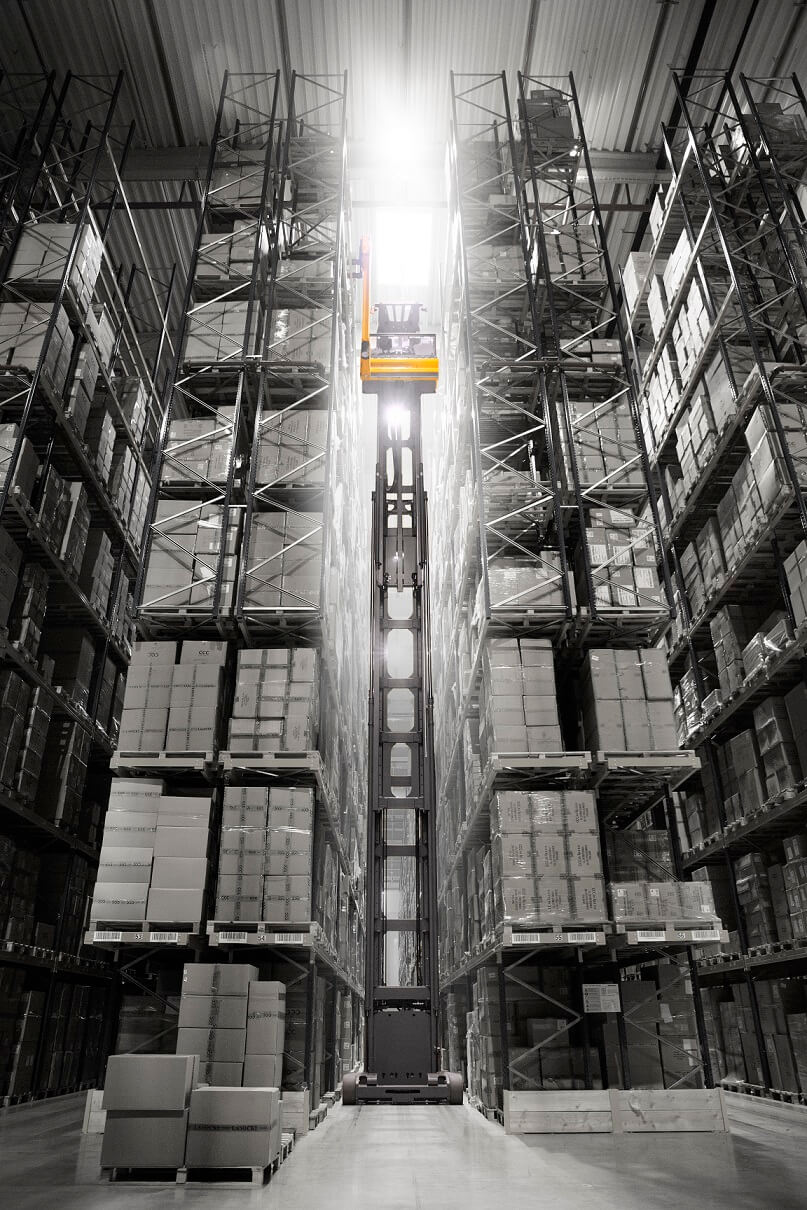
Ponieważ maszyny napędzane są elektrycznie, ich wdrożenie wymagało budowy stacji ładowania akumulatorów, w technologii litowo-jonowej. Wózki mogą pracować zarówno w nowo powstałej, jak i użytkowanej wcześniej części magazynu.
– Jeśli klient korzysta z wózków z funkcją automatycznego sterowania, jesteśmy w stanie dodać do systemu warstwę sterującą tymi pojazdami. Integracja różnych rozwiązań w ramach systemu zarządzania magazynem gwarantuje, że klient będzie mógł w czasie rzeczywistym gromadzić i przetwarzać wszystkie dane o tym, co właśnie dzieje się w magazynie i w konsekwencji zwiększać wydajność i niezawodność – mówi Sławomir Budzaj, competence center manager w PSI Polska.
WMS nadzoruje nie tylko kompletacje
Wykorzystywany przez CCC PSIwms zapewnia bieżącą komunikację między serwerem, a terminalami wózków, dzięki czemu ciągle monitoruje ich pozycję.
To kolejny etap procesu automatyzowania logistyki w CCC. Główna faza projektu obejmuje obsługę większości podstawowych procesów magazynowych oraz integrację z systemem ERP, systemami firm kurierskich i złożoną automatyką magazynową (obejmującą m.in. sortery oraz automatyczny magazyn kartonowy typu miniload). WMS odpowiada też za usprawnienie procesów w strefach przyjęcia, kompletacji i wydania z magazynu oraz śledzenia transportu. Kolejne kroki obejmują procesy związane m.in. z obsługą rynku e-commerce.
Fot. Jungheinrich
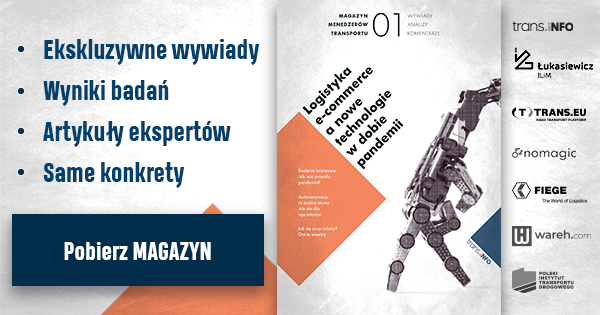