Robot może być przyczynkiem do budowy całego środowiska logistycznego opartego na danych. Wykorzystując go można uzyskać dostęp do bardzo precyzyjnych danych i procesów. A dzięki temu można na bieżąco monitorować różne etapy obsługi, np. czas realizacji przepływów towarów, między innymi uśredniony czas dostawy i odbioru. Można ponadto szacować wielkość pól buforowych. O visibility w magazynie, kosztach robotów i kontrowersjach związanych z zastępowaniem przez te urządzenia ludzi rozmawiamy z Jackiem Królikiem, CEO VersaBox – firmy, w którą fundusze venture capital zainwestowały 11 mln zł.
Dorota Ziemkowska, Trans.INFO: Podkreślacie często, że wasze roboty działają na zasadzie autonomicznej armii mrówek. Obrazowe określenie, tylko co ono dokładnie oznacza?
Jacek Królik, CEO VersaBox: Oznacza, że każde z urządzeń jest wyposażone w cyfrowy mózg, czyli rodzaj sztucznej inteligencji, nazywanej przez nas nawigacyjną. Dzięki niemu roboty są w stanie obserwować i interpretować otoczenie. Korzystają z sensorów, kamer i czujników. Ponadto z pomocą mapy terenu, którą mają, są w stanie zidentyfikować swoje położenie.
Potrafią poza tym podejmować różnego rodzaju działania. Omijają przeszkody lub zatrzymują się przed nimi, szukają alternatywnych dróg. Co więcej, niektóre z tych reakcji mają charakter selektywny, a to oznacza, że inaczej robot reaguje zauważając idącego człowieka, a inaczej nieruchomy przedmiot lub nadjeżdżający wózek widłowy.
Skąd to wiedzą? Mają wgrywane pewne scenariusze zachowań, czy uczą się na bieżąco?
Robot obserwując otoczenie jest w stanie rozróżnić kilka podstawowych kategorii obiektów. Po pierwsze, elementy nieruchome, tj. ściany, słupy, które są dla niego punktem odniesienia w nawigacji. Po drugie, elementy nieruchome, ale zmienne. A więc leżące paczki i stojące palety, które najczęściej po prostu się omija.
Po trzecie, obiekty ruchome o różnej charakterystyce. To np. wózek widłowy, który potencjalnie jest elementem, który zagraża robotowi. Ten więc na jego widok powinien się zatrzymać lub nawet wycofać. Innym jednak elementem jest człowiek, który wymaga nieco innych reakcji. Z jednej bowiem strony należy utrzymać dystans, czasami nawet zatrzymać się. Jednak z drugiej strony wiadomo, że człowiek, który się porusza i widzi robota, sam także zaczyna go omijać. W związku z czym robot reagując na człowieka, musi brać pod uwagę fakt, że ten także zacznie wykonywać jakiś manewr. Nie mogą się przecież zdarzyć.
To tylko kilka przykładów. Istnieje wiele reguł organizacji ruchu robotów w fabryce czy magazynie. I oczywiście robot się do nich stosuje. Natomiast w pewnych sytuacjach może te reguły łamać, np. omijając przeszkodę, która stoi na wyznaczonej trasie, albo wybierając alternatywną ścieżkę w sytuacji, gdy poruszanie się tą, która była wyznaczona, jest niemożliwe.
Rozumiem, że robot decyzję z tym związaną podejmuje samodzielnie?
Tak, jest autonomicznym urządzeniem. Jak to dokładnie działa? Generalnie robot służy do realizacji pewnego procesu transportowego. W przestrzeni magazynowej lub produkcyjnej jest zaznaczona pewna liczba punktów, z których zabiera zamówienia i punktów, do których je odwozi. Istnieje też system nadrzędny wobec robota, który przydziela mu tzw. misje transportowe, czyli przewiezienie ładunku w danym reżimie czasowym.
Robot, kiedy otrzymuje taką misję, autonomicznie podejmuje decyzje, jak ją wykona. Żaden człowiek nie siedzi za monitorem, nie ma żadnego zewnętrznego programu, który tym urządzeniem steruje. Oczywiście robot informuje systemy nadrzędne o tym, gdzie jest, co robi, czy ma problemy, jaką trasą jedzie, kiedy dostarczy towar. Te informacje są dostępne, ale to nie zmienia faktu, że samo urządzenie działa autonomicznie.
Czyli nawet, jeśli ma do wykonania kilka misji, każdą może zrealizować nieco inaczej, biorąc pod uwagę warunki, jakie panują akurat w magazynie.
Oczywiście. Co więcej, zakładamy, że robotów jest wiele w danej przestrzeni. Zachodzą więc pomiędzy nimi interakcje, zupełnie jak we wspomnianej już armii mrówek. Roboty mogą się spotykać na trasach, a więc i omijać, by nie dochodziło to zakleszczeń lub kolizji. Ponadto są zamienne, co oznacza, że jeśli jest pewna ich grupa, która jest tak samo skonfigurowana, to nie ma znaczenia, który z nich podejmie się danego zadania transportowego. Natomiast ich system nadrzędny musi dbać o to, żeby były mniej więcej równomiernie obciążone pracą, naładowane prądem, itp.
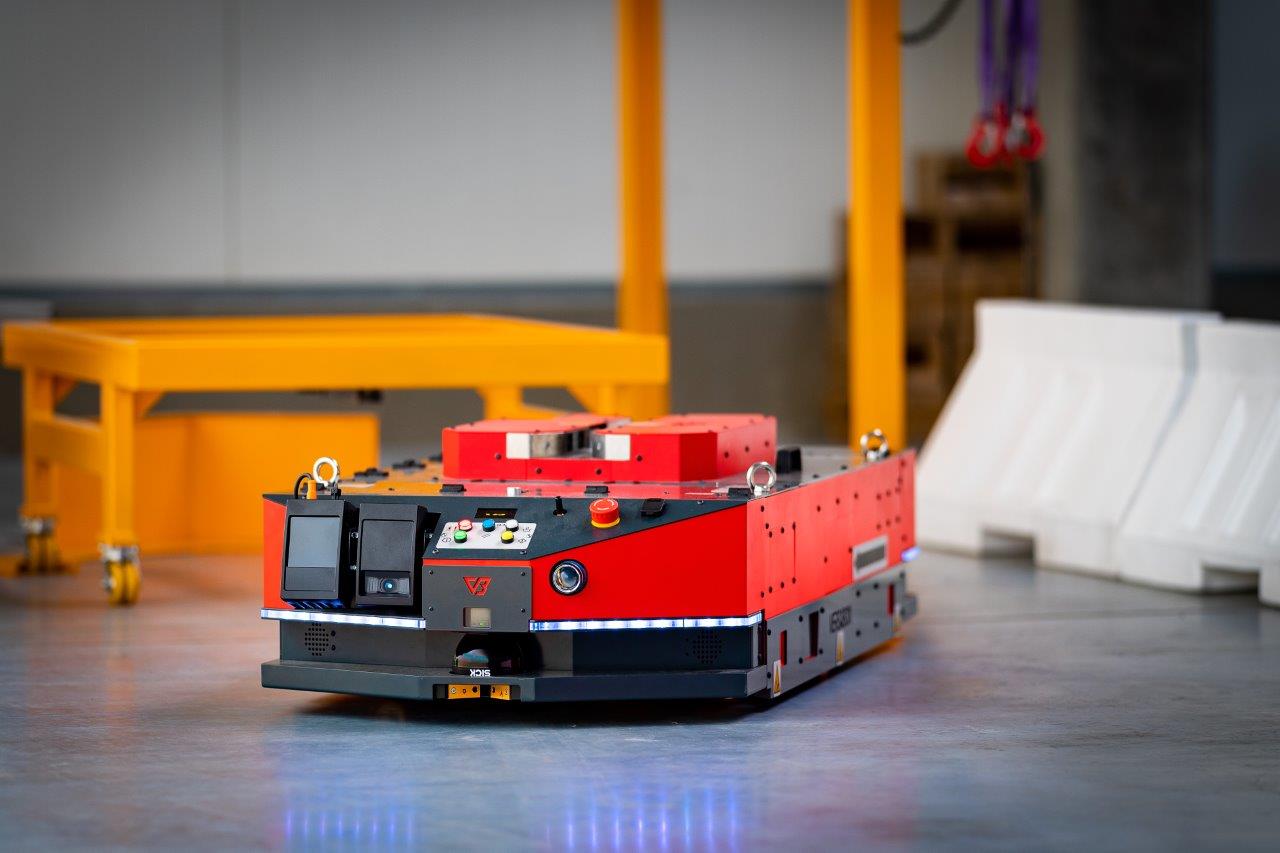
Wspomniał Pan, że roboty tworzą wirtualną mapę obiektu, po którym się poruszają. Czy przy jej powstawaniu człowiek jest już niezbędny?
Mapę robot tworzy sam. Zwykle dzieje się to w ten sposób, że kiedy w magazynie lub hali produkcyjnej przeprowadzana jest pierwsza instalacja systemu robotycznego, specjalista ds. wdrożeń podłącza robota i objeżdża nim cały teren budynku. Urządzenie wówczas samo tworzy mapę, którą zapamiętuje. Następnie może ją dzielić ze wszystkimi robotami, które pracują w tym miejscu. Później wszystkie mają możliwość stałego aktualizowania tej mapy i przekazywania sobie informacji na jej temat.
Rozumiem, że biorąc pod uwagę tę mapę, człowiek może już zaprogramować te roboty, bo to przecież on odpowiada za przygotowanie takich komunikatów, jak “podjedź do punktu”, “zaczekaj w nim 20 sekund”, itp.
Rzeczywiście, ludzie na takiej mapie mogą zaznaczyć wszystkie punkty typu pick up i drop off. Następnie, uwzględniając ograniczenia nakładane przez klienta, związane z prędkością, trasami, zakazanymi miejscami, itp., buduje się mapę procesów, czyli reguł obowiązujących roboty. Później już pozwala się urządzeniom autonomicznie realizować wspomniane wcześniej misje transportowe.
Gdzie w tym wszystkim miejsce na technologię wirtualnego bliźniaka, z której podobno też korzystacie?
W dwóch miejscach. Po pierwsze, kiedy zbudujemy mapę magazynu i zaznaczymy wszystkie punkty podejmowania i odkładania ładunku, to zanim wstawimy do tej przestrzeni choć jednego robota, jesteśmy w stanie właśnie na cyfrowym bliźniaku zasymulować cyfrowo działanie całej floty.
Korzystamy z oprogramowania, które jest pełnym symulatorem ruchów robota. Co to znaczy? Większość używanych dziś programów symulacyjnych opiera się na prostych statystykach ruchu. I to na ich podstawie kalkuluje się liczbę niezbędnych robotów a także przepustowość całego systemu transportowego. Nasz symulator pozwala na to, żeby na planie fabryki lub magazynu odwzorować rzeczywiste działanie floty, przez osadzenie oprogramowania robotów w wirtualnym świecie. Dzięki temu przeprowadzamy symulację działania wielu robotów, w bardzo konkretnych warunkach, u konkretnego klienta, zapewniając mu żądaną przepustowość.
Ten software, który symuluje przebieganie procesów realizowanych przez roboty, może później bazować na danych, które są przez te urządzenia zbierane. A więc po pierwszej symulacji i wdrożeniu systemu, nasze roboty zaczynają działać i zbierają dane o rzeczywistych przebiegach tych procesów. Dzięki tym rzeczywistym danym jesteśmy w stanie w dalszym ciągu (dzięki powstałemu cyfrowemu bliźniakowi) optymalizować działanie takiej floty, by podnosić jej wydajność.
A więc modyfikować pracę robotów w oparciu o dane, które same zbierają?
Tak. Mamy do czynienia z realizowaniem w praktyce logistyki opartej na danych.
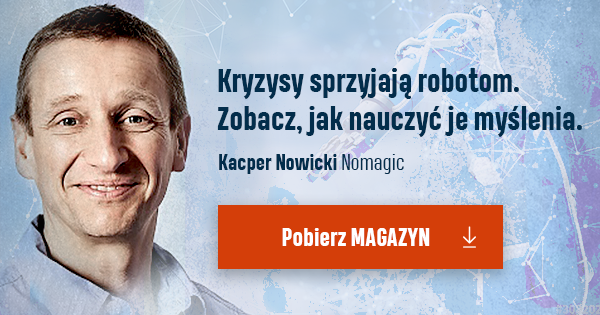
Wasze roboty są też w stanie wykorzystywać dane, które są zbierane na styku operacje magazynowe – produkcyjne albo operacje magazynowe – dostawcy? Pytam, bo przecież magazyn, w którym się poruszają, jest zwykle tylko punktem przesiadkowym towarów.
Technicznie rzecz biorąc, jest to możliwe. Bo trzeba pamiętać, że robot jest po prostu komputerem na kółkach.
Natomiast w praktyce sam robot raczej tego rodzaju informacji nie potrzebuje. Jest podpięty do systemu nadrzędnego, czyli programu Fleet Manager, a ten po pierwsze, steruje flotą robotów, a po drugie, sam jest połączony z systemami nadrzędnymi klienta (magazynowymi lub produkcyjnymi). I tak naprawdę to one wiedzą, co dokładnie robot wiezie i to im ta wiedza jest najbardziej potrzebna.
Pamiętajmy jednak, że robot ma otwartą architekturę, w związku z czym może być wzbogacony o różnego rodzaju urządzenia, które są w stanie przekazywać mu różne informacje. Na przykład robot jest w stanie odczytać jakieś dane z ładunku, który jest na nim umieszczony. To jednak, znów, będzie informacja istotna nie dla samego robota, ale dla dalszych systemów magazynowych i produkcyjnych.
Robot może być chyba jednak przyczynkiem do budowy całego środowiska logistycznego opartego na danych. Tak wnioskuję po czymś, co sami piszecie na stronie – że wykorzystując te urządzenia można uzyskać dostęp do bardzo precyzyjnych danych i procesów, skutkiem czego można na bieżąco monitorować różne etapy obsługi, np. czas realizacji przepływów towarów, między innymi uśredniony czas dostawy i odbioru. Można ponadto szacować wielkość pól buforowych… Czyli generalnie zapewniać jakąś formę visibility, mam rację?
Tak, oczywiście. Robot działając, przekazuje wszystkie informacje o zadaniach, które wykonuje, o swojej prędkości, o przewidywanych czasach przybycia na miejsce, regularnie informuje o tym, że napotyka jakieś przeszkody. W związku z czym jest możliwe zbudowanie bardzo precyzyjnych tzw. heatmap, związanych z jego działaniem w magazynie. A to pozwala na kolekcjonowanie bardzo precyzyjnych danych dotyczących przebiegu całego procesu logistycznego.
Również chyba prognozowania, gdzie są w tej obsłudze wrażliwe miejsca.
Dokładnie. Już sama symulacja procesów logistycznych, o której wspominałem, dąży do tego, żeby te wszystkie “gorące” miejsca zawczasu wykryć i rozładować. A więc by nie dochodziło do tego, że w pewnych miejscach natężenie ruchu jest zbyt duże i efektem jest pojawienie się wąskich gardeł w procesie logistycznym. Później flota robotów na bieżąco przekazuje tego typu informacje, co pozwala na reagowanie na ewentualne opóźnienia.
Jak przygotować magazyn do wdrożenia takich robotów?
Przede wszystkim magazyn musi spełniać pewne warunki techniczne, a więc mieć w miarę gładką podłogę, rozsądnie szerokie i przejezdne korytarze. Druga rzecz – trzeba pamiętać, że roboty sprawdzają się w procesach transportowych, które są regularne. Czyli kiedy możliwe jest wytyczenie regularnych ścieżek oraz istnieją zidentyfikowane cykle transportu. Jeśli tak jest, należy sporządzić layout magazynu i zdefiniować niezbędne elementy procesu logistycznego, które się tam dzieją, i za które odpowiadałby robot.
Ważna jest również infrastruktura towarzysząca. Zwykle robot podejmuje towar z automatycznie działającego regału, stojaka albo rolotoku, a czasem ze stojaka ładowanego na przykład przez wózek widłowy. Te elementy też muszą być przygotowane.
Na koniec trzeba pamiętać, że system do zarządzania robotem musi być połączony z systemami nadrzędnymi klienta, które przydzielają mu misje transportowe. Takie połączenie jest możliwe za pomocą software’owych wtyczek i odpowiedniego rodzaju API.
Ile czasu zajmuje wdrożenie robota do pracy?
Samo zbudowanie mapy i późniejsza konfiguracja robota jest dość prostą operacją, która zajmuje kilka godzin.
Zazwyczaj bardziej skomplikowane jest zbudowanie elementów mechanicznych, które łączą infrastrukturę transportową naszych robotów z magazynową lub produkcyjną. Chodzi na przykład o postawienie urządzeń, które dokonują przeładunku między taśmą produkcyjną a robotem. Na koniec dochodzi integracja systemu robota z systemami zarządczymi klienta.
Ogólnie całe wdrożenie zajmuje od dwóch do kilku tygodni.
Czas to pierwsza z dwóch rzeczy, najbardziej interesujących dla firm, które myślą o wdrażaniu robotów. Druga rzecz to koszty. Piszecie, że żeby sprawdzić, czy opłaca się korzystać z robotów, wystarczy porównać pełne koszty zatrudnienia jednego pracownika magazynowego w skali roku, a następnie zestawić je z kosztem jednego robota. To ma dać nam prostą odpowiedź. Tylko żeby rzeczywiście była prosta, proszę o koszt jednego robota.
Radzimy klientom, by każde myślenie o wdrożeniu robota zaczynali od zasymulowania procesów intralogisytcznych za pomocą naszego symulatora, o którym wspominałem. Bo dzięki temu można dokładnie określić, jaka ich liczba jest niezbędna. Kiedy już wiemy, ile potrzeba robotów, i znamy ich cenę, umiemy przewidzieć, jakie są koszty adaptacji infrastruktury, a następnie jesteśmy w stanie zdefiniować cały budżet kosztowy, czyli ile to wszystko będzie klienta kosztowało.
Tylko że ja nie znam kosztu jednego robota.
Ale Pani chce poznać kwotę?
Tak.
My nie ogłaszamy cenników….
To może inaczej. Skoro nie chce mi Pan zdradzić konkretnych kosztów wdrożenia takiego robota, to może opowie o przykładowej realizacji, z której wyniknie chociażby informacja dotycząca zwrotu z inwestycji?
Jesteśmy w stanie policzyć, ile potrzebujemy robotów, jaką infrastrukturę, jakie będą koszty wdrożenia. To nam daje niezbędny budżet na wdrożenie. Z drugiej strony, by zobaczyć, czy jest to opłacalne, zastanawiamy się, jakie są koszty danego procesu intralogistycznego, przy założeniu, że realizujemy je tak, jak dziś. A więc za pomocą ludzi i na przykład wózków widłowych.
Spróbujmy więc zrobić prostą kalkulację kosztów pracy człowieka, powiedzmy, nie w Polsce, tylko w niedrogiej części Niemiec. Mogę?
Jasne, tylko czemu nie w Polsce?
Dlatego, że z naszym produktem celujemy przede wszystkim w zagranicę.
Celujecie, ale jeszcze was tam przecież nie ma.
Dziś pracujemy przede wszystkim dla polskich fabryk i magazynów, należących do międzynarodowych koncernów. Co oznacza, że następnym celem, który już dziś realizujemy, w tej rundzie inwestycyjnej, jest wyjście do fabryk zagranicznych.
Mamy już na koncie wdrożenia w fabrykach w Czechach, ale mamy też wiele rozmów z innymi zakładami znajdującymi się poza Polską.
We wrześniu firma VersaBox została wsparta kwotą 11 mln zł przez fundusze venture capital: Fidiasz EVC, SpeedUp Energy Innovation, Movens VC i RST Ventures for Earth.
Rozumiem, że chce mi Pan podać przykład niemiecki, bo ma najświeższe dane, tak? W końcu sami przyznajecie, że celujecie obecnie przede wszystkim w Niemcy…
Tak. Otworzyłem kalkulator i policzymy. Weźmy koszt pracownika, który dostaje 10 euro za godzinę. Taka jest niewygórowana cena dla niewykwalifikowanego pracownika w Niemczech.
Razy 8 godzin, to daje 80 euro. Przy trzech zmianach i 20 dniach roboczych w miesiącu, to daje 4 800 euro. Rocznie – około 57 tys. euro kosztu bezpośredniego. Do tego trzeba doliczyć infrastrukturę, chorobowe, urlopy… Szacuję, że jeszcze z 50 proc. kosztów, co oznacza, że koszt trzyzmianowej pracy w danym procesie wynosi blisko 86 tys. euro rocznie. Zapewniam panią, że koszt wdrożenia naszego robota i rocznej eksploatacji jest niższy.
Można zestawić 1:1 pracownika i robota?
Czasami tak, czasami nie. Generalnie rzecz ujmując, tak.
Jeden robot wystarczy, by inwestycja była opłacalna?
Zdecydowanie namawiamy klientów, by inwestowali we floty robotów. Owszem, można kupić jednego, by nauczyć się go obsługiwać, zebrać pierwsze statystyki. Natomiast później działanie jednego nie ma specjalnego sensu, bo wówczas pracuje otoczony wąskimi gardłami, które dramatycznie obniżają jego wydajność. Mowa na przykład o ludziach, którzy wchodzą z nim w kolizję, zastawiają drogę, blokują przejazdy.
Rekomendujemy więc flotę sześciu, dziewięciu lub dwunastu robotów. To daje możliwość osiągnięcia odpowiedniej skali, która z kolei gwarantuje odpowiednią wydajność procesów.
Co się dzieje z pracownikami, którzy zostali zastąpieni przez roboty?
Chyba nigdy nie spotkaliśmy się z sytuacją, w której ktoś byłby zwolniony z powodu robota.
Ludzie jako mądrzejsi od robotów, są predestynowani do nadzoru nad nimi, planowania ich pracy, czy ich konfigurowania. To na tyle twórcza praca, angażująca, że daje lepszy zwrot jakościowy z pracy. Ludzie nie nadają się do wykonywania prostych, nużących zadań. To ich męczy, nudzi i obniża ich zaangażowanie.
Na jakiej zasadzie nadzór nad robotami jest niezbędny? Mówił Pan, że są one całkowicie autonomiczne.
To urządzenia techniczne, więc nie możemy oczekiwać, że są rodzajem Perpetuum Mobile. Niekiedy wymagają interwencji ludzi. Musimy analizować proces ich działania, rekonfigurować go, gdyż czasami na produkcji pojawiają się zmiany. Pojawiają się uszkodzenia robotów… To wszystko wymaga nadzoru wykwalifikowanej kadry.
Wróćmy jeszcze do zwrotu z inwestycji. Określacie ją na poziomie 18-24 miesięcy. To szacunki przygotowanie w oparciu o doświadczenia klientów?
Zwykle klienci nie rozpatrują inwestycji, jeśli okres zwrotu jest dłuższy niż 24 miesiące. Natomiast zauważyliśmy, że w praktyce nie ma specjalnych trudności, by to osiągnąć w ciągu 18 miesięcy, choć są sytuacje, kiedy udaje się szybciej. IDC, znana firma analityczna, opublikowała niedawno raport Industry Spotlight, z którego wynika, że ponad 65 proc. projektów robotyzacji zwraca koszty w czasie poniżej 2 lat, a ponad 70 proc. charakteryzuje się dwucyfrowym wskaźnikiem rentowności.
Udaje się to osiągnąć dzięki różnicy między kosztami korzystania z robotów i ludzi?
Tak.
Tylko skoro Pan mówi, że pracowników nikt nie zwalnia, to oni ciągle siedzą w firmie, i na nich nadal rocznie jest przeznaczane wyliczone przez Pana ponad 80 tys. rocznie. Mimo to dodatkowe kupowanie robotów i tak się opłaca?
Nikt tych ludzi nie zwalnia, co nie oznacza, że siedzą w zakładzie. Z tego, co wiem, rotacja w fabrykach i magazynach w Polsce i zagranicą jest dość duża. Starzy pracownicy odchodzą i pojawia się problem w znalezieniu nowych. Umieszczenie w tym miejscu robotów daje efekt taki, że przestajemy tracić pracowników, bo zostają tylko ci, którzy wykonują wysoko wykwalifikowaną pracę nadzoru nad flotą tych urządzeń. A kierownicy zakładów nie muszą rozpaczliwie szukać nowych pracowników do najprostszych zadań.
Natomiast wracając jeszcze do kalkulacji zwrotu. Nie zapominajmy, że żyjemy w czasach, które charakteryzują się dużą zmiennością procesów produkcyjnych i transportowych. A to oznacza, że konieczne jest elastyczne przerabianie zakładów i magazynów. Jeśli system transportowy bazuje tylko na ludziach, to jest ogromne ryzyko pomyłek, zwłaszcza, jeśli nie są wysoko wykwalifikowani. Z kolei, jeśli zbudujemy strukturę tylko na elementach stałych – taśmociągach, przesuwnicach – to choć będzie to rozwiązanie tanie, to trudne do zmiany. A zmiana to dodatkowy koszt, zwykle niebagatelny.
Tymczasem robot jest urządzeniem, które wnosi pewien element zwinności. Bardzo szybko może być przekonfigurowany i przeniesiony do innego procesu. Przy kalkulacji zwrotu z inwestycji należy też pamiętać o transparentności floty robotów, która nie tylko prowadzi do redukcji kosztów całej obsługi logistycznej w magazynie, ale również do oszczędności czasu.
Zawsze wiemy, gdzie jest robot, co robi, ile czasu mu to zajmuje. Cała obsługa jest w pełni transparentna. Robot i jego flota jest permanentnie zintegrowana z systemami produkcyjnymi, w związku z czym one same mają pełny dostęp do informacji, które są im niezbędne, dotyczących aktualnej działalności, problemów, opóźnień. Tym właśnie roboty różnią się od ludzi, bo ludzie takiej „funkcji” pełnej transparentności danych nie mają.
Fot. VersaBox