Dziś w Chinach powstaje 32 proc. aut, a Europa szykuje się do walki z Ameryką Północną o trzecie miejsce (19 vs. 17 proc.) – wynika z danych zamieszczonych w raporcie “The automobile industry. Pocket guide 2023/2024” Europejskiego Stowarzyszenia Producentów Samochodów (ACEA).
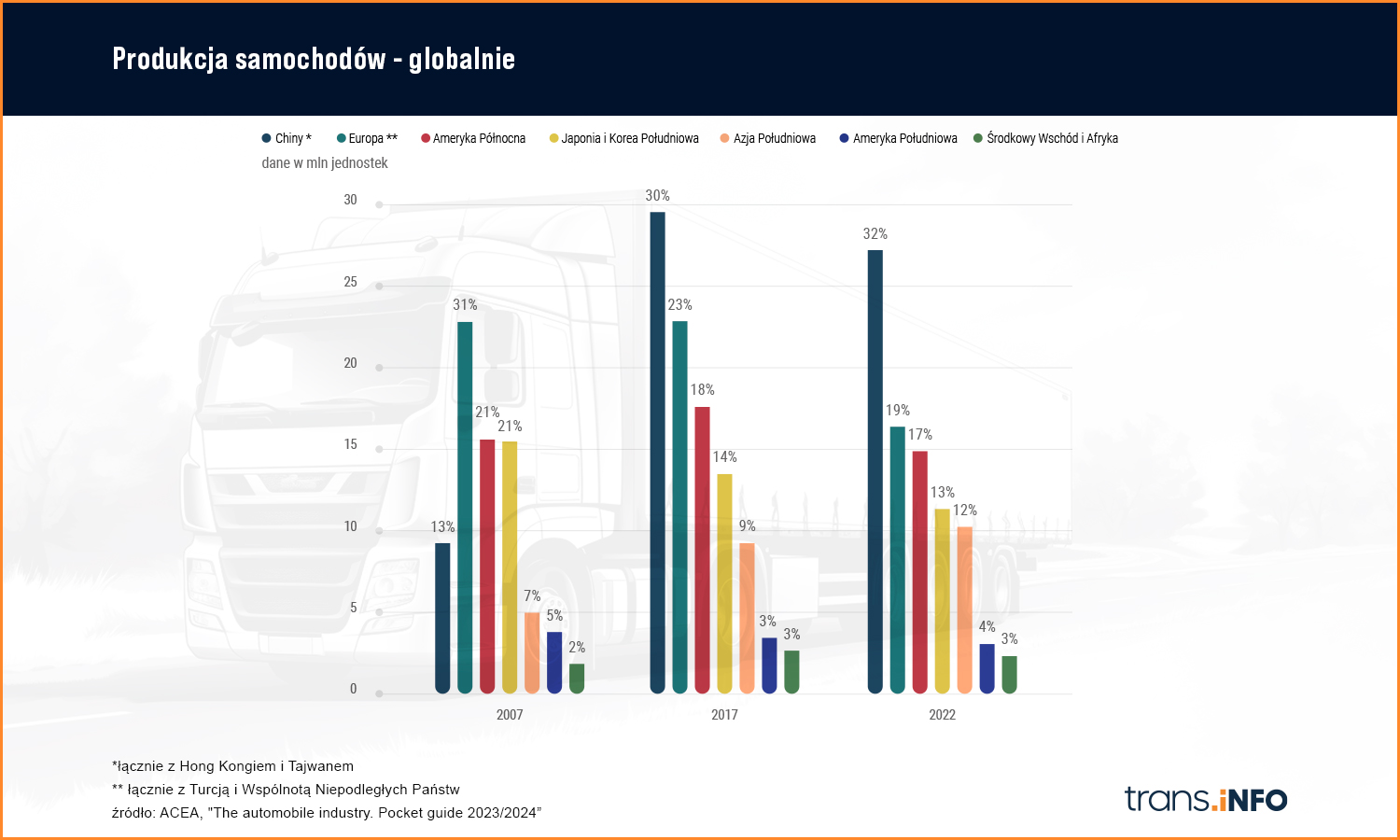
Co więcej, mimo że globalna produkcja samochodów rośnie w najlepsze, w 2022 r. zyskując niemal o 6 proc. względem roku poprzedniego, nie można w tym poczytywać zasług Europy, która jako jedyny region zanotowała w analizowanym okresie spadek – o 0,5 proc. W tym czasie w Chinach produkcja wzrosła o ponad 3 proc., a w Azji Południowej – o ponad 22 proc.
Sama Europa opiera się przede wszystkim na produkcji niemieckiej (ponad 3,7 mln pojazdów w 2022 roku), hiszpańskiej (2,2 mln), francuskiej (1,4 mln) i czeskiej (1,2 mln).
Polska w dziesiątce
W masie 13 mln pojazdów wyprodukowanych w Unii Europejskiej, polska produkcja stanowiła blisko 3,5 proc. Nasz kraj jest jednak jednym z ważniejszych jeśli chodzi o produkcję dostawczaków – w 2022 r. zajął bowiem trzecie miejsce, za wspomnianymi już Francją i Hiszpanią. To również jeden z ważniejszych regionów na europejskiej mapie zakładów montażu oraz fabryk akumulatorów i silników. W 2023 r. mieściło się tu 19 takich zakładów, więcej było tylko w Niemczech (54) i we Włoszech (23) – wynika z danych ACEA.
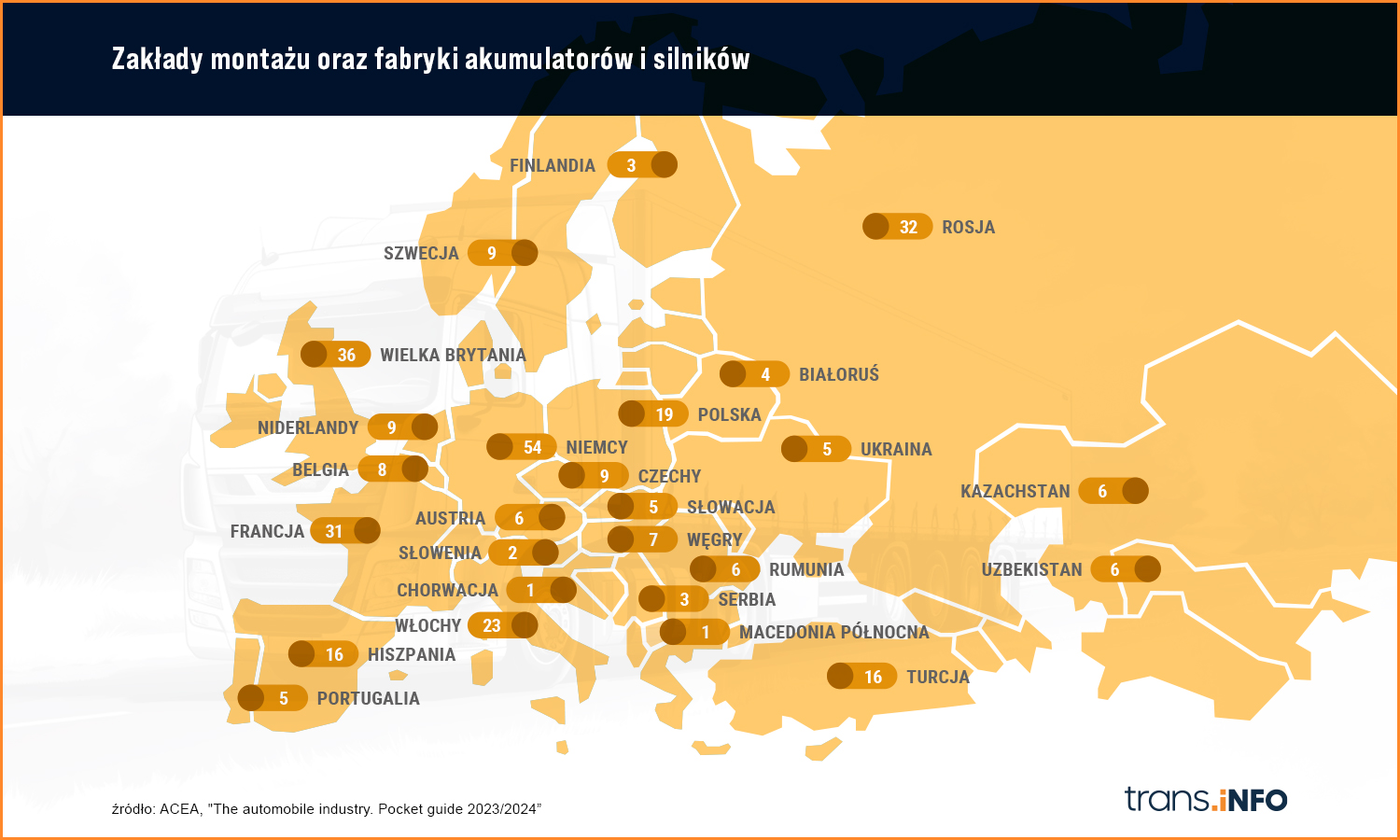
Nic dziwnego, że branża automotive jest bardzo istotna z punktu widzenia polskiej gospodarki. Rośnie produkcja sprzedana – w ciągu pierwszych trzech kwartałów 2023 r. wyniosła 174,6 mln złotych, czyli o 18,7 proc. więcej niż w analogicznym okresie poprzedniego roku – wynika z Raportu kwartalnego KPMG w Polsce i PZPM „Branża motoryzacyjna. Edycja Q4/2023”.
W ostatnich latach poprawiły się szczególnie dane dotyczące produkcji samochodów dostawczych i ciężarowych – w ciągu trzech kwartałów ubiegłego roku wyprodukowano bowiem 221,5 tys. sztuk pojazdów co stanowiło wzrost o 48,5 proc. rok do roku. Rośnie również eksport silników, części samochodowych i akcesoriów.
Motorem napędowym branży są dostawcy części. Polska zajmuje 10. miejsce na liście największych eksporterów podzespołów na świecie z wartością eksportu 12,3 mld dolarów” – podaje Polskie Stowarzyszenie Paliw Alternatywnych w raporcie “Wpływ elektromobilności na rozwój gospodarczy w Polsce”.
W naszym kraju produkuje się gumowe i plastikowe elementy, wodór i baterie litowo-jonowe, co jest szczególnie ważne z punktu widzenia rozwijającego się sektora pojazdów nieemisyjnych. W produkcji wspomnianych baterii jesteśmy liderem, wodoru – zajmujemy piąte miejsce na świecie, ponadto plasujemy się na siódmym w globalnym zestawieniu producentów miedzi – podaje portal trade.gov.pl, równocześnie przypominając, że “miedź jest surowcem wykorzystywanym m.in. do produkcji silników elektrycznych, baterii, falowników, okablowania i stacji ładowania”.
Wszystko to sprawia, że sektor motoryzacyjny jest jednym z ważniejszych dla polskiej gospodarki. W 2021 r. odpowiadał za 8 proc. polskiego PKB, a jego udział w produkcji przemysłowej przekraczał 10 proc. Pracowało a nim 397 tys. osób – szacuje PSPA.
Co dalej z just in time?
Nic więc dziwnego, że Polska, podobnie jak cały świat, uważnie przyglądała się zakłóceniom łańcuchów dostaw, najpierw powodowanym przez lockdown, później przestoje w portach na na produkcji, wojnę na Ukrainie, i kolejne trudności globalne, tj. kryzys żeglugowy związany z atakami na statki w Kanale Sueskim.
Oddziałujące na biznes w ostatnich latach czynniki makroekonomiczne, ale też pandemia COVID-19 czy toczące się konflikty zbrojne, choć negatywnie wpłynęły na gospodarkę, jedynie chwilowo wstrzymały rozwój automotive. Jednocześnie postawiły nowe wyzwania m.in. przed przedsiębiorstwami logistycznymi, które musiały przeanalizować swoje działania w zakresie łańcuchów dostaw i odpowiednio je dostosować. Przykładem był kryzys związany z brakiem półprzewodników, który zakłócił produkcję nowych pojazdów, ale też zrodził potrzebę przeniesienia zakładów odpowiadających za powstawanie tych części bliżej rynków zbytu – zauważa Edwin Osiecki, wiceprezes ds. marketingu i sprzedaży w DHL Express Polska.
Co więcej, w konsekwencji wielu producentów na całym świecie w ubiegłych latach odeszło od standardu dostaw just in time, typowego dla branży automotive.
Mówiło się, że podczas COVID większość firm zmieniła swoje łańcuchy z just-in-time na just-in-case, ale długoterminowo jest to ciężki i drogi model funkcjonowania – potwierdza Andrzej Mowczan, członek zarządu ds. komercyjnych Wielton.
Równocześnie zastrzega, że jego firma nigdy nie była nastawiona “nastawiony na pełne just-in-time”.
Zawsze kierowaliśmy się pewną logiką ekonomiczną, decydując o wielkości dostaw i zapasów. Sytuacja z dostawami dziś jest już na tyle komfortowa, że nie musimy mrozić milionów złotych na magazynach przyprodukcyjnych, ale trzeba przyznać, że pewne komponenty ze starszą datą produkcji jeszcze można u nas znaleźć – dodaje.
Zmodyfikowany system dostaw w stosunku do klientów z branży automotive stosują nadal niektórzy operatorzy logistyczni.
Na wzór przedcovidowego standardu just in time, Seifert Polska wypracowała i proponuje swoim aktualnym i potencjalnym klientom rozwiązanie just in stock, w ramach realizacji polityki safety stock. Chodzi o działania polegające na zapobieganiu i minimalizowaniu ryzyka wystąpienia dłuższych przestojów w formie buforowania i tworzenia w kraju zapasów surowców oraz półproduktów pochodzących głównie z Azji – tłumaczy Szymon Szczepanik, dyrektora logistyki i członek zarządu.
Tym niemniej zauważono również, że niektórzy z producentów “wracają powoli do just in time”. Potwierdza to również przedstawiciel Kuehne + Nagel, którego zdaniem standard ten pozostaje “dominującym modelem dostaw”.
Wiele firm napotyka trudności w poszukiwaniu alternatywnych rozwiązań, ponieważ utrzymanie dużych stocków magazynowych nadal jest niechętnie akceptowane. W przypadku firm automotive fabryki posiadają zapasy komponentów potrzebnych do zasilenia swojej linii produkcyjnej czy linii montażowej na jeden może dwa dni, a w największych fabrykach bufor to zaledwie kilka godzin. Nie ma zaplecza, które gwarantowałoby dostarczenie towarów, komponentów, na linię produkcyjną w razie nieprzewidywalnych okoliczności. To było bardzo dużym wyzwaniem zarówno dla producentów, którzy montują auta, jak i dostawców gotowych komponentów – wskazuje Wojciech Sienicki, dyrektor zarządzający polskim oddziałem firmy.
Żeby to jeszcze lepiej zobrazować, Wojciech Sienicki porównuje konstrukcję rynku branży automotive do piramidy.
Na szczycie są producenci samochodów, którzy mają swoje linie montażowe. Każdy z nich jest zaopatrywany przez dostawców, którzy dostarczają im gotowe moduły. Ci z kolei mają swoich podwykonawców, którzy dostarczają im części do zmontowania modułów, np. do zmontowania kokpitu są potrzebne zarówno elementy plastikowe, jak i elementy tapicerki, czy gotowe wiązki elektryczne. Liczba poddostawców może się zwiększać z każdym niższym piętrem piramidy – tłumaczy.
– Nadal „just-in-time” jest najważniejszym wyznacznikiem zoptymalizowanego łańcucha dostaw – przedsiębiorstwa chcą dostarczać swoje produkty po niskich kosztach i w odpowiednim czasie – kwituje.
Również Kuehne + Nagel dostrzega jednak pewne zmiany, zachodzące pod wpływem zmian w logistyce.
Powoli rośnie znaczenie logistyki „just-in-case”. Większe skupienie się na „just-in-case” wiąże się z dywersyfikacją operacji w łańcuchu dostaw poprzez łączenie i wykorzystywanie różnych rodzajów transportu, tras, portów i miejsc zaopatrzenia. Dzięki proaktywnemu planowaniu z wyprzedzeniem i szerokiej gamie opcji do wyboru, klienci mogą wybrać alternatywne rozwiązanie, które spełni określone potrzeby w sytuacjach awaryjnych – tłumaczy Wojciech Sienicki.
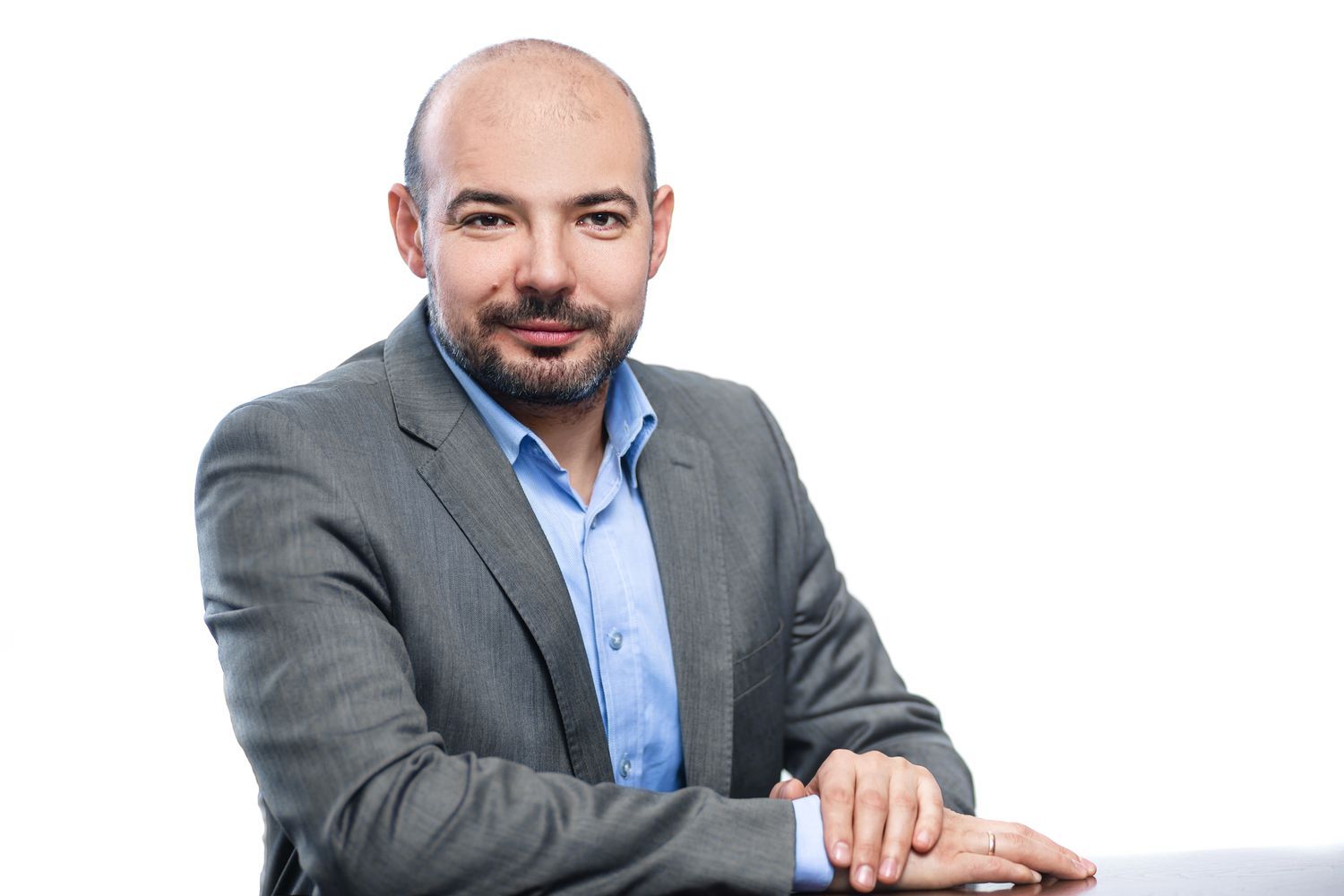
Fot. Wielton
Punkt widzenia producenta: Jak globalne trudności wpłynęły na działalność automotive?
– Producenci w branży pojazdów ciężarowych, naczep i przyczep mają za sobą trudny i niespokojny czas. Sytuacja nie wróciła jeszcze do normy, natomiast zauważalna jest poprawa w dostępności komponentów, a terminy produkcji i wydań pojazdów klientom uległy skróceniu. W dalszym ciągu branża mierzy się ze zmiennym otoczeniem rynkowym, a europejskie i światowe gospodarki zmagają się z wieloma problemami, związanymi z konsekwencjami wojny w Ukrainie, wzrostem cen energii i gazu, galopującą inflacją, czy rosnącymi kosztami finansowania. W efekcie w wielu branżach, także naszej, obserwujemy spowolnienie rynku. Wysoka inflacja i koszty prowadzenia działalności, spadek zapotrzebowania na usługi transportowe, wysokie stopy procentowe przekładają się na mniejszy popyt na naczepy i przyczepy, a także odkładanie decyzji zakupowych – komentuje Andrzej Mowczan, członek zarządu ds. komercyjnych Wielton.
Rzut oka na półprzewodniki
Szczególne wyzwanie stanowiło w ostatnim czasie uzyskanie półprzewodników. Dziś operatorzy logistyczni zapewniają, że ich klienci z OEMs (Original Equipment Manufacturer, czyli producenci oryginalnego wyposażenia) zabezpieczyli swoje fabryki w odpowiednią ilość półprzewodników. Potwierdza to Krzysztof Szeligowski, dyrektor sprzedaży FVL w firmie ADAMPOL. Podobne obserwacje ma Szymon Szczepanik.
Zależność od azjatyckich producentów kontraktowych została obnażona paraliżem przemysłu w 2021 i 2022 roku Europa, jak i Ameryka Północna wyciągnęły wnioski z czasów niedoborów dążąc do większej autonomii w zakresie produkcji półprzewodników. W krok za geopolitycznym dążeniem do przeciwdziałania rosnącym ambicjom Chin w branży, po obu stronach Atlantyku wspierana jest produkcja krajowa. To trend, który zmniejsza narażenie na przyszłe okresy ograniczonej podaży półprzewodników, wynikające z wzrostów i spadków w azjatyckim ekosystemie produkcji elektroniki użytkowej – tłumaczy.
Przypomina przy tym, że w latach 2024-2026 mają w Polsce powstać zakłady produkcji półprzewodników, “które mają pomóc w zabezpieczeniu dostaw w Unii Europejskiej oraz wzmocnić odporność unijnego ekosystemu półprzewodników”. Wartość programu opiewa na 1,5 mld dolarów.
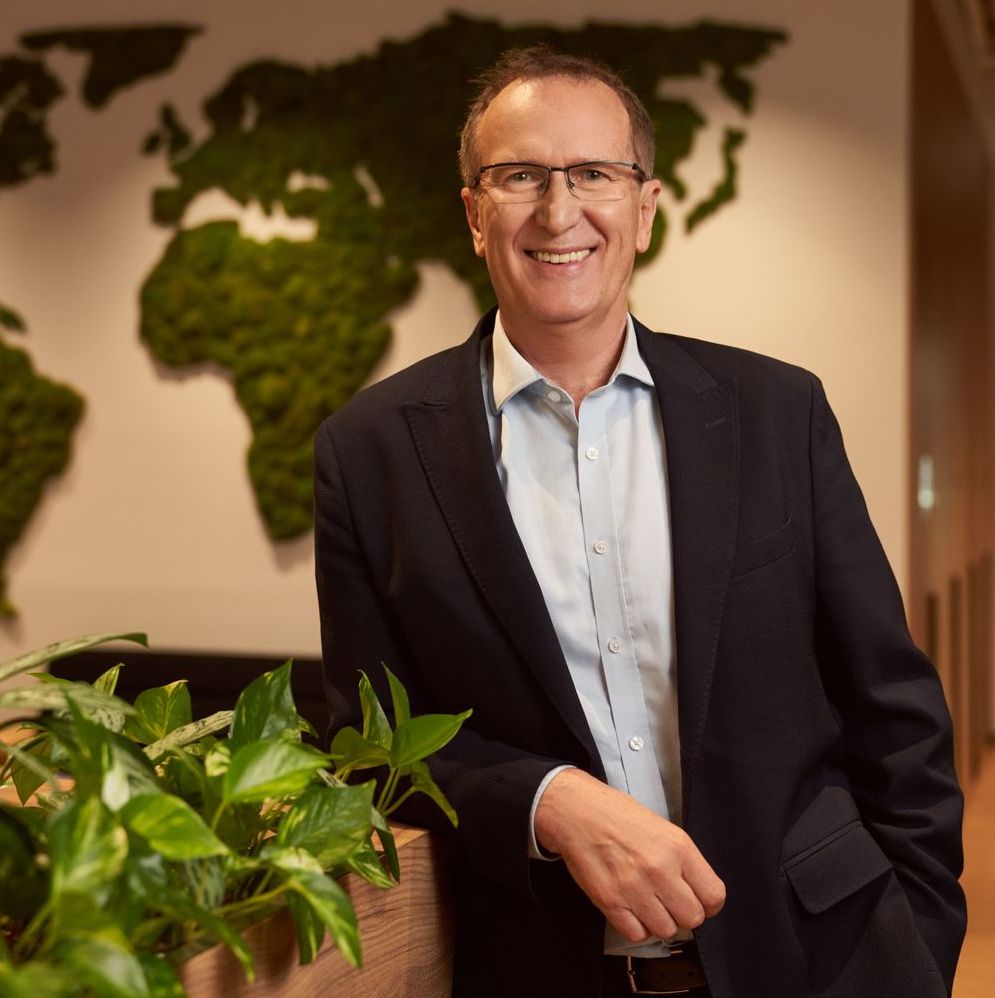
Fot. Kuehne + Nagel
Punkt widzenia operatora: Przenoszenie zakładów produkcyjnych i jego wpływ na logistykę
– Wraz ze wzrostem produkcji chińskich samochodów w Europie, oczekuje się przesunięcia centrów łańcucha dostaw, zdejmując je z Azji i przesuwając bliżej europejskich rynków. To potencjalnie stanowi wyzwanie dla europejskich dostawców pod względem kosztów logistycznych oraz zarządzania łańcuchem dostaw – tłumaczy Wojciech Sienicki, dyrektor zarządzający polskim odziałem Kuehne + Nagel.
Jego zdaniem jednym z istotniejszych rynków dla produkcji komponentów do branży motoryzacyjnej staje się Afryka.
– Największą koncentrację tego sektora obserwujemy głównie w Maroko, Tunezji i Republice Południowej Afryki. W Europie z kolei Węgry zyskują na znaczeniu ze względu na większą stabilność legislacyjną. W tym zestawieniu możemy znaleźć również Polskę, która uważana jest za wschodnie Detroit Europy – dodaje.
Europa, by utrzymać konkurencyjność, musi reagować. – W rezultacie europejskie łańcuchy dostaw dostosowują się do nowej rzeczywistości, a wejście chińskich producentów wprowadza nową dynamikę konkurencji. Chociaż może to prowadzić do podwyższenia cen komponentów. Z kolei chińscy dostawcy stoją przed koniecznością sprostania europejskim standardom, rozszerzając jednocześnie swoje zdolności logistyczne – tłumaczy ekspert.
Branża automotive w przyszłości
Choć zakłócenia w łańcuchach dostaw nadal się pojawiają, operatorzy logistyczni przekonują, że w przypadku obsługi klientów z branży automotive dostrzegalna jest duża odporność wspomnianego łańcucha.
Zauważalne jest, że przedsiębiorstwa z branży automotive odchodzą od reaktywnego zarządzania logistyką, w którym reagują na zakłócenia po ich wystąpieniu. Zamiast tego koncentrują się na zarządzaniu predykcyjnym, wykorzystując dane i analitykę, aby przewidywać zakłócenia i podejmować kroki, aby im zapobiec. Firmy zdają sobie sprawę, że inwestowanie w odporność logistyczną ma kluczowe znaczenie dla długoterminowego sukcesu. Działania te obejmują posiadanie alternatywnych dostawców i rezerwowych zapasów, korzystanie z różnych tras i modelów transportu, a także wykorzystywania technologii w celu zwiększenia widoczności i kontroli nad łańcuchem dostaw – tłumaczy Wojciech Sienicki z Kuehne + Nagel.
– Nadal widoczne jest obniżanie kosztów poprzez minimalizację zapasów i zdolności produkcyjnych, jednak zakłócenia w łańcuchu dostaw ujawniły ryzyko związane z tym podejściem. Pandemia pokazała, że zarządzanie łańcuchem dostaw stało się krytycznym czynnikiem sukcesu we wszystkich branżach, a nie tylko kosztem, który trzeba ponieść – dodaje.
Wyzwań co prawda nie brakuje.
Przesunięcia w łańcuchach dostaw i niesprawdzające się plany powodowały dużą fluktuację wolumenów i co za tym idzie dużą niepewność, brak stabilności i bezpieczeństwa w planowaniu i wykonywaniu usług. Obecnie w FVL (sieć logistyki pojazdów gotowych – przyp.red.) szczególną rolę odgrywają zaburzenia w transportch kolejowych i awaryjne spychanie wolumenów na transport drogowy – wskazuje Krzysztof Szeligowski z firmy ADAMPOL.
Tym niemniej przedstawiciele branży logistycznej są przekonani, że specjalizacja w obsłudze branży automotive, wspierana przez szerokie portfolio usług, zapewniających dywersyfikację przychodów, pomoże im działać w niepewnych czasach.
Przy ponownym wzroście rynku automotive o 18 proc. z 2023 roku, z którym wzrastała ilość naszych ruchów logistycznych – handlingu, jeżeli rozwój rynku będzie taki sam w 2024, osiągniemy ponownie poziom z roku 2019, kiedy pick logistyczny był produkcyjny – szacuje Szymon Szczepanik z Seifert Polska.
Gotowi na szczyt sezonowy?
Tymczasem trwają przygotowania do szczytu sezonowego, bo pierwszy tuż przed nami. Przypomnijmy, że w branży automotive szczyty przypadają w marcu, czerwcu, wrześniu i grudniu (dla niektórych graczy – również w lipcu).
Wiąże się to z wymuszaniem wypełnienia celów sprzedażowo-dystrybucyjnych (kwartalnych, półrocznych i rocznych) przez OEMs. W marcu jest też koniec roku fiskalnego w Japonii i duża presja ze strony japońskich producentów na wypełnienie planów – przypomina Krzysztof Szeligowski.
Punkt widzenia producenta: Szczyty sezonowe
Różne produkty z naszego portfolio mają swoje „sezony”, np. wywrotka stalowa dla branży budowlanej zazwyczaj jest potrzebna od razu po zimie, wywrotka pod produkty rolne – od kwietnia do września, furgony mają swój pik często przed Świętami, a kurtyna jest sprzedawana przez cały rok. Naturalne spadki zauważalne są w okresie wakacyjnym, głównie w sierpniu z uwagi na coroczny postój produkcyjny w spółkach oraz sezon urlopowy. W okresie jesienno – zimowym często mamy do czynienia z zamówieniami z dłuższym wyprzedzeniem, ponieważ firmy zaczynają przygotowanie do realizacji świeżo zatwierdzonych budżetów – tłumaczy Andrzej Mowczan, członek zarządu ds. komercyjnych Wielton.