Już kilka lat temu niemiecki potentat w branży napojowej, Gerolsteiner postanowił wdrożyć jedno z najnowocześniejszych rozwiązań logistycznych. W pełni zautomatyzowany, kompaktowy magazyn z głębokim korytarzem miał zdecydowanie usprawnić składowanie, ale też przygotowanie towarów do ekspedycji.
Regały mobilne, kanałowe i standardowe systemy magazynowania, systemy wahadłowe – z takich rozwiązań korzysta zazwyczaj branża napojowa. Z punktu widzenia wydajności, liczą się głównie rozwiązania automatyczne. Pewne czynności wykonywane są za pomocą robotów, stosuje się zautomatyzowany system kompletacji, a firmy korzystają z automatycznego paletyzowania i depaletyzowania.
Część z tego rodzaju rozwiązań wykorzystano w zautomatyzowanym obiekcie Gerolsteiner. Bazę systemu składowania stanowi Schäfer Lift&Run – System. To rozwiązanie do obsługi palet w magazynach kanałowych. Jest używane zwykle do wprowadzania do magazynu i wydawania z niego palet, obsługując systemy regałowe o wysokości do 8 m (może obsługiwać od 2 do 4 poziomów regałów na oś). Dwumasztowy Lift&Run przenosi palety poprzecznie na swoim wózku podnoszącym. Wraz z windami tworzy kompletny system, który pozwala znacznie zwiększyć przepustowość.
Wśród kluczowych korzyści użytkownicy wymieniają: wysoką dynamikę, zajmowanie małej ilości miejsca, a także energooszczędność. System zwiększa też dostępność produktu, wydajność dostaw i jakość usług, wyższą przepustowość.
Magazyn kanałowy – tam rządzą WAMAS i Orbiter
Ważnym elementem systemu stosowanego w Gerolsteiner są: Orbiter oraz inteligentny system zarządzania, WAMAS. Generalnie rzecz biorąc, wózek Orbiter odpowiada za odstawianie palet w kanale na miejsca magazynowe i pobieranie ich stamtąd.
W przeciwieństwie do typowych układnic, ten system przemieszcza się po dwóch szynach, w związku z czym nie potrzebuje górnej szyny prowadzącej. Zastosowanie kilku urządzeń jedno nad drugim pozwala obsługiwać bardzo wysokie regały (do 45 m). Palety są wtedy doprowadzane do kanałów i podejmowane z nich z użyciem wind.
Orbiter zapewnia automatyczną obsługę palet w magazynach kanałowych. Kanałowy wózek transportowy (nazywany również wózkiem wahadłowym) współpracuje ze stacją dokowania.
Na regałach kanałowych, w których używany jest system wahadłowy, od przodu montowane są konsole centrujące przyspieszające i upraszczające obsługę.
Konsola centrująca zapobiega uszkodzeniom
Eksploatacja systemu rozpoczyna się od ustawienia w konsoli centrującej zestawu stacji dokującej wraz z wózkiem wahadłowym. Konsola centrująca gwarantuje prawidłowe ustawienie zestawu Orbiter, a później kolejnych ładowanych do kanału palet, zapobiegając uszkodzeniom materiału i zapewniając oszczędność czasu podczas podawania ładunku. Ta zaleta szczególnie ujawnia się w przypadku wyższych poziomów regałów, daje maksymalne poczucie pewności i bezpieczeństwa operatorom. Wstawioną do kanału na stanowisko stacji dokującej paletę przejmuje wózek Orbiter, który przewozi ją w najbliższe wolne miejsce magazynowe w kanale.
Obsługa palet w systemie kanałowym jest możliwa w schematach FILO i FIFO. W przypadku modelu FILO (First in-Last Out – pierwsze weszło, ostatnie wyszło) palety są wprowadzane do magazynu i pobierane z niego tylko z jednej strony. W przypadku modelu FIFO (First In-First Out – pierwsze weszło, pierwsze wyszło) palety wprowadzane do magazynu z jednej strony są pobierane z niego po przeciwnej stronie.
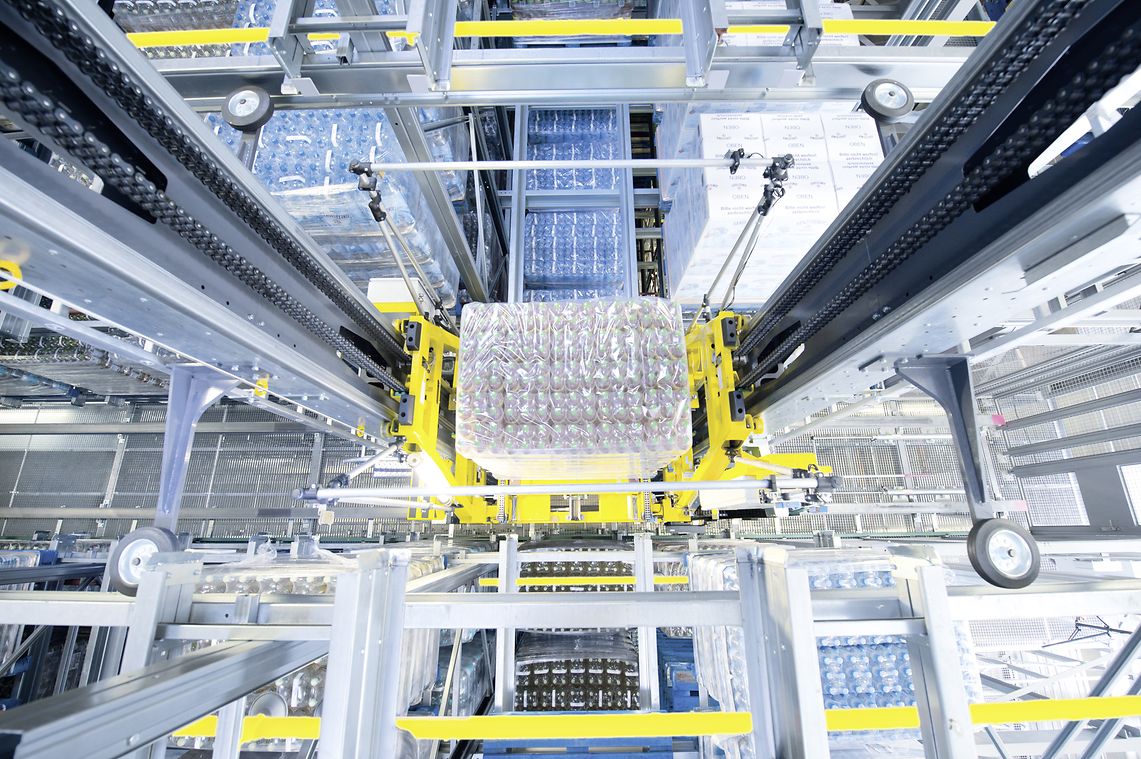
Fot. Schäfer
Kiedy wózek Orbiter przenosi paletę na miejsce magazynowe, wózek widłowy może jechać już po kolejną paletę, która ma być, jako następna wprowadzona do kanału. To oznacza oszczędność czasu. System pozwala obsługiwać ponad 100 różnych typów palet.
System wahadłowy zasilany jest z użyciem opatentowanych modułów Power Caps (napęd zasilany za pomocą kondensatorów) lub akumulatorów. Polecenia przejazdu wysyłane są do wózka bezprzewodowo za pomocą pilota. Po zakończeniu zadania, wózek wahadłowy automatycznie wraca do stacji dokującej.
Procesami realizowanymi przez system Lift&Run steruje oprogramowanie logistyczne WAMAS. Obejmuje wprowadzanie towarów do magazynu i pobieranie ich stamtąd, kontrolowanie załadunku oraz zarządzanie stanami i miejscami magazynowymi. Zarządza też przepływami materiałów i wewnątrzzakładowym transportem.
Magazyn ma sześć naw i ok. 19 tys. miejsc składowania.
Fot. Schäfer