Mydibel to producent żywności. Wiele jego wyrobów wymaga głębokiego zamrażania. Po to, by zapewnić im optymalne warunki składowania, firma zdecydowała się wdrożyć zautomatyzowany system wykorzystujący maszyny Orbiter. Kanałowe rozwiązanie (mrożenie do -24 st. C) zastosowane w belgijskim Mouscron dostarczył SSI Schaefer.
Firma Mydibel, założona trzydzieści lat temu dostarcza dziennie ok. 2 tys. ton mrożonych produktów ziemniaczanych dla przemysłu spożywczego, sieci handlowych i firm cateringowych w ponad stu krajach. Specyficzne cechy organoleptyczne i fizyczne produktów, jak również duże zróżnicowanie asortymentowe nakładają na logistyków przedsiębiorstwa spore wymagania. Zdecydowano się na maszyny do przechowywania i wyszukiwania z pojemnikami Orbiter i tzw. inteligentną koncepcją przepływu materiału. To ona ma zagwarantować zachowanie należytej przejrzystości asortymentu, odpowiednią wydajność i niezbędną wygodę obsługi. Całość kontrolowana jest przez system zarządzania magazynem WAMAS.
Wcześniej, w pięciu obiektach składowania należących do Mydibel procesy logistyczne odbywały się ręcznie. By to zmienić postanowiono skoncentrować wszystkie pojemności magazynowe w jednym nowym, nowoczesnym obiekcie, w siedzibie głównej, w Mouscron.
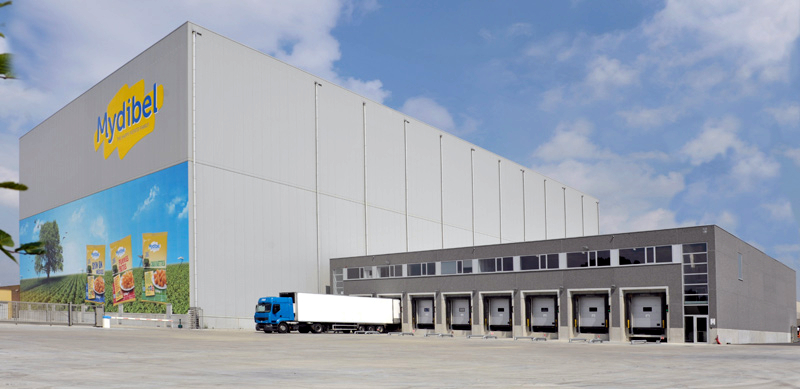
Fot. Mydibel
Skoncentrowanie przechowywania w jednym punkcie należało do kluczowych zadań projektu. Uznano bowiem, że taka koncentracja ułatwi utrzymanie łańcucha głębokiego mrożenia przez zaniechanie transportu między magazynami (rozproszenie powodowało ryzyko zerwania tego łańcucha).
Skutkiem tego miało być też m.in. bardziej efektywne wykorzystanie kilkuset osobowego personelu. Aby to osiągnąć należało zautomatyzować czynności, zoptymalizować składowanie i procesy dystrybucji.
System prowadzi palety do ciężarówek
Zastosowane rozwiązanie to system z tzw. przewozami wahadłowymi.
Trzon stanowi pięć 93-metrowych korytarzy wysokiego składowania. Palety składowane są na jedenastu poziomach. Zdecydowana większość kanałów dostępna jest po każdej stronie przejścia, a dostęp umożliwia pięć urządzeń magazynujących i pobierających (SRM). Kanały mogą być “obsługiwane” z dwóch stron różnymi towarami, np. zgodnie z zasadą FIFO (First-In, First-Out, pierwsze weszło, pierwsze wyszło), co w praktyce oznacza, że przechowywanie odbywa się po jednej stronie kanału, a pobieranie po drugiej.
Po przyjęciu palet, SRM przesuwają je do docelowego kanału. Automatyczna stacja lokacyjna umieszcza następnie palety systemowe pod towarami. System transportowy prowadzi palety do stanowisk magazynowych wysokiego składowania (HBW).
Centralny system przenoszenia palet obsługuje dwie sekcje transportowe, które znajdują się jedna na drugiej.Przechowywanie odbywa się na najniższym poziomie, a pobieranie odbywa się za pośrednictwem najwyższego poziomu.
Palety z towarami są prowadzone na jednej sekcji transportowej. Przy pojemności prawie 100 palet, linie tworzą bufor do sekwencjonowania (przed załadunkiem palet na ciężarówki).
Orbiter wyeliminował pracę ręczną w magazynie
Proces adaptacji tego rodzaju rozwiązań w magazynie trwał kilkanaście miesięcy. Rozpoczął się od wykonania symulacji i planu, później stworzono projekt funkcjonalny i architektoniczny, jak również koncepcję ochrony przeciwpożarowej (bez tryskaczy). Magazyn zaopatrzono następnie w odpowiednie urządzenia (m.in. maszyny do przechowywania i pobierania z wahadłowcami Orbiter), jak również w system sterowania do zarządzania magazynem i przepływu materiału oraz układ transportujący palety.
W rezultacie zmian, łącząc pojemności magazynów uzyskano łatwo sterowalny obiekt, likwidując przy tym np. potrzebę stosowania specjalnych, przystosowanych do pracy w niskich temperaturach wózków widłowych. Praca ręczna osób w samym magazynie została praktycznie wyeliminowana, odpowiadają oni jedynie za programowanie, sterowanie i nadzorowanie poszczególnych czynności.
Fot. SSI Schaefer