Bühler to firma produkująca urządzenia i maszyny stosowane m.in. w przemyśle zbożowym i nasienniczym, browarach i fabrykach słodu, w branży budowlanej i chemicznej, w zakładach produkujących paszę treściwą, przy składowaniu nawozów i w przetwarzaniu biomasy oraz recyklingu. Odpowiednie zorganizowanie logistyki, na stosunkowo niewielkiej powierzchni i przy dość skomplikowanych maszynach obróbczych jest kwestią kluczową. Dlatego układnica regałowa stanowi najważniejsze urządzenie w magazynie.
Przymierzając się do inwestycji w zautomatyzowany system produkcyjno-logistyczny chodziło przede wszystkim o minimalizowanie strat i zwiększenie efektywności. W istocie, w przypadku takiej działalności, efekty przynieść może głównie skrócenie czasu realizacji poszczególnych procesów, optymalizacja kosztów zatrudnienia.
– W dziale produkcji używaliśmy do obróbki blach płaskich sześciu maszyn. Jednak w nowym magazynie blach miało znaleźć się miejsce dla dziesięciu maszyn, abyśmy w razie potrzeby mogli się elastycznie rozwijać. Oprócz tego nowy obiekt miał zostać wzniesiony na bardzo małej powierzchni magazynowej – tłumaczy Klaus Harrer, szef produkcji zakładu w Beilngries.
Proces wdrożenia całkowicie nowego zautomatyzowanego magazynu blach Remmert przeprowadzono wyjątkowo krótko, wszystko trwało ok. osiem miesięcy.
Układnica regałowa sercem magazynu
Jak to działa? Nowo powstały magazyn ma rozmiary: 51,5 x 8 x 6 m (dł. x szer. x wys.). Mieści 250 palet, każda dysponuje obciążeniem użytkowym na poziomie 5 t. Składowane blachy mogą mieć maksymalnie rozmiar 2 x 4 m. Serce stanowi układnica regałowa o prędkości przesuwania 100 m/min. Magazyn składa się z dwóch rzędów regałów ustawionych naprzeciw siebie – jednego z jedenastoma wieżami i drugiego składającego się z zaledwie trzech modułów. Zgodnie z założeniem inwestycji z perspektywą rozbudowy – jest on przygotowany do ewentualnego poszerzenia w przyszłości.
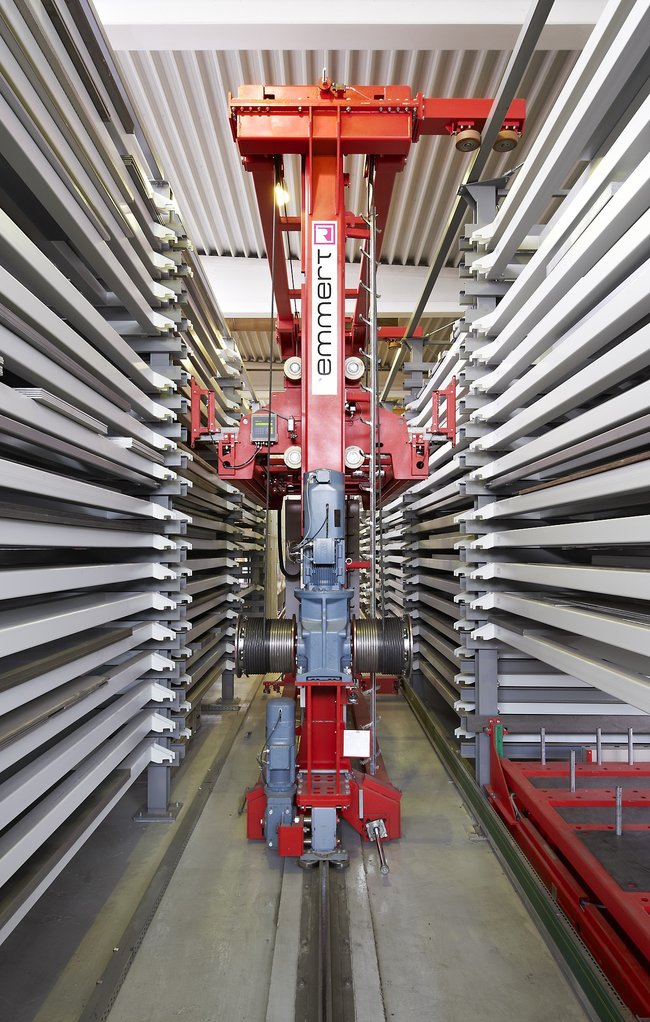
Fot. Remmert
Między regałami porusza się układnica o dużej wydajności, co umożliwia szybki załadunek i rozładunek materiałów.
Przygotowano jedną stację załadowczą i pięć rozładowczych. Wokół nowej instalacji zgrupowano pięć maszyn do obróbki: trzy lasery Bystronic Bystar 4020, maszynę do cięcia strumieniem wody Bystronic Byjet 2030 i dwie sztance Trumpf. Połączono je z automatem magazynowym mechanicznie, za pomocą przyssawek próżniowych. Wszystkie blachy wychodzące z magazynu są obrabiane zgodnie z zasadą “pull”.
– Przy zastosowaniu zasady “pull” konieczna jest szczególnie duża dyspozycyjność układu. W końcu materiały pobierane są tylko wtedy, gdy mogą zostać bezpośrednio przetworzone. Nie stosuje się buforowania. Nowy magazyn i zwiększona do ponad 99 proc. dyspozycyjność układu zaspokajają nasze potrzeby – stwierdza Klaus Harrer.
Program steruje ruchem w magazynie
Szybkimi procesami załadowania i rozładowania steruje i zarządza oprogramowanie PRO WMS Enterprise.
Zgodnie ze strategią przypisuje ono każdemu ładunkowi miejsce składowania w obrębie systemu i optymalizuje w ten sposób czas potrzebny na ruchy materiału. Dzięki programowi magazynowemu można też w każdej chwili dokonać kontroli stanów magazynowych, ponieważ wszystkie wchodzące i wychodzące palety są automatycznie ważone.
Jak wyjaśnia Klaus Harrer dzięki inwestycji udało się wydłużyć czas pracy laserowych maszyn tnących z niecałych 17 do średnio 20 godzin dziennie. Mowa tu o rzeczywistej pracy laserów, bez czasu niezbędnego do ładowania i programowania maszyn.
Fot. Pixabay/jarmoluk