Ograniczenie przestojów maszyn ma kluczowe znaczenie dla wydajności produkcji. W Wieltonie, a zatem u producenta naczep, gdzie różnego rodzaju materiałów, w tym blach, przetwarza się bardzo dużo – sprawa nabiera szczególnego znaczenia. Problem pomogła rozwiązać m.in. układnica regałowa i magazyn automatyczny.
Wielton ma wielu dostawców. Są to producenci osi i zawieszeń, opon i felg, układów hamulcowych, hydrauliki siłowej, sklejki podłogowej oraz farb i lakierów. Szczególnie ważne są blachy stalowe i aluminiowe, ponieważ to one stanowią jeden z głównych elementów każdej naczepy, zwłaszcza wywrotek. Na liście dostawców są producenci i dystrybutorzy blach i kształtowników stalowych tacy jak SSAB EMEA, ThyssenKrupp Energostal, ArcelorMittal, VoestAlpine Krems, Stalprodukt Centrostal, a także producenci kształtowników, blach aluminiowych: Grupa Kęty, Sapa Aluminium, Alcoa EMEA. Miesięcznie fabryka przerabia ponad tysiąc ton blach. Zapanowanie nad tymi ciężkimi i często mało “poręcznymi” elementami stanowi spore wyzwanie.
Jeszcze kilka lat temu blachy po przywiezieniu na teren zakładu były składowane na regałach znajdujących się w kilku halach, oddalonych od maszyn obróbczych. Proces zaopatrywania maszyn w materiał był z tego powodu czasochłonny i trudny do kontroli.
Blachy trzeba było przewozić, co skutkowało dużymi nakładami na logistykę wewnętrzną. Trudno było też zapewnić w każdym przypadku ciągłość produkcji, a to wiąże się z odpowiednim wykorzystaniem, działających w fabryce wycinarek laserowych.
Automatyczny magazyn zajmuje mniej miejsca
Zdecydowano się na zmiany, zbudowano magazyn, w którym można składować zarówno blachy w formacie 1,5 x 3 m, jak i 6 x 2 m.
Magazyn jest automatyczny, a instalację zintegrowano z czterema laserami. Pobór niezbędnego do produkcji surowca następuje samoistnie, wtedy gdy jest on potrzebny, aby zapewnić ciągłość pracy wycinarkom. Dzięki temu przestojów w pracy praktycznie nie ma.
Zdecydowano się na automatyczny magazyn blach nie tylko dlatego, by uniknąć przestojów. Chodziło też o zwiększenie pojemności magazynowej, a tym samym wygospodarowanie większej przestrzeni na produkcję.
Magazyn automatyczny zajmuje relatywnie niedużo miejsca, jego wymiary to 72,5 x 7,7 x 7,5 m (dł. x szer. x wys.). Wewnątrz jest 356 miejsc składowania o wymiarach 3 x 1,5 m, a także 90 miejsc składowania o wymiarach 6 x 2 m. W obu przypadkach obciążenie użytkowe każdego z miejsc paletowych wynosi 5 t. W sumie, na powierzchni ok. 560 m kw. można składować blachy o łącznej wadze ok. 1,6 tys. t.
Obsługa odbywa się z wykorzystaniem centralnej stacji załadowczej, czterech stacji wyładowczych zaopatrujących bezpośrednio wycinarki laserowe w surowe blachy, jak również stacji wyładowczej dostarczającej materiał do trzech pozostałych maszyn. Cztery wycinarki laserowe Bystronic połączono bezpośrednio z systemem magazynowym, które poprzez ByLoadery w zautomatyzowany sposób zaopatrywane są w surowe blachy. Dwie inne wycinarki laserowe Bystronic i Trumpf oraz wycinarka plazmowa zaopatrywane są przez oddzielną stację oraz urządzenie dźwigowe z przyssawkami.
Całością “opiekuje się” oprogramowanie PRO WMS Enterprise (łącznie z interfejsem SAP). Praktycznie wyeliminowano potrzebę stosowania środków transportu wewnętrznego.
Pozyskanie dodatkowej przestrzeni to tylko jedna z korzyści.
Układnica regałowa zwiększyła efektywność pracy wycinarek
Dzięki zautomatyzowanemu procesowi zaopatrywanie maszyn w materiał odbywa się znacznie szybciej i bezpieczniej. Układnica regałowa o wysokiej wydajności umożliwia wykonanie ok. 20 cykli podwójnych na minutę.
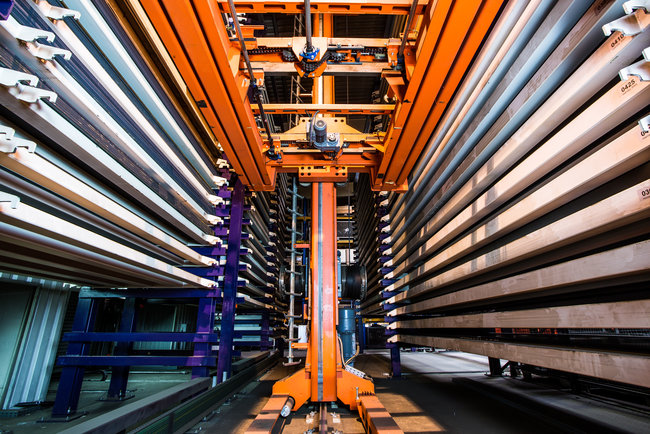
Fot. Remmert
– Dawniej blachy transportowano z miejsc składowania do maszyn obróbczych za pomocą wózka widłowego, teraz wystarczy przycisnąć odpowiedni guzik, by surowce w ciągu kilku minut zostały dostarczone przez zintegrowaną układnicę regałową do wyznaczonej stacji magazynowej. Czas dostępu został znacznie skrócony. Dzięki temu rozwiązaniu zyskaliśmy wystarczającą ilość miejsca, by móc rozbudować dział produkcji i powiększyć liczbę wycinarek laserowych z dwóch do sześciu, zwiększając jednocześnie efektywność pracy maszyn, gdyż nie muszą one już czekać na materiał – mówi Tomasz Swędrak, dyrektor techniczny Wieltonu.
Potwierdza jednocześnie, że kluczowa dla użytkownika była elastyczność i wydajność systemu, dostosowanie do pracy z dwoma formatami blach, ale też możliwość przyłączenia w przyszłości wycinarki laserowej dowolnego producenta.
Obecnie cztery wycinarki laserowe są zaopatrywane bezpośrednio przez zautomatyzowany magazyn blach, natomiast pozostałe dwie wycinarki laserowe oraz wycinarka plazmowa są obsługiwane przez odrębną stację.
– W ten sposób nie zakłócamy podłączonych bezpośrednio procesów produkcyjnych i wszystkie siedem maszyn w trybie ciągłym otrzymuje potrzebne surowce – wyjaśnia Paweł Zieliński, general manager Eastern Europe z Remmert.
Fot. Wielton