Nazwa Alnatura zobowiązuje. Niemiecka firma, jeden z ważnych graczy na tamtejszym rynku tzw. zdrowej żywności gruntownie zmodernizował swoje centrum magazynowo-dystrybucyjne stawiając na… drewno. To z niego zbudowano praktycznie cały obiekt. Wewnątrz zastosowano natomiast nowoczesny system automatyczny CycloneCarrier. Centrum dystrybucyjne z magazynem wysokiego składowania Alnatury znajduje się w Lorsch.
Potężna hala ma wysokość 17,5 m. Umieszczono w niej CycloneCarrier, czyli zautomatyzowany system magazynowo-transportowy, przeznaczony głównie do obsługi małych ładunków. Wahadłowe rozwiązanie zaprojektowano z myślą o aplikacjach, w których niezbędna jest wysoka przepustowość i duża dostępność, np. w handlu detalicznym i handlu elektronicznym. Automatyzacja ma zapewniać wydajny i bardzo dynamiczny przepływ towarów od przyjęcia do magazynu, poprzez wydanie, kompletację, aż do przygotowanie wysyłki dla sklepu.
W CycloneCarrier można składować pojemniki, tace lub kartony na podwójną albo poczwórną głębokość. Jeden system magazynowy może obsługiwać korytarze o nawet 150-metrowej długości (ten konkretny w Lorsch ma 118 m). Pojazdy są dostępne w dwóch wersjach, z urządzeniami do przeładunku o stałej lub regulowanej szerokości (do obsługi różnych rozmiarów produktów). Opcjonalnie można zastosować windę z dwoma pokładami, co jeszcze zwiększa przepustowość.
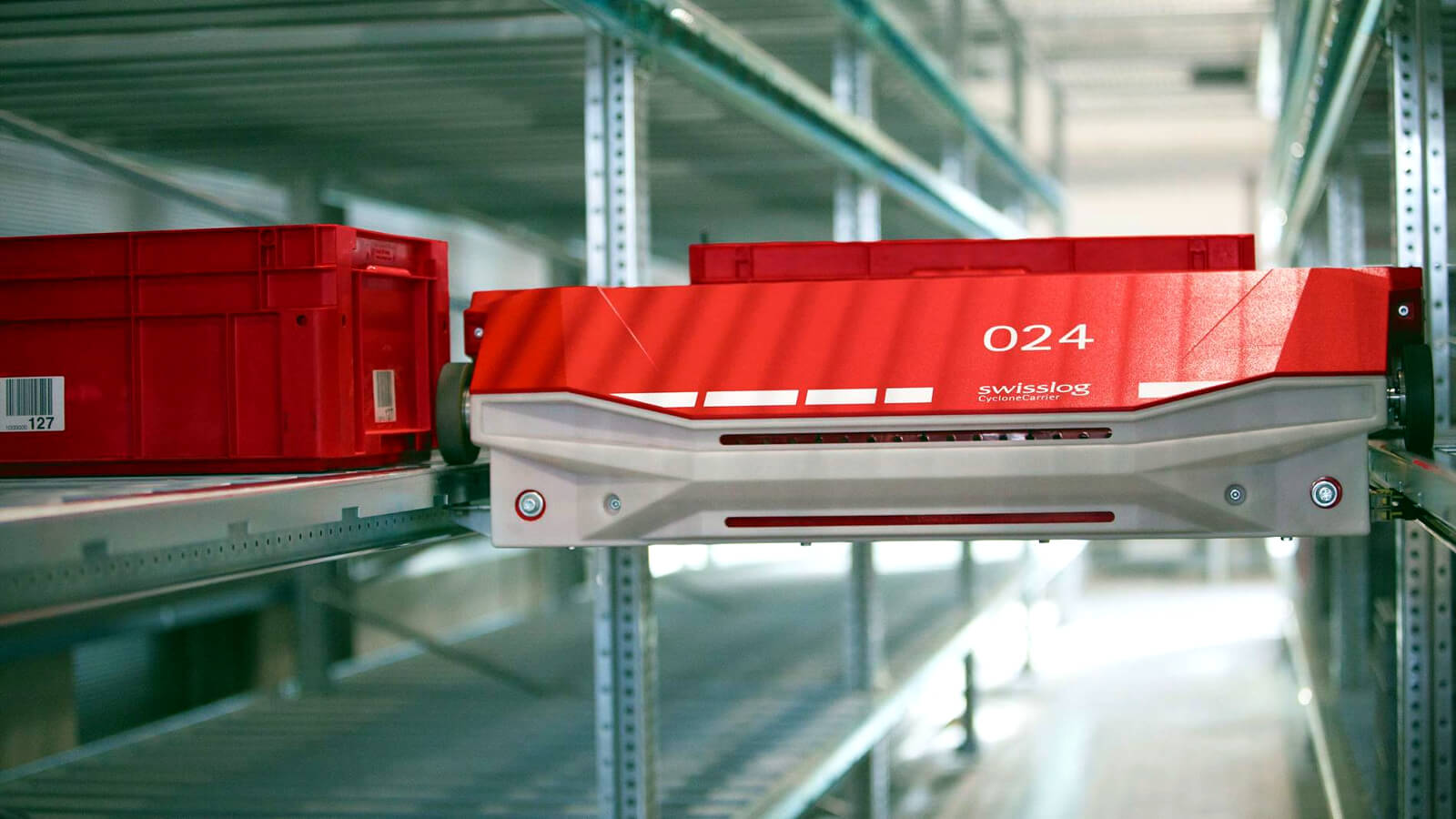
CycloneCarrier w Lorsch obsługują 32 wózki (shuttle). Do dyspozycji jest ponad 30 tys. miejsc. Wózki poruszają się z maksymalną prędkością 4m/s. Zarówno wprowadzają towar do magazynu, jak i go z niego wyprowadzają. Do dyspozycji jest w sumie sześć stacji, w których prowadzone są czynności związane z paletyzacją/depaletyzacją, pickingiem i kompletacją. Oprócz wózków, w systemie zastosowano zatem również np. przenośniki paletowe oraz roboty kompletujące.
Więcej i szybciej dzięki automatyzacji
Automatyzacja centrum dystrybucyjnego okazała się niezbędna m.in. po to, aby można było w nim realizować ponad 1 tys. pozycji (zleceń) w ciągu godziny. To konieczne aby zapewnić sprawną realizację zamówień wynikających z aktualnego popytu na produkty Alnatury, a jednocześnie aby zagwarantować możliwość łatwej rozbudowy systemu w późniejszym okresie, gdy zaistnieje taka potrzeba.
Przyjazne dla środowiska rozwiązanie ma przede wszystkim skracać trasy transportu i pozwolić sprawnie zarządzać znacznie większą niż dotąd liczbą jednostek asortymentowych, kompletować i przygotowywać do wysyłki. Nadaje się do obsługi zwrotów, uzupełniania lub buforowania (w celu konsolidacji zamówień). Dzięki dynamicznemu systemowi wahadłowego magazynowania Alnatura może dostarczać do sieci sklepów swe produkty z jednego centralnego miejsca.
Twórcami rozwiązania są konstruktorzy Swisslog. Funkcjonowanie CycloneCarrier automatycznie kontroluje układ zarządzający SynQ. Jest modułowy, inteligentny i potrafi działać predykcyjnie. Ma funkcje monitorowania, a jedną z nich jest wizualizacja 3D. Pozwala ona uprawnionym pracownikom obserwować w czasie rzeczywistym pracę całego magazynu i jego poszczególnych elementów i wykryć ewentualne błędy znacznie wcześniej, niż one w rzeczywistości mogą nastąpić.
Matthias Lindner, szef departament logistyki, Alnatura podkreśla, że CycloneCarrier dysponuje zaawansowanym urządzeniem do obsługi ładunku (sprawdzanie odległości pomiędzy kartonami, a ramiona teleskopowe mogą być regulowane niezależnie, jeśli to konieczne, by bezpiecznie podnosić kartony, które są uszkodzone lub przesunęły się z właściwej pozycji). Standardowy moduł oprogramowania zapewnia dostęp do narzędzi biznesowych optymalizujących wydajność “wahadłowca”.
Drewno dobrze izoluje
Cały, olbrzymi obiekt magazynu Alnatury wykonano z drewna. Wykorzystano 5 tys. metrów sześc. drewna świerkowego i modrzewiowego z Niemiec, Austrii i Czech. W silosowym budynku jest w sumie ponad 65 kilometrów różnego rodzaju wsporników, a także łączników. Fasadę również zbudowano z certyfikowanego drewna modrzewiowego. Użytkownik podkreśla, że dzięki dobrej izolacji i naturalnemu chłodzeniu nie jest wymagane ogrzewanie, ani sztuczne chłodzenie (co obniża emisję CO2 obiektu).
Fot. Alnatura
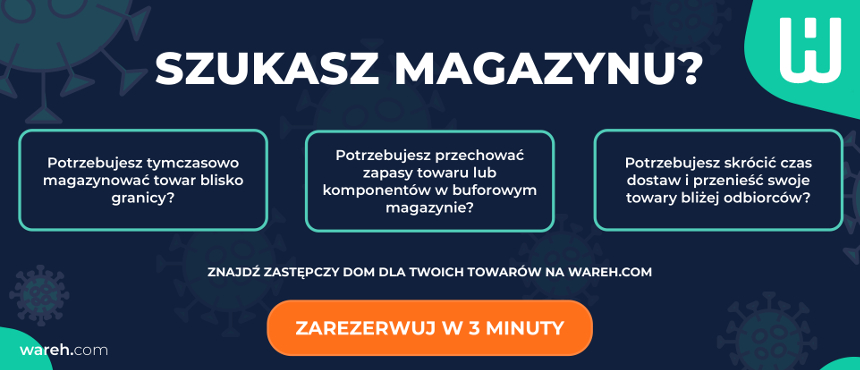