Wyroby mięsne i wędliniarskie wymagają szczególnych warunków przechowywania i dystrybucji. W jednej z największych w Polsce firm z branży mięsnej zdecydowano się na magazyn pojemnikowy automatyczny oraz paletowy. Ma ułatwić składowanie, ale też usprawnić przygotowywanie zamówień.
Decyzja o automatyzacji centrum logistycznego ZM Henryk Kania zapadła, gdy okazało się, że dotychczasowe jest za małe, a efektywność i płynność przygotowywania zamówień pozostawia wiele do życzenia. Stwierdzono, że budowa nowego centrum logistycznego i zaopatrzenie go w automatyczny system magazynowy może zaspokoić nie tylko obecne, ale też przyszłe potrzeby firmy w obszarze logistyki.
Z racji specyfiki składowanych towarów, postanowiono stworzyć paletowe i pojemnikowe magazyny automatyczne wraz z urządzeniami, które pozwalają na sprawną komunikację pomiędzy częścią produkcyjną a obszarem ręcznej kompletacji zamówień, a także informatycznym systemem zarządzania magazynem Easy WMS. System ten kontroluje wszystkie procesy zachodzące w instalacji (od momentu wejścia produktów do magazynu, do ich wysyłki do klienta).
Kontrola przez system Easy MWS
Koniec ciągu produkcyjnego stanowią linie pakujące. Właśnie tam kontrolę nad towarem przejmują automaty.
Stanowiska pakujące skomunikowano z resztą magazynu za pomocą podwójnej linii przenośników automatycznych: jedna z nich odstawia puste pojemniki do strefy pakowania, a druga przenosi pełne w kierunku magazynu. Napełnianie pojemników odbywa się na końcu każdej linii lub bezpośrednio na przenośniku nienapędzanym (grawitacyjnym), który może również pełnić rolę stołu przygotowawczego. Równolegle do niego porusza się przenośnik do transportu ciągłego, który przewozi pojemniki już zapełnione.
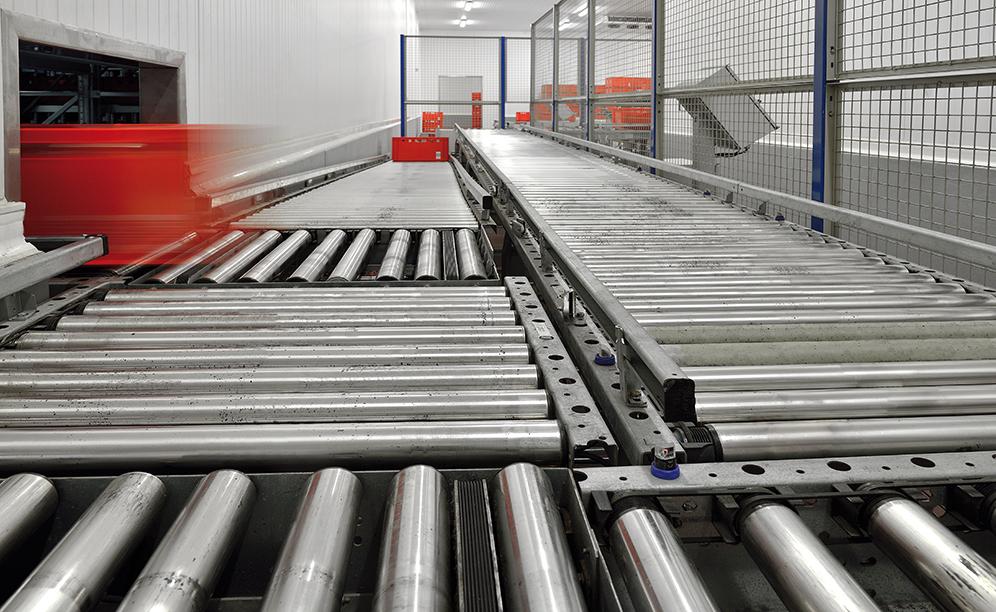
Fot. Mecalux
Procesy przebiegające w strefie łączącej linie pakujące z przenośnikami są kontrolowane przez oprogramowanie Easy WMS. Jego zadaniem jest zapamiętywanie danych o wszystkich produktach umieszczanych w pojemnikach i przechowywanie tych danych aż do momentu wydania towaru. Te same linie przenośników wykorzystywane są zarówno do przesyłania pojemników wewnątrz magazynu, jak i do strefy ręcznego przygotowywania zamówień. Dla zagwarantowania bezpieczeństwa przenośniki transportu ciągłego są odgrodzone metalową siatką.
Istnieje możliwość skumulowania dużej liczby pojemników przeznaczonych do magazynowania. System pozwala na nadanie pierwszeństwa oczekującym na kompletację.
Magazyn pojemnikowy na 694 tys. kg
Stricte magazynową część podzielono na dwie strefy chłodnicze. Większa z nich służy do przechowywania pojemników z gotowymi produktami, mniejsza do składowania palet z przygotowanymi zamówieniami, które nie są przeznaczone do dystrybucji bezpośrednio po zakończeniu procesu przetwórczego.
Automatyczny magazyn pojemnikowy składa się z sześciu korytarzy, z umieszczonymi po obu stronach regałami o podwójnej głębokości o wysokości 8,7 m. Każdy regał składa się z 47 modułów 17-poziomowych i dwóch modułów 14-poziomowych. Całkowita pojemność magazynu wynosi 19 848 pojemników, a maksymalna ładowność pojemnika to 35 kg (co daje w sumie 694 680 kg).
W korytarzach poruszają się układnice typu miniload, wyposażone w mechanizm wyjmujący podwójnej głębokości. Pozwala on na manewrowanie dwoma pojemnikami jednocześnie, zarówno w strefie wejść, jak i wyjść (stanowiska kompletacji i obsługi pojemników są przystosowane do przyjmowania dwóch pojemników jednocześnie).
Wejścia do korytarzy wyposażono w drzwi bezpiecznego dostępu, których otwarcie skutkuje odcięciem zasilania układnicy.
Układnica pobiera palety do wysyłki
Automatyczny magazyn paletowy składa się z jednego korytarza, w którym porusza się układnica obsługująca palety z wyrobami gotowymi do wysyłki. Zarówno wejścia, jak i wyjścia realizowane są z jednego przenośnika, który znajduje się w bocznej części strefy ręcznej kompletacji, w pobliżu punktu wejścia pustych pojemników.
Przenośnik ten łączy magazyn z częścią wspólną, która sąsiaduje z rampami załadowczymi. Na tym etapie kolejność operacji nadzoruje pracownik (wejście/wyjście), późniejsze etapy są w pełni zautomatyzowane. Magazyn paletowy mieści 288 palet. Maksymalne obciążenie palety to 700 kg.
Do ręcznej kompletacji zamówień przystosowano osiem stanowisk z dwoma przenośnikami, na których można umieścić do sześciu pojemników. By zapewnić stałą dostępność wolnych miejsc, przy nieustającej rotacji pojemników, przygotowano specjalne rozwiązania. Niewykorzystywane w danym momencie, puste pojemniki mogą być składowane w magazynie, na paletach bądź też odkładane w specjalnym miejscu przeznaczonym do tego celu, a następnie przesyłane do pakowni.
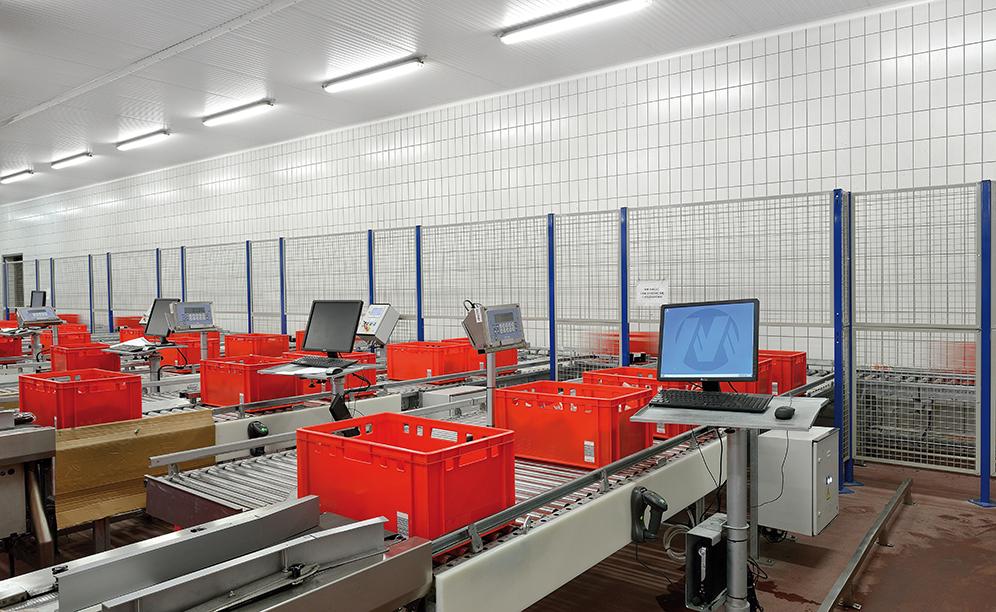
Fot. Mecalux
Zarządzający centrum logistycznym ZM Henryk Kania Easy WMS, współpracuje z oprogramowaniem Galileo. Ten ostatni steruje elementami mechanicznymi wewnątrz instalacji oraz zapewnia kontrolę nad ich działaniem. Easy WMS pozostaje również w stałej łączności z programem ERP SAP użytkownika magazynu, zapewniając przepływ informacji, kontrolę operacji oraz wymianę poleceń niezbędnych do zagwarantowania poprawnego działania magazynu.
Fot. Mecalux